RMD Kwikform pulled out all the stops to win a contract from Bouygues Travaux Publics and Dunne Building & Civil Engineering for the Tyne Tunnel, creating a unique concept for a 21 metre long, 60 tonne falsework traveller system - in just 7 days.
For formwork and falsework specialist RMD Kwikform, given 7 days to go back to the drawing board, following an unsuccessful bid for an important contract on the Tyne Tunnel, led to the conception of the company’s most innovative travelling tunnel soffit support system to date.
Having secured the deal through Concessionaire TT2's main Design and Build Contractor Bouygues Travaux Publics at the final hour, engineers teamed up with North tunnel section subcontractor, Dunne Building & Civil Engineering, combining expertise to successfully utilise the unique traveller system.
Travelling on the equivalent of train tracks, the RMD Kwikform traveller used a combination of specially designed and standard equipment to create a solid yet flexible structure, capable of snaking up an incline of 6%. Withstanding loads of up to 750 tonnes the traveller was capable of supporting up to 300 cubic metres of concrete poured over 173 square metres.
The 21m long traveller system was used by Dunne Civil Engineering to successfully cast the nine, 1200mm thick roof slabs that make up the roof of the tunnel’s North section for the Tyne Tunnel operator, TT2 who, together with Project Promoter the Tyne and Wear Integrated Transport Authority (TWITA), funded £260m project.
For RMD Kwikform Engineering Director, Ian Fryer who led the four strong engineering design team for the project, overcoming the challenges faced at both the design and utilisation stages of the project were particularly rewarding.
Ian said: "When you are challenged to go back to the drawing board on a project of this scale and importance, it tests all of your engineering knowledge and capabilities.
"The challenge was to deliver a whole-slab-area travelling formwork system with 2 metre height variation which could be operated without the site staff working at height. The traveller also needed to give the users the flexibility to snake the equipment up an incline of 6%, travelling on rails whilst casting a slab that was up to 8.5 metres off the ground, at the bottom of a 25 metre deep excavation full of large ground shoring props.
"Once we had overcome the design element and been awarded the contract by Bouygues Travaux Publics, we entered the phase of taking the proposal design to the end solution. At this time, because the works for the North contract were subcontracted to Dunne Civil Engineering, we had to deal with a new construction team to demonstrate how the system would work.
"At this stage Dunne's were able to assist the design team with suggested amends to the design in order for the system to best meet the needs of the site team. The very tight programme schedule also placed further challenges on the delivery and erection of equipment, which physically required assembling and commissioning 60 tonnes of system and special components at the base of what is effectively a large hole.
"As part of the intensive design and detailing phase that followed, the first thing the team concentrated on was the calculations, detailing, procurement and fabrication of the special items of equipment needed for the project. Shortly followed by production of the general arrangement drawings required for assembly and the detailed instructions for use of the machine.
"Procurement of the special equipment, (which included the hydraulic leg components that were central to the function of the traveller), ultimately determined whether the system could be assembled and operated within the time frame required."
Having developed an assembly sequence in collaboration with Dunne’s for the traveller, RMD Kwikform provided three customer service team members to assist with the erection of the traveller which as a part of the design required the support legs to always be perpendicular to the slope of the soffit.
Unlike previous travellers designed by RMD Kwikform, which incorporated structural steel work at the soffit level, the RMD Kwikform engineering team recognised the opportunity to adapt its R700 truss girder panels for use on this project. By adapting the R700 girders with specially fabricated cantilever frames at the ends, the units were used to span across the tunnel whilst still maintaining sufficient headroom beneath to accommodate site traffic, such as concrete mixers and scissor lifts.
Having to negotiate both varying horizontal and vertical curves, the 21 metre long traveller had to be flexible enough to be able to be travelled around the tunnel profile, rising from its start point at the river side end wall. For this reason RMD Kwikform split the structure into three 7.2m long rectangular tables, which were linked by adjustable bays of equipment that could be changed in length to adjust the horizontal and vertical curvature of the entire assembly and provided sufficient flexibility during travelling to accommodate level tolerances in the running rails.
