Construction News
25/11/2009
Extechnology Presents Low Carbon Odour And Grease Control Technology
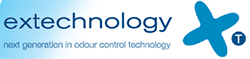
Extechnology's patented EXE 12 UV-C technology is designed to offer a low carbon solution to the rising number of complaints regarding nuisance odours from commercial kitchen extract systems.
With the EXE 12 unit's UV-C tubes mounted outside the ductwork the tubes pose no resistance to air flow allowing air movement systems to maintain their efficiency.
Used in a variety of air cleaning applications for more than 20 years, UV-C technology works by oxidising the odour and grease particulate, permanently destroying and altering the compounds. Comprising 12 UV-C tubes, the Extechnology EXE 12 unit controls odour and grease by producing ozone a powerful oxidant which interacts with most pollutants such as odour, bacteria, mould, mildew and grease.
The unit is specially designed to maximise the generation of ozone through its UV-C tubes in combination with the EXE 12’s patented titanium plated walls. The ozone produced in the Extechnology unit is introduced into the extract system and a breakdown of the polluted molecules results in permanent oxidation and a conversion of the grease and odour molecules into harmless compounds, such as water vapour and carbon dioxide.
"Extract systems are one of the largest energy consumers in commercial kitchens. In the current financial climate, restaurants and hotels are increasingly focusing on operating costs which is driving them away from using carbon filters which demand larger energy consuming fans to drive kitchen extract systems. Carbon filters also need to be replaced on a monthly basis which can prove expensive, possibly upwards of £500 a month. In contrast the only maintenance required by our EXE 12 system is tube replacement every 8000 hours or once a year," explained Cian Flood, Director at Extechnology.
The major difference with the patented Extechnology application when compared to other traditional inline UV-C units on the market, is that the UV-C tubes are mounted outside the ductwork or canopy in a separate, self-contained chamber. This chamber is linked to the kitchen extract ductwork or canopy via two spigots 90mm in length and 20mm in diameter.
The location of the UV-C tubes outside the ductwork makes the unit significantly easier to install than inline applications, especially when retrofitting.
Extechnology's EXE 12 is also very low in maintenance only requiring tube replacement every 8000 hours or once a year. In contrast traditional inline applications require rigorous cleaning regimes once fitted since the tubes sit in air laden with cooking effluent and so the grease tends to adhere to their surface impairing performance.
In addition, the EXE 12 unit reduces the grease build up in a duct by up to 85% and in conjunction with traditional methods of maintenance can drastically reduce the risk of a duct fire as well as maintain the efficiencies of the air movement system.
"Odour from the kitchen extract is an issue for many commercial kitchens. However, grease is also a problem since insurers demand rigorous cleaning regimes to keep ductwork grease free, this can be an issue in all day restaurants or hotels where service is demanded 24-7. For this reason Extechnology’s EXE unit is an ideal solution since the ozone generated by the unit breaks down odour, bacteria and grease. As result the need for ductwork cleaning is significantly reduced," added Cian Flood.
Extechnology units are constructed entirely from 1.2mm (18g) grade 304 satin-finish stainless steel, all-welded fabrication. Rugged construction allows the EXE 12 to cope with harsh conditions in the field.
Extechnology has developed a unique UV-C application which overcomes many of the barriers preventing traditional UV-C technology from operating effectively. The Extechnology UV unit sits outside the airflow and is attached to a canopy or duct via two connecting spigots.
The Extechnology process works through the production of ozone. The Extechnology UV tubes are specially designed to maximise the generation of ozone. (Ozone is a powerful oxidant which interacts with most pollutants such as odour, bacteria, mould, mildew and grease.) The ozone produced in the Extechnology unit is introduced into the extract system and a breakdown of the polluted molecules results in permanent oxidation and a conversion of the grease and odour molecules into harmless compounds such as water vapour and carbon dioxide.
For further information visit: www.extechnology.com
With the EXE 12 unit's UV-C tubes mounted outside the ductwork the tubes pose no resistance to air flow allowing air movement systems to maintain their efficiency.
Used in a variety of air cleaning applications for more than 20 years, UV-C technology works by oxidising the odour and grease particulate, permanently destroying and altering the compounds. Comprising 12 UV-C tubes, the Extechnology EXE 12 unit controls odour and grease by producing ozone a powerful oxidant which interacts with most pollutants such as odour, bacteria, mould, mildew and grease.
