Construction News
26/11/2013
New MIG/MAG Welding-Appliance Platform Takes A Quantum Leap
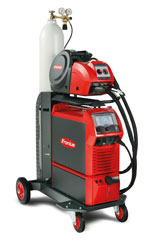
With its radically new modular MIG/MAG welding-appliance platform TPS/i, Fronius is leading the welding sector into a new era: users benefit from working with individually customisable and upgradeable appliances that stand out for their high intelligence and extensive communications functions.
The equipment lets them carry out welding-tasks not only more easily and more quickly, but with even better results. As well as these immediate advantages, the platform is also the foundation on which many innovative future advances will build, giving owners a highly secure investment for the long term.
This quantum leap in welding technology is the fruit of the biggest innovation project in the entire history of Fronius. To pull off this 'tour de force', the project team at this keynote technological leader set their sights on nothing less than getting as close as possible to the perfect arc. This is why staff were told to cast aside old modes of thought, to comb through the company's huge fund of experience and pick out the very best for the benefit of users, and to combine it with ground-breaking new technologies. The result is the rigorously modular MIG/MAG welding-appliance platform TPS/i. This already meets the requirements of 'Industry 4.0', and lifts welding technology to a wholly new level of performance.
Right from the very first development phase of this new platform, its users benefit immediately from numerous technical improvements and new functions. These solve familiar problems and let users weld with noticeably less spatter, with a more stable arc, better penetration and higher efficiency. They also greatly simplify handling of the machines, and make life very much easier for the welder.
A key role is played here by the integrated intelligence that comes with the TPS/i. The process control system is approx. 2000 times faster than in the predecessor generation, capturing far more information about the arc and enabling this to be regulated with even greater precision than ever before. The high-speed bus (SpeedNet) that links system components such as the torch and the wirefeeder to the power source transmits data many times faster than its predecessors, ensuring short reaction times and superior control.
Building on this, the Fronius engineers have further optimised the individual phases of the welding process and dovetailed them with one another even more tightly. For example, TSP/i is the first-ever system to compute the instantaneous temperature at the end of the wire electrode, to calculate from this the necessary (lowered) ignition energy and then to control the power source accordingly. This stabilises the arc more quickly. During the actual welding process, the TPS/i's integrated intelligence now adapts the wirefeed speed to the actual contact-tip to workpiece distance (CTWD) even more rapidly and precisely, thanks to its more advanced control circuit and its highly dynamic motor. One very positive consequence for the welder is that the arc length is re-adjusted in a shorter time, so that the penetration is subject to fewer fluctuations. The controllability of the wirefeeder helps to achieve even better results at the end of the welding operation as well: the wire electrode is retracted at the same time as the welding current is limited, effectively preventing both droplet formation (otherwise unavoidable) and the spattering that would come with it, and wire burn-back.
These optimisations in the welding phases benefit not only the standard process but also two new weld processes which have only been made possible by the integrated intelligence and high-speed control circuits of the TPS/i. The dip-transfer arc process LSC (Low Spatter Control) stands out for its previously unobtainable low tendency to spatter, and for its exceptionally high process stability. The second new process that Fronius now offers is PMC (Pulse Multi Control), which permits significantly higher welding speeds in pulsed-power welding, yet with optimum droplet detachment. What is more, in the PMC process there is markedly less undercutting.
Special mention should be made that users of the TPS/i platform can put together the hardware and software they need to match their own individual requirements, and later alter or upgrade it as needed; this gives them high security of investment. For example, the consistent approach taken to modularisation makes it possible for a user to start by investing in just one machine for dip-transfer welding, and then to upgrade this same machine for pulsed-power welding at a later stage. The system is multiprocess-capable, so if it is used for another process only the process-relevant system components need to be changed – the power source, wirefeeder and hose-connector package are the same for all processes.
Adapting the software after the system has been modified, and indeed updating the software, is simplicity itself: One central data-copying operation is all it takes to supply all the components with the software they need, or with the latest version of it. New characteristics can be added without the system software having to be changed.
The TPS/i not only elevates the welding process itself to a new level but also opens up a new dimension in terms of its interactive possibilities. A sturdy touch-sensitive 7-inch display informs the user quickly and clearly – with graphics and local-language plain text – on the current system status. Together with the intuitive graphical user interface, which can be adapted to users’ special requirements, this lets the welder stay in control of his system and avoid operator errors. Welding-system/robot interaction has also been significantly evolved: not only are data now interchanged with the robot control very much faster, making it possible to integrate the robot more tightly into the welding system, but this data interchange can also be adapted to local circumstances with the aid of a user-friendly programming tool, needing no expert assistance, and visualised via the display.