Advancing up to 21 metres in about an hour, the RMD Kwikform traveller system has reduced the time for slab pouring significantly when compared with traditional methods. This in-turn allowed this section of the project to be completed on-schedule by the end of November 2009.
For further information contact RMD Kwikform on Tel: 01922 743743 or Email: info@rmdkwikform.com
Construction News
09/03/2010
RMD Kwikform's Unique Tyne Tunnel Traveller System
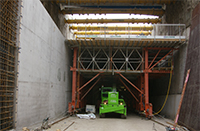
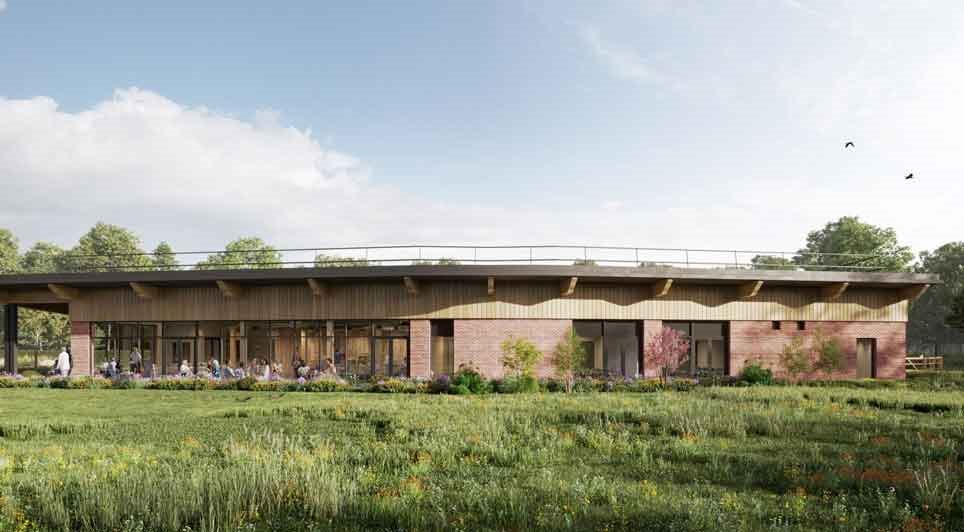
17/04/2025
Willmott Dixon has been selected by Oldham Council to build a new Visitor Centre and Forestry Skills Centre at Northern Roots, the UK's largest urban farm and eco-park.
The development marks a major milestone in the transformation of 160 acres of green space at the heart of Oldham, part of the coun
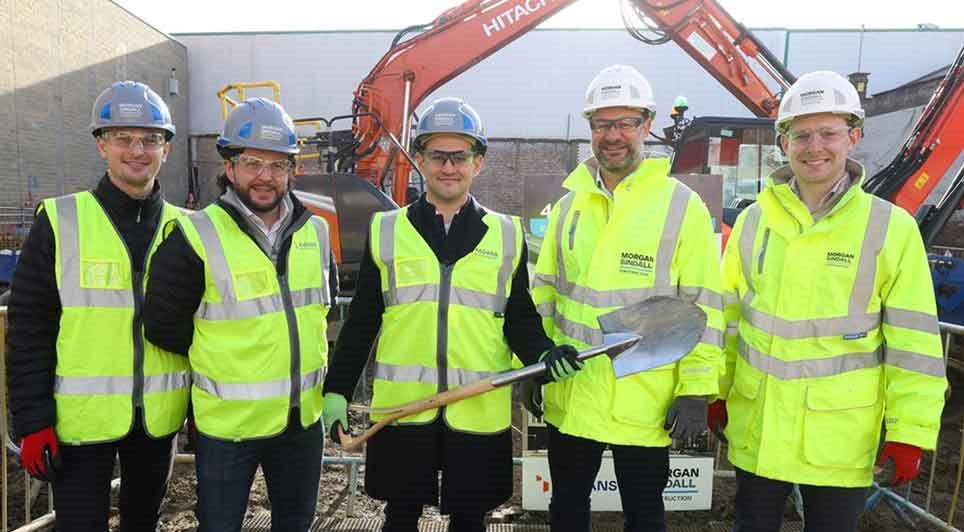
17/04/2025
A groundbreaking ceremony has officially marked the commencement of construction for Versa, a state-of-the-art laboratory facility at King's Cross.