The unit is specially designed to maximise the generation of ozone through its UV-C tubes in combination with the EXE 12’s patented titanium plated walls. The ozone produced in the Extechnology unit is introduced into the extract system and a breakdown of the polluted molecules results in permanent oxidation and a conversion of the grease and odour molecules into harmless compounds, such as water vapour and carbon dioxide.
"Extract systems are one of the largest energy consumers in commercial kitchens. In the current financial climate, restaurants and hotels are increasingly focusing on operating costs which is driving them away from using carbon filters which demand larger energy consuming fans to drive kitchen extract systems. Carbon filters also need to be replaced on a monthly basis which can prove expensive, possibly upwards of £500 a month. In contrast the only maintenance required by our EXE 12 system is tube replacement every 8000 hours or once a year," explained Cian Flood, Director at Extechnology.
The major difference with the patented Extechnology application when compared to other traditional inline UV-C units on the market, is that the UV-C tubes are mounted outside the ductwork or canopy in a separate, self-contained chamber. This chamber is linked to the kitchen extract ductwork or canopy via two spigots 90mm in length and 20mm in diameter.
The location of the UV-C tubes outside the ductwork makes the unit significantly easier to install than inline applications, especially when retrofitting.
Extechnology's EXE 12 is also very low in maintenance only requiring tube replacement every 8000 hours or once a year. In contrast traditional inline applications require rigorous cleaning regimes once fitted since the tubes sit in air laden with cooking effluent and so the grease tends to adhere to their surface impairing performance.
In addition, the EXE 12 unit reduces the grease build up in a duct by up to 85% and in conjunction with traditional methods of maintenance can drastically reduce the risk of a duct fire as well as maintain the efficiencies of the air movement system.
"Odour from the kitchen extract is an issue for many commercial kitchens. However, grease is also a problem since insurers demand rigorous cleaning regimes to keep ductwork grease free, this can be an issue in all day restaurants or hotels where service is demanded 24-7. For this reason Extechnology’s EXE unit is an ideal solution since the ozone generated by the unit breaks down odour, bacteria and grease. As result the need for ductwork cleaning is significantly reduced," added Cian Flood.
Extechnology units are constructed entirely from 1.2mm (18g) grade 304 satin-finish stainless steel, all-welded fabrication. Rugged construction allows the EXE 12 to cope with harsh conditions in the field.
Extechnology has developed a unique UV-C application which overcomes many of the barriers preventing traditional UV-C technology from operating effectively. The Extechnology UV unit sits outside the airflow and is attached to a canopy or duct via two connecting spigots.
The Extechnology process works through the production of ozone. The Extechnology UV tubes are specially designed to maximise the generation of ozone. (Ozone is a powerful oxidant which interacts with most pollutants such as odour, bacteria, mould, mildew and grease.) The ozone produced in the Extechnology unit is introduced into the extract system and a breakdown of the polluted molecules results in permanent oxidation and a conversion of the grease and odour molecules into harmless compounds such as water vapour and carbon dioxide.
For further information visit: www.extechnology.com
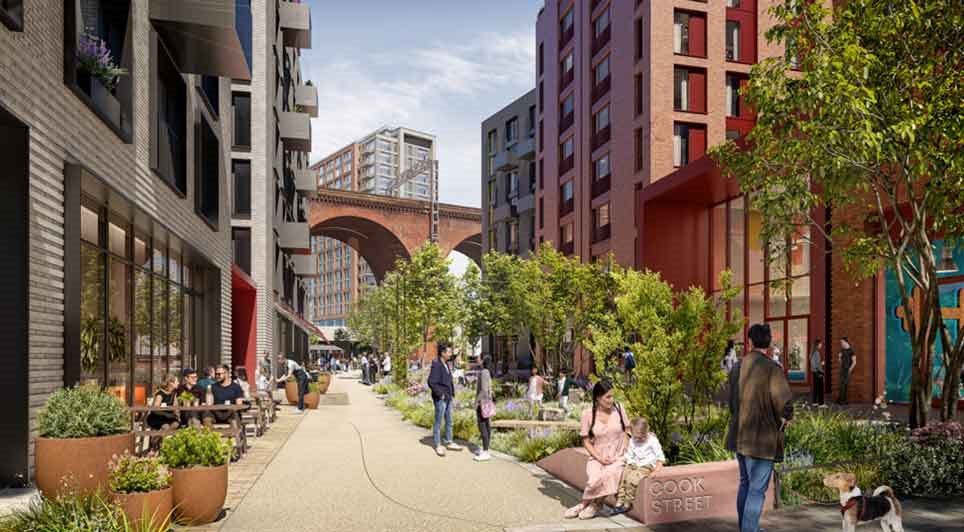
05/02/2025
Stockport Mayoral Development Corporation (MDC) and ECF, a joint venture between Homes England, Legal & General, and Muse, have selected Vinci as the preferred contractor for Phase 1 of Stockport 8, a £350 million residential development west of Stockport town centre.
