Address
Unit 8 Millennium Drive
Leeds
Leeds
LS11 5BP
England UK
Opening Hours
Today
08:00-16:30
View All Hours
Sunday
Closed
Monday
08:00-16:30
Tuesday
08:00-16:30
Wednesday
08:00-16:30
Thursday
08:00-16:30
Friday
08:00-13:00
Saturday
Closed
About Spiroll Precast Services Ltd
Our approach is founded on over 40 years of technical know-how and precast manufacturing experience aligned with low overhead costs, people on the ground supporting a global customer base and an internationally proven hollowcore production system.
Products
Alongside our turnkey solutions for hollowcore, we provide a wide range of supporting products including a full range of production accessories; prestressing equipment; site safety systems and refurbished machinery.
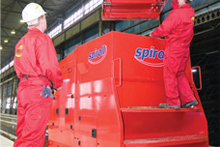
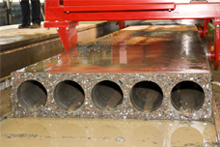
Services
We provide a comprehensive range of tailored services to support hollowcore production together with design and manufacturing support for prestressed precast concrete products.
Turnkey Plants
Spiroll deliver total solutions for start-ups and comprehensive hollowcore factories providing machinery and support that achieves a quick payback. As well as supporting a low cost entry strategy, our solutions provide provision for growth enabling manufacturers to increase production capacity in line with demand.
Even mobile hollowcore plant set-ups can be offered to manufacture directly on the construction site. This is a cost effective option which can be offered to suit large volume projects or where the remoteness of the site does not offer access to existing hollowcore manufacturers.
Start-Up Hollowcore
Spiroll can provide all the support necessary to start a hollowcore facility without having to outlay a large capital investment. The aim is to have a staged investment with progressive development funded from the sales and future market growth of product.
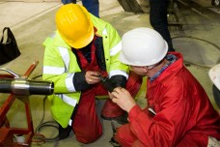
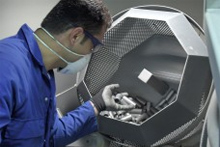
Comprehensive Hollowcore
Spiroll provides efficient, cost effective, comprehensive hollowcore factories. Our skill is providing machinery and support for projects with a good pay back. We have people on the ground, an internationally proven hollowcore production system and 40 years of know-how and manufacturing experience.
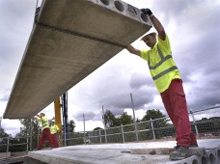
Products
Alongside our turnkey solutions for hollowcore, we provide a wide range of supporting products including a full range of production accessories; prestressing equipment; site safety systems and refurbished machinery.
- Hollowcore Production
- Prestressing Systems
- Site Safety Systems
- 2nd Hand Machinery
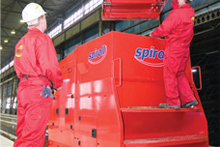
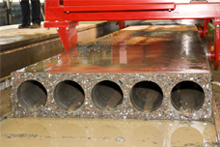
Services
We provide a comprehensive range of tailored services to support hollowcore production together with design and manufacturing support for prestressed precast concrete products.
- Prestressing Training
- Consultancy Services
- Stressing Services
Turnkey Plants
Spiroll deliver total solutions for start-ups and comprehensive hollowcore factories providing machinery and support that achieves a quick payback. As well as supporting a low cost entry strategy, our solutions provide provision for growth enabling manufacturers to increase production capacity in line with demand.
Even mobile hollowcore plant set-ups can be offered to manufacture directly on the construction site. This is a cost effective option which can be offered to suit large volume projects or where the remoteness of the site does not offer access to existing hollowcore manufacturers.
Start-Up Hollowcore
Spiroll can provide all the support necessary to start a hollowcore facility without having to outlay a large capital investment. The aim is to have a staged investment with progressive development funded from the sales and future market growth of product.