The project, which is being delivered by Morgan Sindall Construction, has been commissioned by Kadans Science Partner, a prominent European investor s
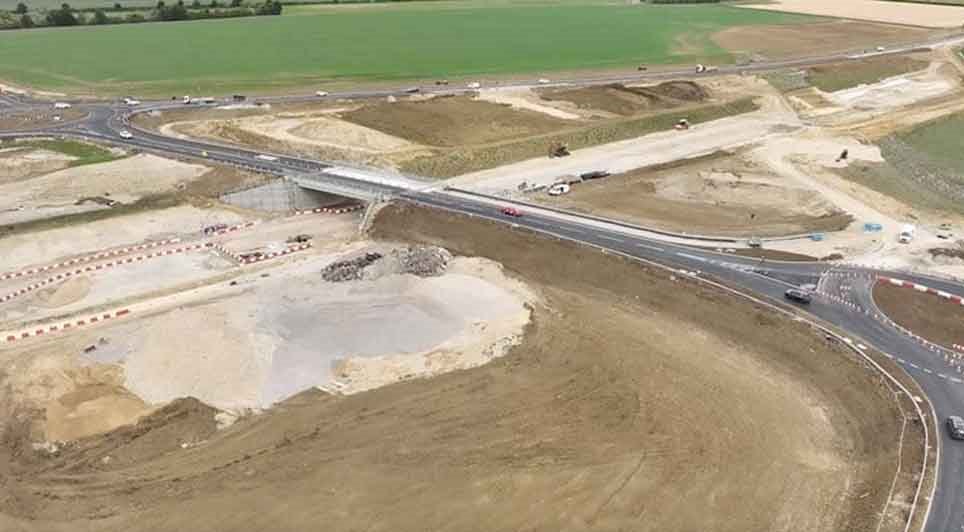
17/04/2025
A major milestone has been reached on Skanska's A428 improvement scheme, as the project team connected the new A428 and B1040 roads over a newly constructed bridge and opened it to traffic last weekend.
The achievement marks a crucial step forward in the project, enabling access to part of the main
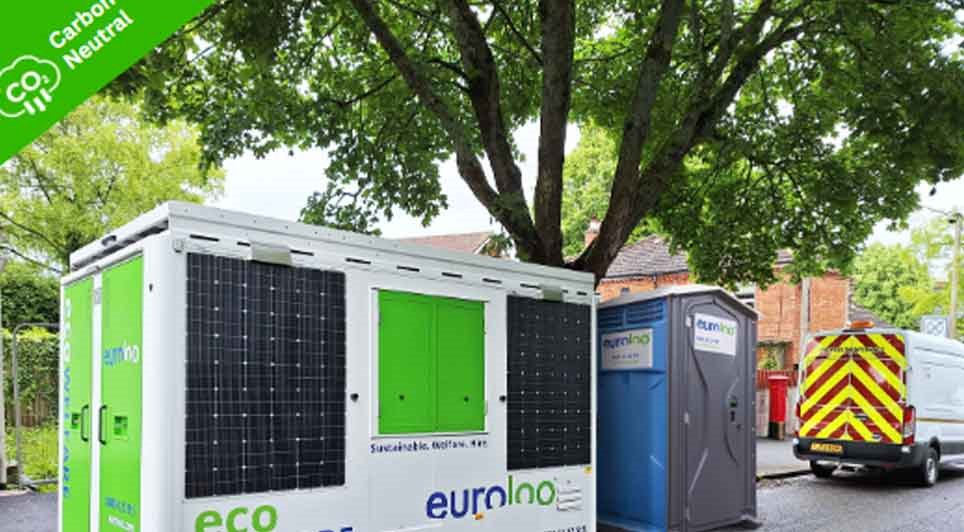
17/04/2025
Our welfare unit hire division offers innovative ecowelfare units ready to be delivered nationwide and available in a range of configurations to accommodate 