The decision follows a competi
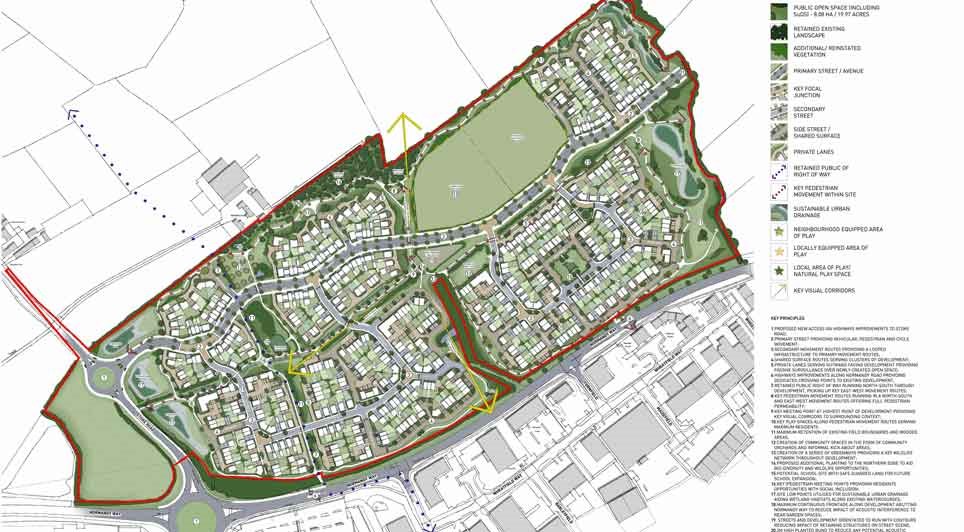
05/02/2025
Vistry Group has finalised contracts for a significant housing development in Hinckley, Leicestershire, securing outline planning permission to deliver 475 new homes in the area.
The development, located east of Stoke Road and north of Normandy Way in the town's northern region, has a projected val
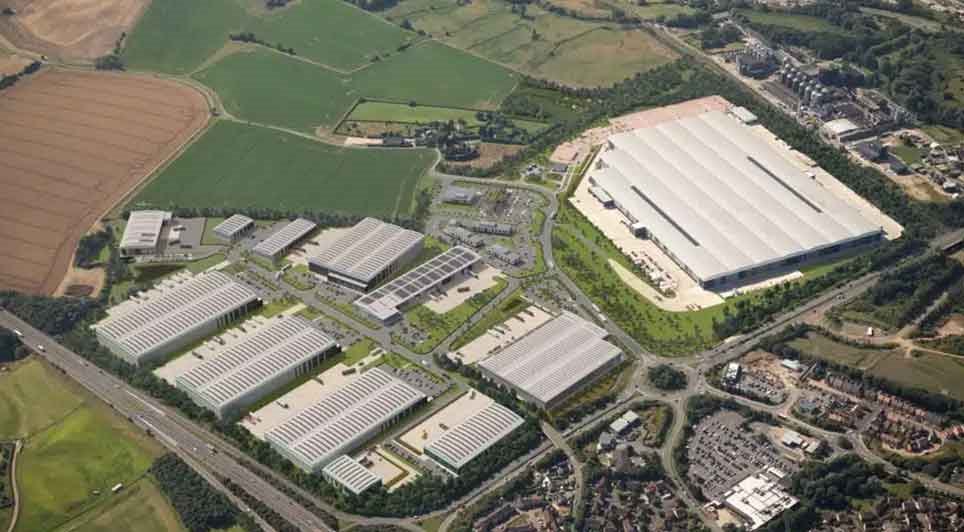
05/02/2025
Wilten Construction has been awarded a second Design and Build contract at Gateway 14 by client Gateway 14 Ltd and Jaynic.