The new welding platform TPS/i opens up to users an unprecedented degree of individuality, interactive possibilities and marked improvements. This lets companies carry out even complex and varying welding-tasks swiftly, effectively and with consistently high quality. The TPS/i's built-in intelligence and end-to-end modularity provide a firm foundation for future innovations, ensuring high security of investment for years to come.
The equipment lets them carry out welding-tasks not only more easily and more quickly, but with even better results. As well as these immediate advantages, the platform is also the foundation on which many innovative future advances will build, giving owners a highly secure investment for the long term.
This quantum leap in welding technology is the fruit of the biggest innovation project in the entire history of Fronius. To pull off this 'tour de force', the project team at this keynote technological leader set their sights on nothing less than getting as close as possible to the perfect arc. This is why staff were told to cast aside old modes of thought, to comb through the company's huge fund of experience and pick out the very best for the benefit of users, and to combine it with ground-breaking new technologies. The result is the rigorously modular MIG/MAG welding-appliance platform TPS/i. This already meets the requirements of 'Industry 4.0', and lifts welding technology to a wholly new level of performance.
Right from the very first development phase of this new platform, its users benefit immediately from numerous technical improvements and new functions. These solve familiar problems and let users weld with noticeably less spatter, with a more stable arc, better penetration and higher efficiency. They also greatly simplify handling of the machines, and make life very much easier for the welder.
A key role is played here by the integrated intelligence that comes with the TPS/i. The process control system is approx. 2000 times faster than in the predecessor generation, capturing far more information about the arc and enabling this to be regulated with even greater precision than ever before. The high-speed bus (SpeedNet) that links system components such as the torch and the wirefeeder to the power source transmits data many times faster than its predecessors, ensuring short reaction times and superior control.
Building on this, the Fronius engineers have further optimised the individual phases of the welding process and dovetailed them with one another even more tightly. For example, TSP/i is the first-ever system to compute the instantaneous temperature at the end of the wire electrode, to calculate from this the necessary (lowered) ignition energy and then to control the power source accordingly. This stabilises the arc more quickly. During the actual welding process, the TPS/i's integrated intelligence now adapts the wirefeed speed to the actual contact-tip to workpiece distance (CTWD) even more rapidly and precisely, thanks to its more advanced control circuit and its highly dynamic motor. One very positive consequence for the welder is that the arc length is re-adjusted in a shorter time, so that the penetration is subject to fewer fluctuations. The controllability of the wirefeeder helps to achieve even better results at the end of the welding operation as well: the wire electrode is retracted at the same time as the welding current is limited, effectively preventing both droplet formation (otherwise unavoidable) and the spattering that would come with it, and wire burn-back.
These optimisations in the welding phases benefit not only the standard process but also two new weld processes which have only been made possible by the integrated intelligence and high-speed control circuits of the TPS/i. The dip-transfer arc process LSC (Low Spatter Control) stands out for its previously unobtainable low tendency to spatter, and for its exceptionally high process stability. The second new process that Fronius now offers is PMC (Pulse Multi Control), which permits significantly higher welding speeds in pulsed-power welding, yet with optimum droplet detachment. What is more, in the PMC process there is markedly less undercutting.
Special mention should be made that users of the TPS/i platform can put together the hardware and software they need to match their own individual requirements, and later alter or upgrade it as needed; this gives them high security of investment. For example, the consistent approach taken to modularisation makes it possible for a user to start by investing in just one machine for dip-transfer welding, and then to upgrade this same machine for pulsed-power welding at a later stage. The system is multiprocess-capable, so if it is used for another process only the process-relevant system components need to be changed – the power source, wirefeeder and hose-connector package are the same for all processes.
Adapting the software after the system has been modified, and indeed updating the software, is simplicity itself: One central data-copying operation is all it takes to supply all the components with the software they need, or with the latest version of it. New characteristics can be added without the system software having to be changed.
The TPS/i not only elevates the welding process itself to a new level but also opens up a new dimension in terms of its interactive possibilities. A sturdy touch-sensitive 7-inch display informs the user quickly and clearly – with graphics and local-language plain text – on the current system status. Together with the intuitive graphical user interface, which can be adapted to users’ special requirements, this lets the welder stay in control of his system and avoid operator errors. Welding-system/robot interaction has also been significantly evolved: not only are data now interchanged with the robot control very much faster, making it possible to integrate the robot more tightly into the welding system, but this data interchange can also be adapted to local circumstances with the aid of a user-friendly programming tool, needing no expert assistance, and visualised via the display.