7, 12, or 15 persons with our most popular unit being our 12ft model fitted with advanced solar panels means there is no noise or vibrations f
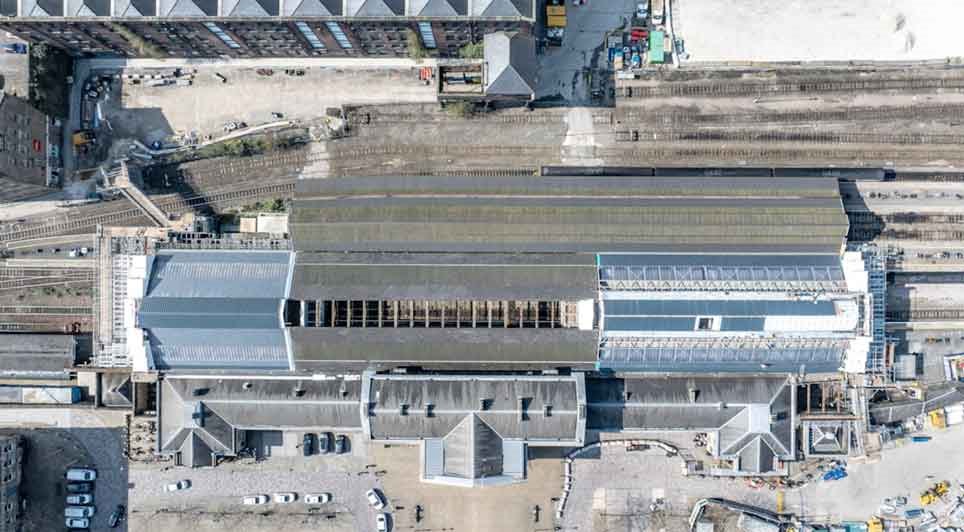
17/04/2025
Huddersfield Station will temporarily close from Saturday 30 August to Monday 29 September 2025 to allow for a critical phase of engineering work as part of the Transpennine Route Upgrade (TRU).
The closure will enable extensive track and platform remodelling at the Grade I listed station, which ha
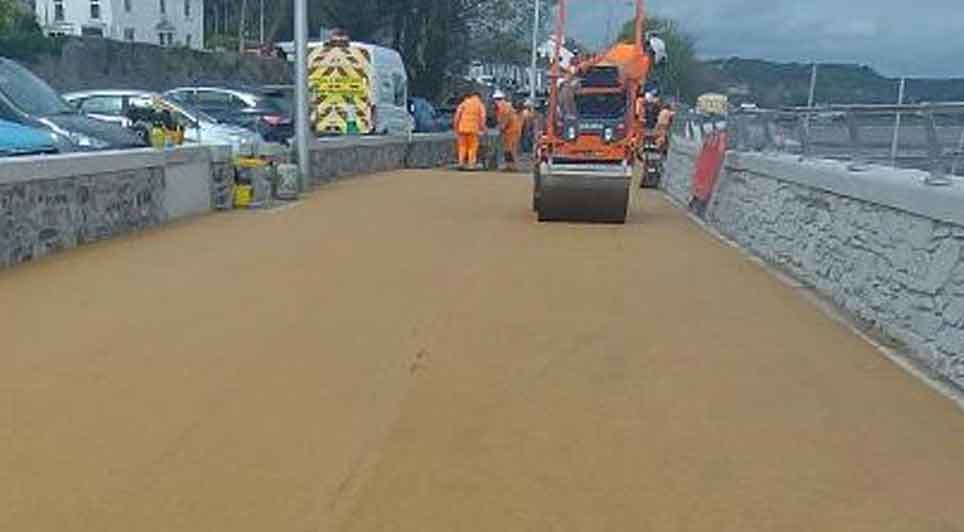
17/04/2025
Visitors to Mumbles over the Easter holidays can now enjoy the transformed promenade, as major upgrades under the Mumbles Coastal Protection Project near completion.