The project involves the development of a state-of-the-art, three-storey Skills and Innovation Centre spanning 35,000 sq ft in the heart of Gateway 14. Designed to achieve BREE
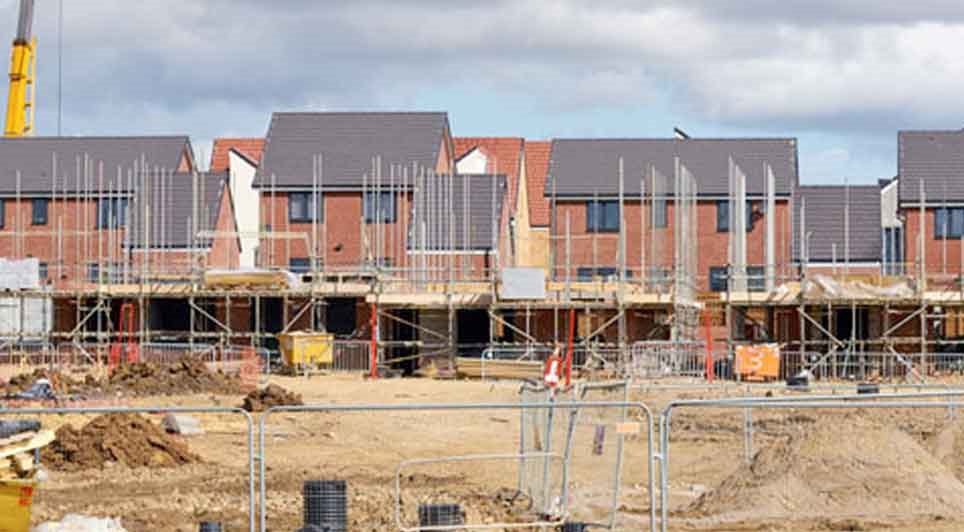
05/02/2025
Knowsley Council has approved a major housing development in Kirkby, giving the green light to 800 new energy-efficient homes in the town's centre.
The decision also secures £7.7 million in Section 106 contributions from developer Barratt David Wilson Homes, further boosting local investment.
The
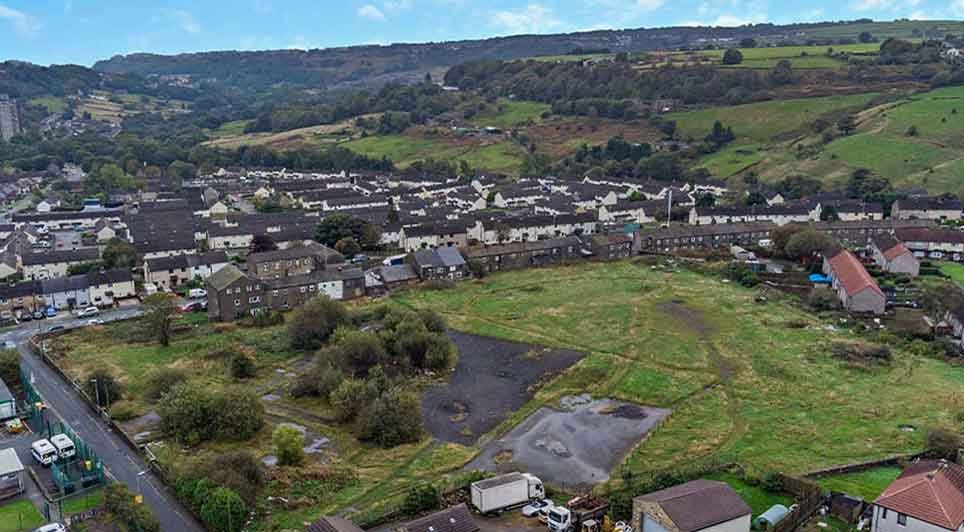
05/02/2025
Keepmoat Homes has announced plans to invest over £50 million in three new housing developments across Calderdale, aiming to deliver more than 200 new homes.