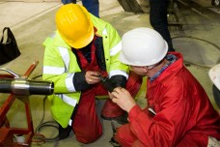
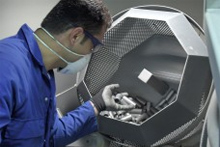
Comprehensive Hollowcore
Spiroll provides efficient, cost effective, comprehensive hollowcore factories. Our skill is providing machinery and support for projects with a good pay back. We have people on the ground, an internationally proven hollowcore production system and 40 years of know-how and manufacturing experience.
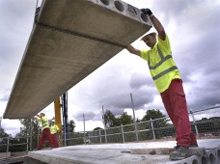
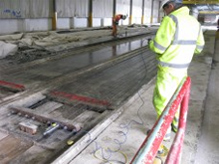
Gallery
Videos
News
Acheson + Glover (A+G), precast and hollowcore concrete specialist and long-standing Spiroll customer, has invested in the Spiroll Concrete Aspirator – to further enhance its efficiencies in hollowcore slab production at its Ballygawley site in County Tyrone.
The Concrete Aspirator is the newest addition to Spiroll’s fleet of precast production machinery and is designed to reduce the manual labour in slab detailing as well as ensuring accuracy and consistency of the product.
A+G’s Ballygawley site has 11 casting beds and currently produces 316,000 m2 of hollowcore slabs per year. The new machine will enable the company to respond to the growing demands for hollow core slab detailing and offers the potential to increase the plant’s production capacity because of the reduction in the onerous amounts of manual labour required.
https://spiroll.co.uk/news/hollowcore-slab-detailing-demands-answered-by-spirolls-concrete-aspirator/
The Concrete Aspirator is the newest addition to Spiroll’s fleet of precast production machinery and is designed to reduce the manual labour in slab detailing as well as ensuring accuracy and consistency of the product.
A+G’s Ballygawley site has 11 casting beds and currently produces 316,000 m2 of hollowcore slabs per year. The new machine will enable the company to respond to the growing demands for hollow core slab detailing and offers the potential to increase the plant’s production capacity because of the reduction in the onerous amounts of manual labour required.
https://spiroll.co.uk/news/hollowcore-slab-detailing-demands-answered-by-spirolls-concrete-aspirator/
Spiroll has introduced three new machines to its precast equipment range designed to improve production processes, minimise manual labour and reduce costs.
An efficient and cost-effective solution to hollowcore slab detailing, the Spiroll Detailing Machine is a significant advancement on the basic wet-cut saw and is designed to make longitudinal cuts in green concrete immediately after casting. The machine is equipped with a 0.5 m3 mixer complete with a chute to place the wet concrete. Further options include a weep hole drilling head and a cover roller.
The Spiroll Concrete Aspirator is designed to reduce the manual labour in hollowcore slab detailing. It is a vacuum suction machine which removes concrete from green slabs immediately after casting using a suction nozzle. The nozzle is equipped with a waterjet which emulsifies the concrete before it can be removed and has push-button controls to allow the operator to move forward and back without interrupting the operation when concrete is removed.
Used to create water drainage holes in hollowcore slabs the Spiroll Weep Hole Driller achieves maximum efficiency during the slab production process. The drilling operation is carried out as part of the bed stripping process to minimise double handling of the slab. The weep hole driller has an automated cut sequence that drastically reduces costs associated with performing these tasks manually.
https://spiroll.co.uk/news/spirolls-latest-precast-machines-deliver-efficiencies-in-hollowcore-slab-production/
An efficient and cost-effective solution to hollowcore slab detailing, the Spiroll Detailing Machine is a significant advancement on the basic wet-cut saw and is designed to make longitudinal cuts in green concrete immediately after casting. The machine is equipped with a 0.5 m3 mixer complete with a chute to place the wet concrete. Further options include a weep hole drilling head and a cover roller.