Contractors have begun laying a durable buff-coloured top surface, replacing the previously installed black Tarmac. The fresh finish
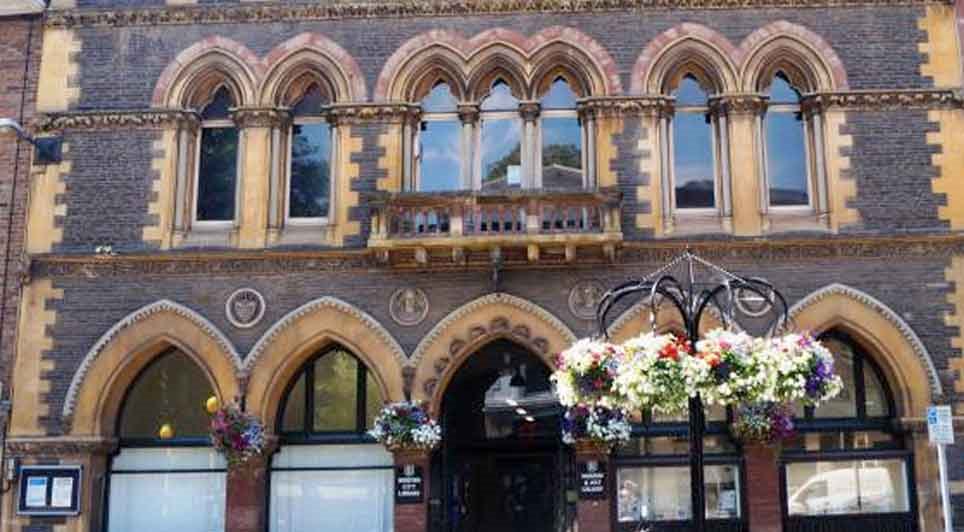
17/04/2025
Herefordshire Council has secured £1 million in funding from the government’s Public Sector Decarbonisation Scheme, to redevelop Hereford's Museum and Art Gallery into one of the most energy-efficient heritage public buildings in the UK.
The funding will be used to install a low carbon heating syst
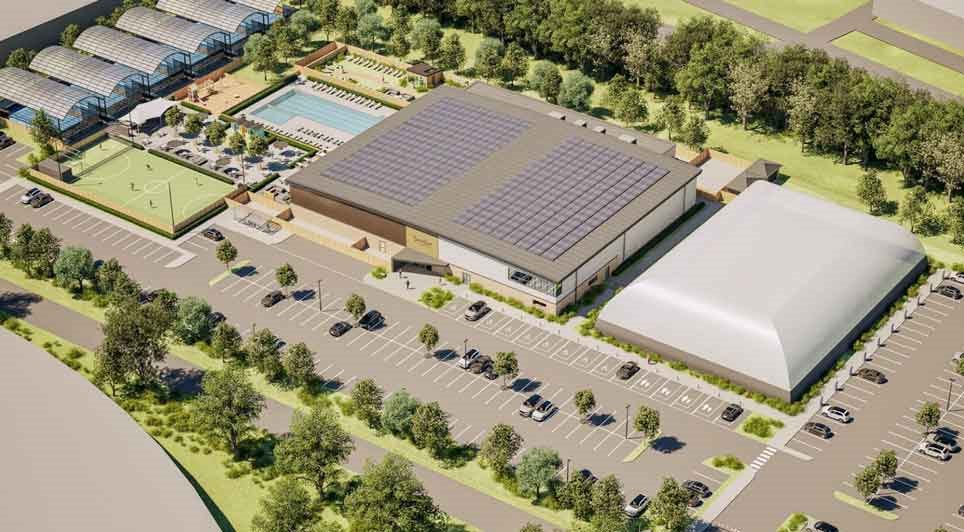
17/04/2025
David Lloyd Leisure, Europe's leading health, fitness and wellness group, has submitted a planning application to Wirral Council for a new club at Wirral Waters.