The developments, undertaken in partnership with Calderdale Council, form part of the North Halifax Transformation Programme, a local authori
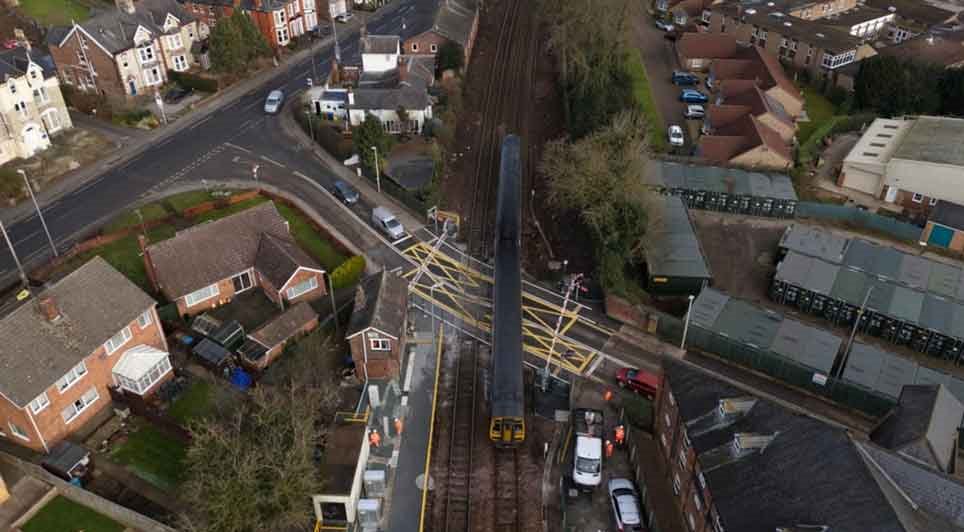
05/02/2025
Essential renewal work at Skerne Road level crossing in Driffield has been completed. Over a six-day period, engineers replaced decades-old equipment, installing a state-of-the-art operating system, replacing the level crossing deck, and resurfacing the road.
The newly installed operating system is
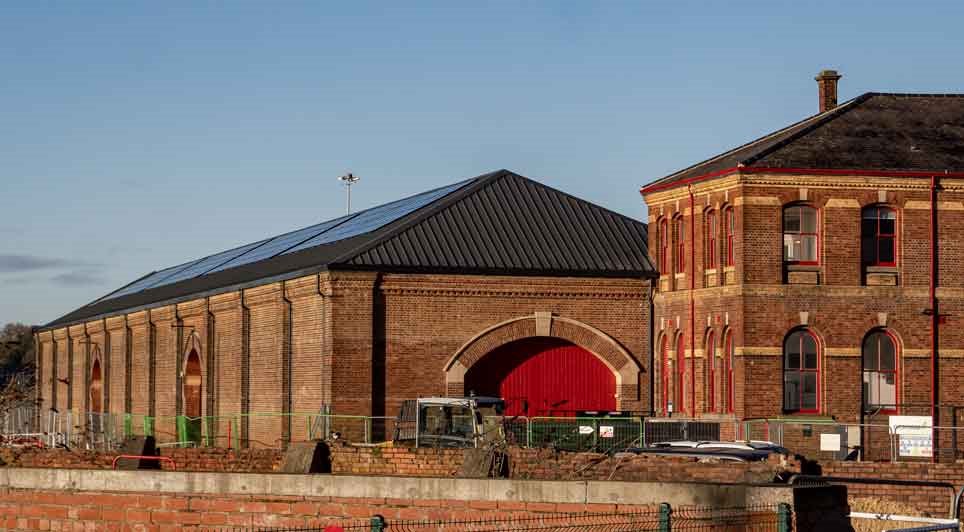
05/02/2025
Construction firm GRAHAM is currently carrying out essential restoration work at the National Railway Museum in York, replacing the Grade II listed roof structure at Station Hall.
Originally built between 1875 and 1877 as a goods station, Station Hall now houses the museum’s six royal carriages.