The Spiroll Concrete Aspirator is designed to reduce the manual labour in hollowcore slab detailing. It is a vacuum suction machine which removes concrete from green slabs immediately after casting using a suction nozzle. The nozzle is equipped with a waterjet which emulsifies the concrete before it can be removed and has push-button controls to allow the operator to move forward and back without interrupting the operation when concrete is removed.
Used to create water drainage holes in hollowcore slabs the Spiroll Weep Hole Driller achieves maximum efficiency during the slab production process. The drilling operation is carried out as part of the bed stripping process to minimise double handling of the slab. The weep hole driller has an automated cut sequence that drastically reduces costs associated with performing these tasks manually.
https://spiroll.co.uk/news/spirolls-latest-precast-machines-deliver-efficiencies-in-hollowcore-slab-production/
Spiroll engineers have used innovative 3D printing technology in a bespoke cooling system for the company’s Vortex Extruder to enhance its performance in very hot climates.
The usual solution to regulate heat generated by electrical systems used in industrial plant is to draw in surrounding air to cool the system. However, in some situations the air is too warm to provide effective cooling of the electrical components. To overcome this problem, Spiroll has designed a new cooling system for its Vortex Extruder, specifically for use in hot climates.
Location of the ducting within the cooling system required a number of custom-made components which would fit the compact design of the extruder. Spiroll was able to 3D print the parts at its Leeds production facility tailoring the items specifically to suit the available space.
https://spiroll.co.uk/news/3d-printed-components-for-spirolls-vortex-extruder/
The usual solution to regulate heat generated by electrical systems used in industrial plant is to draw in surrounding air to cool the system. However, in some situations the air is too warm to provide effective cooling of the electrical components. To overcome this problem, Spiroll has designed a new cooling system for its Vortex Extruder, specifically for use in hot climates.
Location of the ducting within the cooling system required a number of custom-made components which would fit the compact design of the extruder. Spiroll was able to 3D print the parts at its Leeds production facility tailoring the items specifically to suit the available space.
https://spiroll.co.uk/news/3d-printed-components-for-spirolls-vortex-extruder/
A hollowcore slab manufacturer in India has saved an estimated US $100,000 in raw material costs after investing in the Spiroll Vortex Extruder.
Teemage Precast is part of the Chennai Silks Group of companies and supplies precast concrete slabs for a wide range of projects and contractors across India.
Having opted for a slipformer machine for its first venture into hollow core slab production at its Tirrupur factory, the company invested in the Vortex to exploit the greater efficiencies provided by a high frequency vibration extruder. Teemage has recently tripled its production capacity, and the purchase of Spiroll machinery has allowed them to fast track set up of a new plant in Delhi.
Teemage chose the Vortex Extruder because of Spiroll’s engineering expertise in hollowcore production machinery backed by the global capabilities of parent company CCL, as well as the value for money offered by the machine and the excellent levels of customer service.
The raw material savings are the result of two key features of the Vortex Extruder; Dynacore high frequency vibration, facilitating a mix with lower cement content than other machines; and a mandrel drive with static follower tube, which produces Spiroll slabs with highly efficient profiles.
https://spiroll.co.uk/news/spirolls-vortex-extruder-takes-on-india/
Teemage Precast is part of the Chennai Silks Group of companies and supplies precast concrete slabs for a wide range of projects and contractors across India.
Having opted for a slipformer machine for its first venture into hollow core slab production at its Tirrupur factory, the company invested in the Vortex to exploit the greater efficiencies provided by a high frequency vibration extruder. Teemage has recently tripled its production capacity, and the purchase of Spiroll machinery has allowed them to fast track set up of a new plant in Delhi.
Teemage chose the Vortex Extruder because of Spiroll’s engineering expertise in hollowcore production machinery backed by the global capabilities of parent company CCL, as well as the value for money offered by the machine and the excellent levels of customer service.