The new welding platform TPS/i opens up to users an unprecedented degree of individuality, interactive possibilities and marked improvements. This lets companies carry out even complex and varying welding-tasks swiftly, effectively and with consistently high quality. The TPS/i's built-in intelligence and end-to-end modularity provide a firm foundation for future innovations, ensuring high security of investment for years to come.
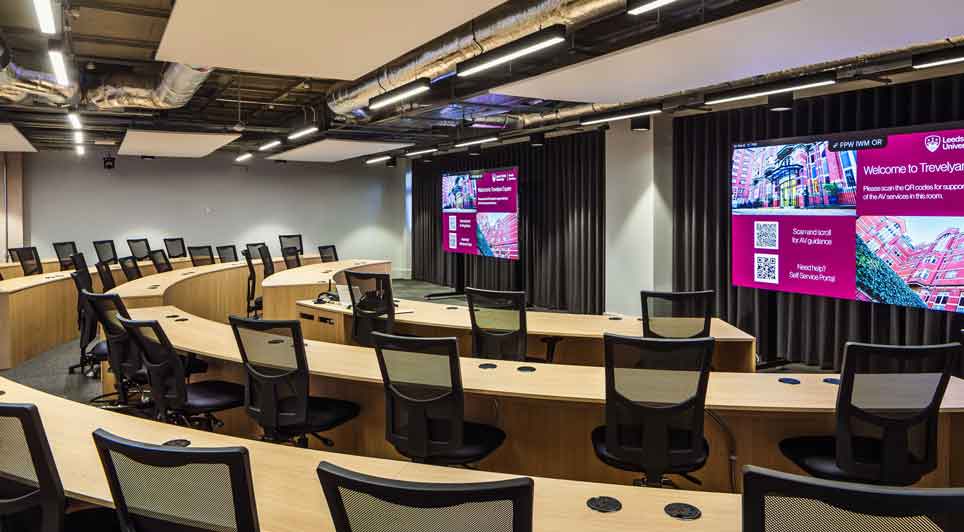
17/01/2025
Leeds Trinity University has officially opened its newly refurbished City Campus at 1 Trevelyan Square in Leeds.
Completed by GRAHAM Interior Fit-Out, the transformation of the central Leeds site introduces state-of-the-art facilities designed to improve learning and collaborate with industry partn
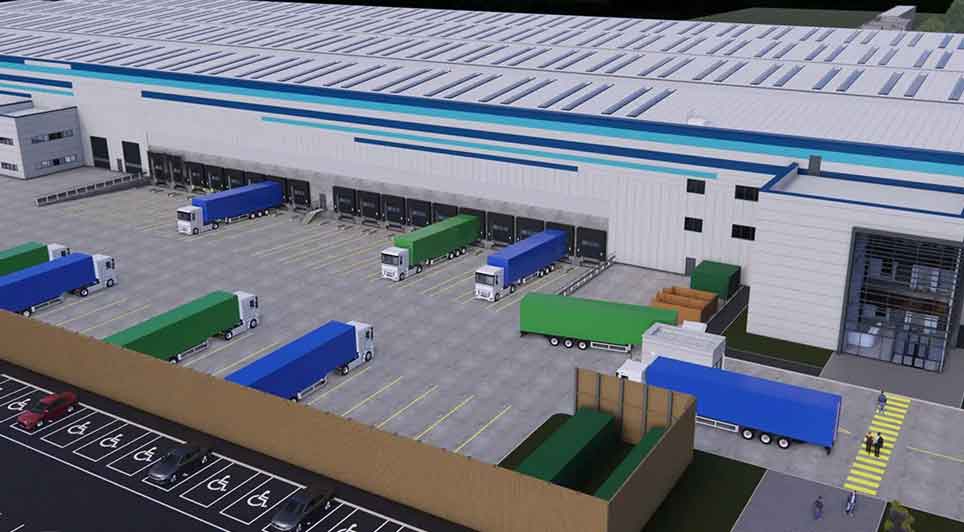
17/01/2025
Trammell Crow Company (TCC) has secured planning permission for a Grade A logistics scheme in Heywood, Greater Manchester, following a successful planning appeal.