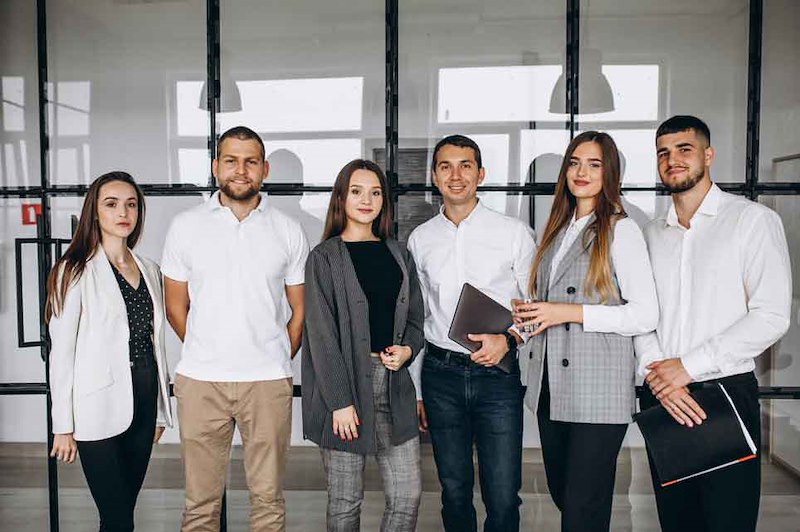
05/02/2025
Mezzanine floors are commonly associated with additional storage or expanded floor space, but did you know they can also have a profound impact on employee productivity and morale? At Doity Engineering, we specialise in designing and installing mezzanine floors for
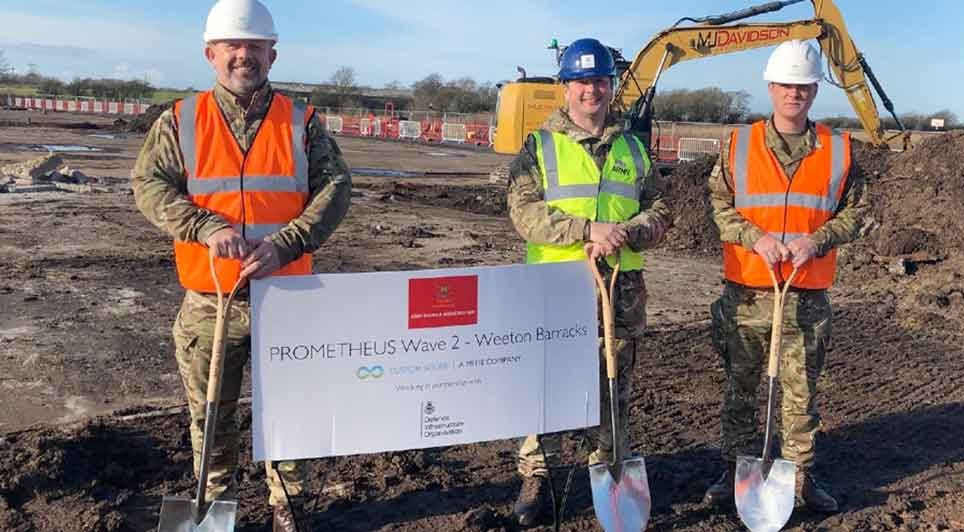
05/02/2025
Construction work is commencing on a new solar array at Weeton Barracks in Lancashire that will generate over one third of the site’s energy needs.
The work has been funded under the British Army’s Project Prometheus, a scheme that is increasing renewable energy across the army estate through inst
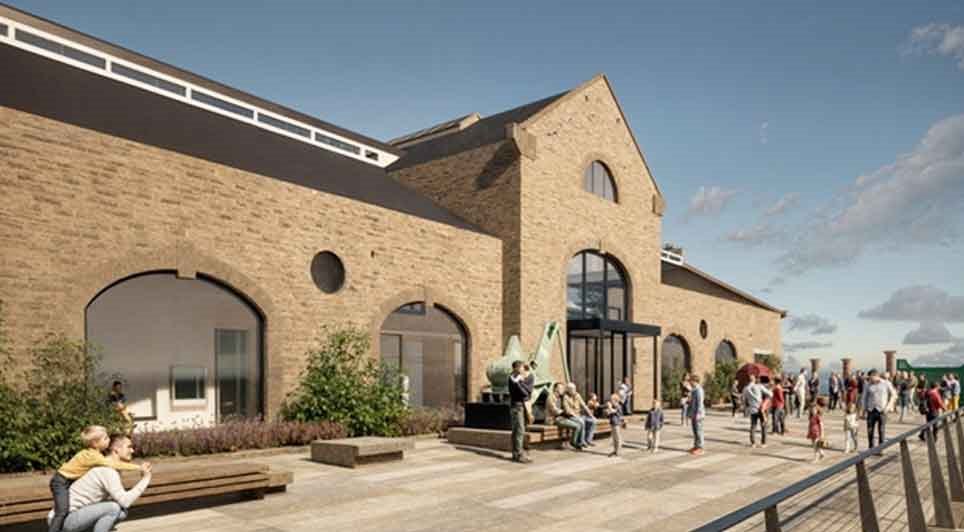
05/02/2025
The regeneration of Hartlepool's waterfront has reached a significant milestone with a £631,000 grant from The National Lottery Heritage Fund.
The funding will support the development phase of the 'Tides of Change' project, aimed at transforming the visitor experience at the Museum of Hartlepool a