The raw material savings are the result of two key features of the Vortex Extruder; Dynacore high frequency vibration, facilitating a mix with lower cement content than other machines; and a mandrel drive with static follower tube, which produces Spiroll slabs with highly efficient profiles.
https://spiroll.co.uk/news/spirolls-vortex-extruder-takes-on-india/
Following the relocation of Spiroll manufacturing operations to CCL’s premises in Leeds, more exciting developments have taken place with the addition of a new 10-tonne overhead crane. Over the last three months, continued improvements have transformed Spiroll’s dedicated manufacturing area, and the installation of the new crane will further enhance Spiroll’s efficiency in the production of precast concrete machinery.
The crane, which has been installed this week, stands six metres high and spans 18 m. It will improve production processes, and speed up workflow in the factory. With the Vortex hollowcore slab extruder weighing in at over 4 tonnes, the new crane will facilitate the safe manoeuvring of heavy plant machinery and parts.
https://spiroll.co.uk/news/2017/06/
The crane, which has been installed this week, stands six metres high and spans 18 m. It will improve production processes, and speed up workflow in the factory. With the Vortex hollowcore slab extruder weighing in at over 4 tonnes, the new crane will facilitate the safe manoeuvring of heavy plant machinery and parts.
https://spiroll.co.uk/news/2017/06/
As part of our continued growth strategy since becoming part of the CCL group, Spiroll has relocated manufacturing operations to CCL’s 33,000 ft2 production facility in Leeds. The move will allow us to offer greater efficiencies and higher levels of service to our customers throughout the world.
The relocation completes a programme of systems integration aligning Spiroll’s processes with CCL’s business across a wide range of commercial and operational areas, including manufacturing, procurement, stock control and order processing. The careful preparation on the part of both companies has allowed us to drive enhanced efficiency and high standards of customer service from day one of the new operation in Leeds.
As well as supporting our international growth strategy, the move allows us to draw on our parent company’s resources as we continue to facilitate more efficient precast concrete production for our customers worldwide.
https://spiroll.co.uk/news/production-expands-to-leeds/
The relocation completes a programme of systems integration aligning Spiroll’s processes with CCL’s business across a wide range of commercial and operational areas, including manufacturing, procurement, stock control and order processing. The careful preparation on the part of both companies has allowed us to drive enhanced efficiency and high standards of customer service from day one of the new operation in Leeds.
As well as supporting our international growth strategy, the move allows us to draw on our parent company’s resources as we continue to facilitate more efficient precast concrete production for our customers worldwide.
https://spiroll.co.uk/news/production-expands-to-leeds/
The Crosscut Saw is specifically designed for cutting 90 degree crosscuts in the hollowcore slabs. It provides a fast, reliable and economical cutting solution. The standard saw cuts up to 400mm deep hollowcore but we also provide a conversion kit for slabs up to 500mm deep. It is very easy set the saw to use a range of diamond blades from 900mm to 1300mm in diameter. This ensures you use the optimum blade depending on the maximum depth of precast product.The operator sits on a sprung seat in the cabin and controls all the movements by means of two pilot operated hydraulic joysticks which maximise comfort and provide close control. The operator has a clear unobstructed view of the cutting point on the slab.There is also a laser marker which projects a line on the cutting point on the slab. These features make it easier for the operator to line the blade and cut the required angle in the slab.
The saw can also be supplied complete with two optional hydraulic cable reelers for power and water. Each reeler would be supplied complete with 130 metres of cable/hose as standard (maximum length 180 metres). The saw head operates on a precision slide way movement running on the same linear bearing rails used in CNC milling machines. There is a highly efficient blade drive mechanism as the motor is mounted directly on the cutting head. This allows high precision movement; minimal vibration minimises the reduction in lose of energy due to friction and inefficiencies in power transmission. Our saws are designed to be used in an aggressive working environment. The blade head mechanism is up in the air away from the cutting point so that no spray and contaminates can get in the moving parts. The saws are very efficient and have a fast driving and cutting speed. They are extremely robust; very easy to maintain and can be designed/built to work in conjunction with any existing type of casting bed.