The development will feature two state-of-the-art industrial and logistics buildings. One building will house two units measuring 4,796
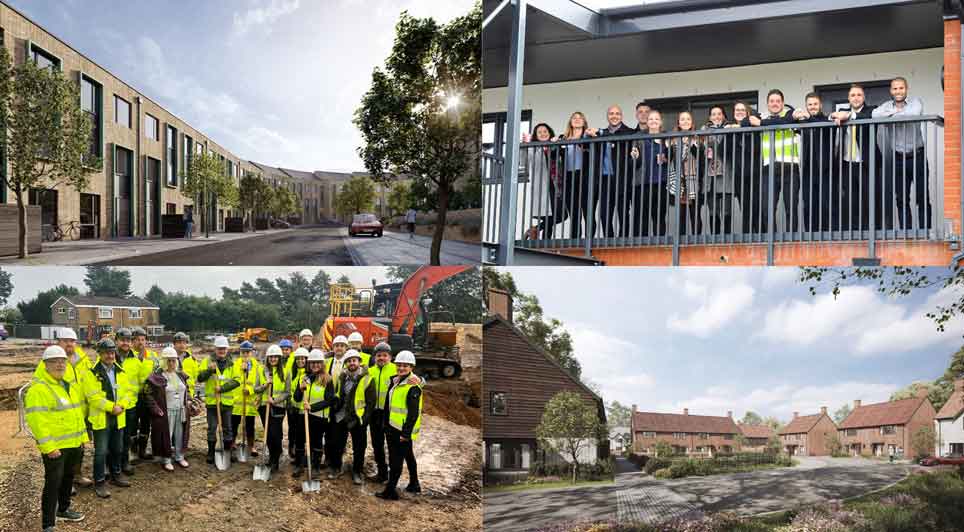
17/01/2025
Poole-based developer AJC Group has celebrated a record-breaking 2024, delivering 100 affordable homes, a significant increase from the 72 units completed in the previous year.
Since 2023, AJC Group has completed and handed over 172 affordable homes across five sites.
In 2024 alone, the developer
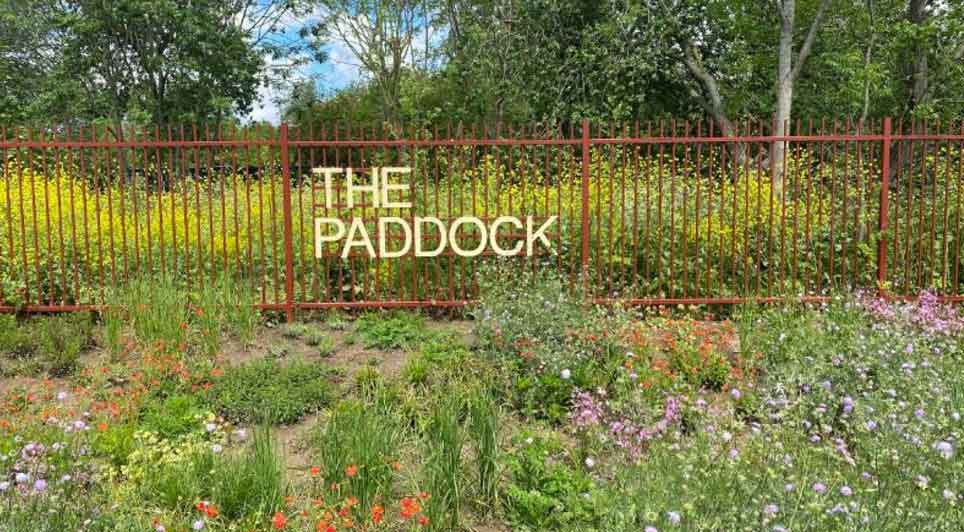
17/01/2025
Plans for one of the most ambitious parks projects in London have taken a significant step forward, with Haringey Council securing nearly two additional acres of land around The Paddock nature reserve in Tottenham Hale.
The agreement with Thames Water marks a major milestone in the transformation o
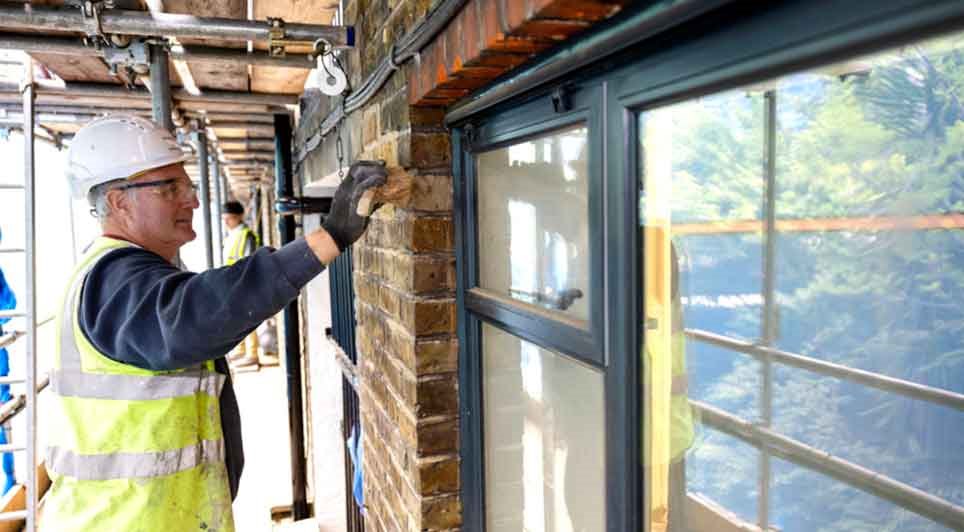
17/01/2025
Islington Council has unveiled two draft guidance documents aimed at helping residents, businesses, and developers combat climate change by making buildings more energy efficient and fostering a greener, healthier borough.