The proposed club, set to create up to 100 permanent jobs upon completion, will be located at Peel Waters’ Bidston Dock site off Wallasey
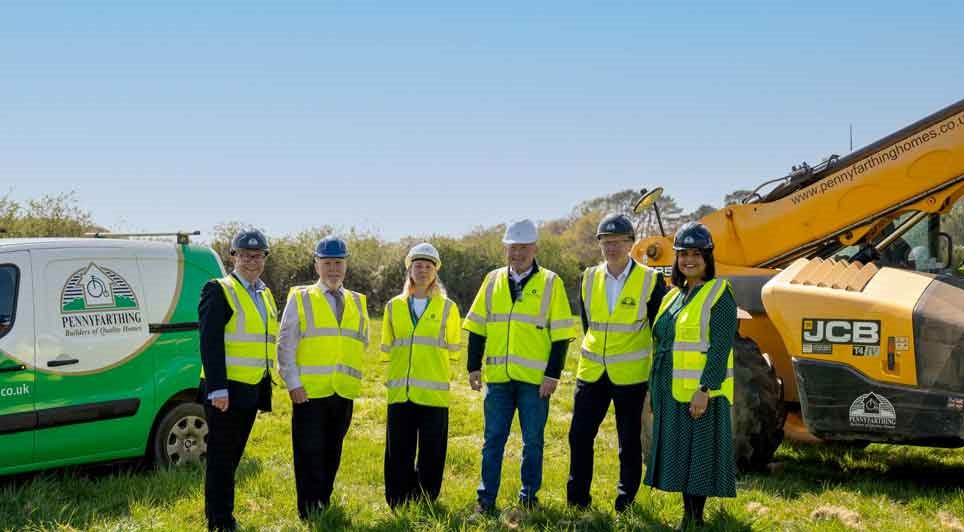
16/04/2025
Pennyfarthing Homes has officially broken ground at Danes Park in New Milton, launching construction on a significant new residential development that will deliver 164 homes.
To mark the milestone, directors from Pennyfarthing Homes welcomed Councillor Steve Davies, Portfolio Holder for Housing and
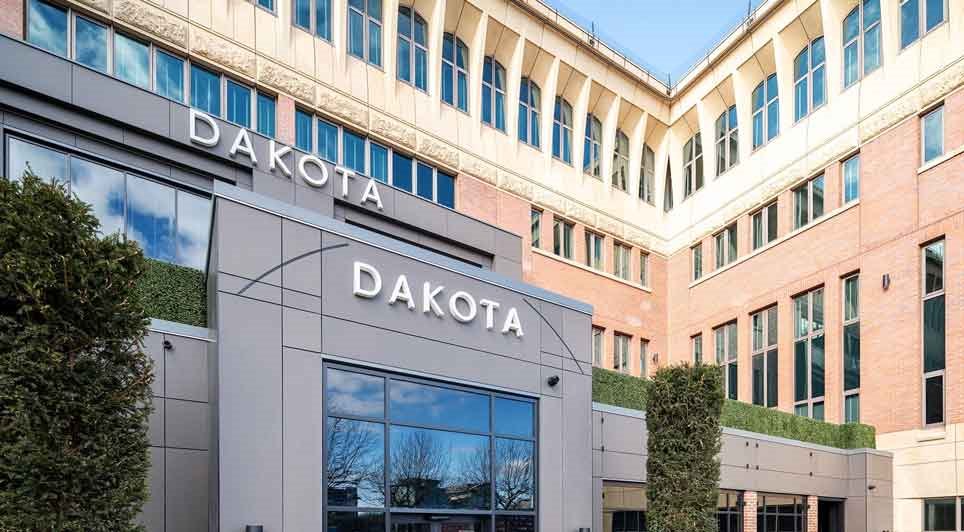
16/04/2025
GMI Construction Group is celebrating the official opening of Dakota Newcastle, the North East's first Dakota Hotel, situated on Newcastle's Quayside.
The 118-room luxury boutique hotel, located at St Anne's Wharf, has welcomed its first guests and is poised to become a major addition to the region