The saw can also be supplied complete with two optional hydraulic cable reelers for power and water. Each reeler would be supplied complete with 130 metres of cable/hose as standard (maximum length 180 metres). The saw head operates on a precision slide way movement running on the same linear bearing rails used in CNC milling machines. There is a highly efficient blade drive mechanism as the motor is mounted directly on the cutting head. This allows high precision movement; minimal vibration minimises the reduction in lose of energy due to friction and inefficiencies in power transmission. Our saws are designed to be used in an aggressive working environment. The blade head mechanism is up in the air away from the cutting point so that no spray and contaminates can get in the moving parts. The saws are very efficient and have a fast driving and cutting speed. They are extremely robust; very easy to maintain and can be designed/built to work in conjunction with any existing type of casting bed.
The Spiroll Multi-Angle Saw is designed for cutting the slabs directly on the production beds. The saw can cut any angle from 0-90 degrees in the hollowcore slabs. It can perform large skews and shallow off sets and also drive long cuts/rips down the entire length of the slab.
The saws are designed to be used in an aggressive working environment. They are extremely robust and very easy to maintain with off the shelf spare parts. The frames are strong and give excellent stability which is very important to maximise blade life.The operator sits on a sprung seat in the cabin and controls all the movements by means of two pilot operated hydraulic joysticks which maximise comfort and provide close control. The operator has a clear unobstructed view of the cutting point on the slab.
The blade head mechanism is up in the air away from the cutting point so that no spray and contaminants can get in the moving parts. All the hydraulic and electrical components are easy to access which also helps with minimal maintenance downtime.The saw head operates on a precision slide way movement running on the same linear bearing rails used in CNC milling machines. The saw head cuts using a vertical plunge movement. This allows high precision movement; minimal vibration and minimses the distance required between the casting beds.
To ensure accurate cutting we have a digital encoder accurate with in +/- 0.1 degrees giving the required angle on a digital readout within the control cabin. There is also a laser marker which projects a line on the cutting point on the slab. These features make it easier for the operator to line the blade and cut the required angle in the slab.
The saws are very efficient and have a fast driving and cutting speed. There is a highly efficient blade drive mechanism as the blade drive motor is mounted directly on the cutting head. This minimises the reduction in lose of energy due to friction and inefficiencies in power transmission.The saws can be easily set-up to be used with a range of diamond blades from 800mm – 1300mm in diameter. This ensures you use the optimum blade depending on the maximum depth of precast product.
The saw has a CCTV system so that the operator can see in front of the hydraulic cable reels where the view is restricted.
The saw can also be supplied complete with two hydraulic cable reelers for power and water. Each reeler would be supplied complete with 130 metres of cable/hose as standard (maximum length 180 metres).The saw can be designed/built to work in conjunction with any existing type of casting bed.
The saws are designed to be used in an aggressive working environment. They are extremely robust and very easy to maintain with off the shelf spare parts. The frames are strong and give excellent stability which is very important to maximise blade life.The operator sits on a sprung seat in the cabin and controls all the movements by means of two pilot operated hydraulic joysticks which maximise comfort and provide close control. The operator has a clear unobstructed view of the cutting point on the slab.
The blade head mechanism is up in the air away from the cutting point so that no spray and contaminants can get in the moving parts. All the hydraulic and electrical components are easy to access which also helps with minimal maintenance downtime.The saw head operates on a precision slide way movement running on the same linear bearing rails used in CNC milling machines. The saw head cuts using a vertical plunge movement. This allows high precision movement; minimal vibration and minimses the distance required between the casting beds.
To ensure accurate cutting we have a digital encoder accurate with in +/- 0.1 degrees giving the required angle on a digital readout within the control cabin. There is also a laser marker which projects a line on the cutting point on the slab. These features make it easier for the operator to line the blade and cut the required angle in the slab.
The saws are very efficient and have a fast driving and cutting speed. There is a highly efficient blade drive mechanism as the blade drive motor is mounted directly on the cutting head. This minimises the reduction in lose of energy due to friction and inefficiencies in power transmission.The saws can be easily set-up to be used with a range of diamond blades from 800mm – 1300mm in diameter. This ensures you use the optimum blade depending on the maximum depth of precast product.
The saw has a CCTV system so that the operator can see in front of the hydraulic cable reels where the view is restricted.
The saw can also be supplied complete with two hydraulic cable reelers for power and water. Each reeler would be supplied complete with 130 metres of cable/hose as standard (maximum length 180 metres).The saw can be designed/built to work in conjunction with any existing type of casting bed.
The Universal Extruder is the heart of our hollowcore production system. Its unique design ensures that production is low cost, extremely reliable and the finished hollowcore is of the highest quality. The functional design means it very easy to use, set-up and maintain.The Extruder is unique as it works with auger drive combined with a 9000rpm high frequency vibration system. It produces hollowcore slabs with early strengths; consistent high quality finishes; low cement content; high load bearing capacities; excellent strand bond and low camber.
The Extruder requires one man to run the machine on the production bed and once it has been set-up correctly it simply requires the mix to be put in the hopper to begin production.
The extruder can manufacture the full range of hollowcore slab depths from 150mm (6”) to 400mm (16”). The unique quick change power unit takes just 5 minutes to swap from one cassette depth to another. The extruder makes hollowcore slabs suitable for both floor and wall panel applications.The machine comes with an independent wire/strand guide trolley to ensure correct positioning of prestress wires/strands and reduces resistance to movement ultimately improving finished product quality and increasing the working life of wearing components in the compaction chamber.
The same effort that feeds the concrete mix through the machine and forms it into the final precast slab also provides the motivation to drive the extruder along the bed. This natural process propels the extruder along the casting bed and allows the compacted concrete to reach the required density.The Spiroll system uses an extremely dry concrete mix and less cement than other machines (typically a water/cement ratio of approximately 0.3). Due to the intense high frequency vibrations and pressure within the machine the concrete mix is 'plasticised' during the short time that it is passed through the extruder which allows it to be moulded and formed into the required section. The formed slab then reverts to its 'dry' state and reaches such a high density that it is possible to stand on the slab immediately after the extrusion process. After a period of natural or accelerated curing, the slabs are then cut to length, stripped from the casting bed and transported to the storage area.The casting beds are then cleaned, a release agent is applied and high tensile steel strands are located in position for the automatic extrusion process to begin again. Normally the entire production takes place over a 24-hour cycle.
The Extruder requires one man to run the machine on the production bed and once it has been set-up correctly it simply requires the mix to be put in the hopper to begin production.
The extruder can manufacture the full range of hollowcore slab depths from 150mm (6”) to 400mm (16”). The unique quick change power unit takes just 5 minutes to swap from one cassette depth to another. The extruder makes hollowcore slabs suitable for both floor and wall panel applications.The machine comes with an independent wire/strand guide trolley to ensure correct positioning of prestress wires/strands and reduces resistance to movement ultimately improving finished product quality and increasing the working life of wearing components in the compaction chamber.
The same effort that feeds the concrete mix through the machine and forms it into the final precast slab also provides the motivation to drive the extruder along the bed. This natural process propels the extruder along the casting bed and allows the compacted concrete to reach the required density.The Spiroll system uses an extremely dry concrete mix and less cement than other machines (typically a water/cement ratio of approximately 0.3). Due to the intense high frequency vibrations and pressure within the machine the concrete mix is 'plasticised' during the short time that it is passed through the extruder which allows it to be moulded and formed into the required section. The formed slab then reverts to its 'dry' state and reaches such a high density that it is possible to stand on the slab immediately after the extrusion process. After a period of natural or accelerated curing, the slabs are then cut to length, stripped from the casting bed and transported to the storage area.The casting beds are then cleaned, a release agent is applied and high tensile steel strands are located in position for the automatic extrusion process to begin again. Normally the entire production takes place over a 24-hour cycle.