The consultation seeks feedback on the draft Climate Action Supplementary Pl
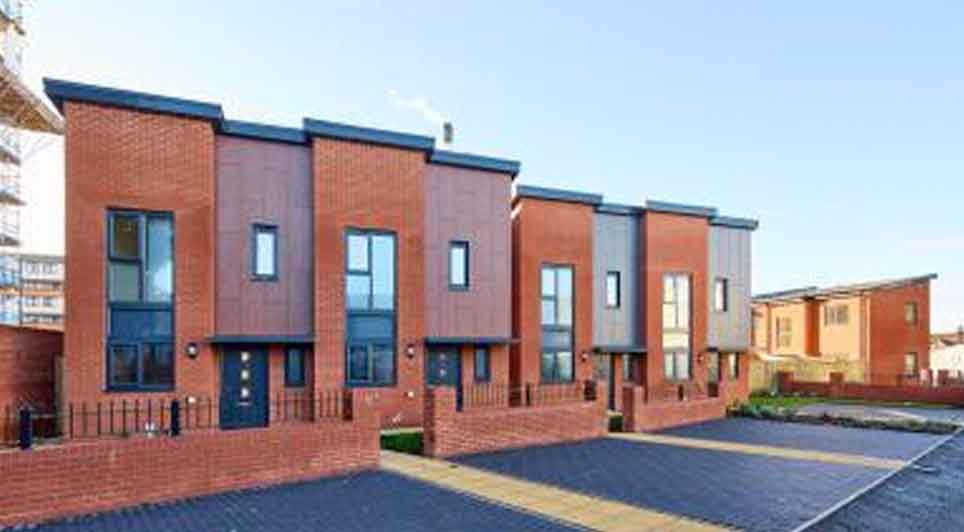
17/01/2025
The City of Wolverhampton Council has unveiled a £98 million investment plan over the next five years to develop around 500 new homes across the city.
The proposal, part of the Housing Revenue Account (HRA) Business Plan, received Cabinet approval this week and now moves to Full Council for final
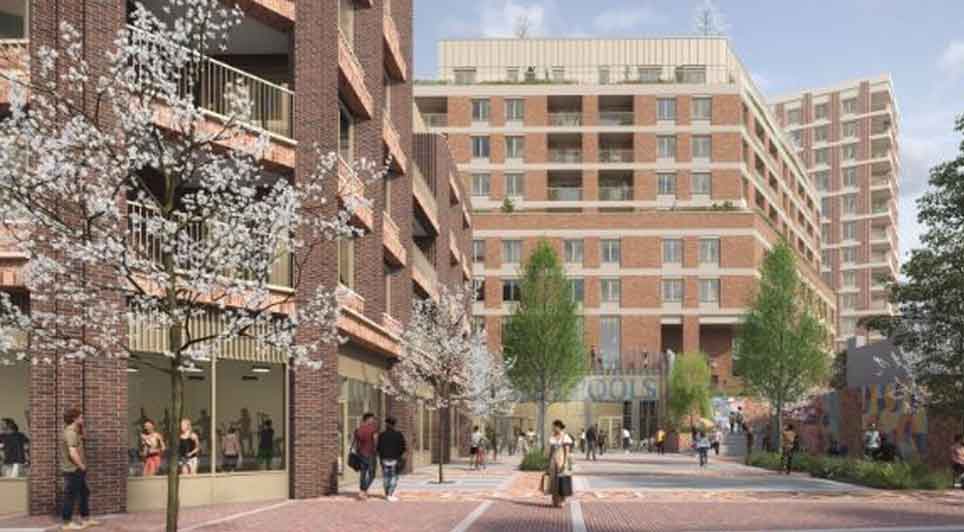
17/01/2025
Croydon Council has announced a significant milestone in the redevelopment of the Purley Pool site, with revised proposals submitted for a new leisure centre, later living housing, and the regeneration of the surrounding area.
A planning application for the site was initially submitted in 2024, pro
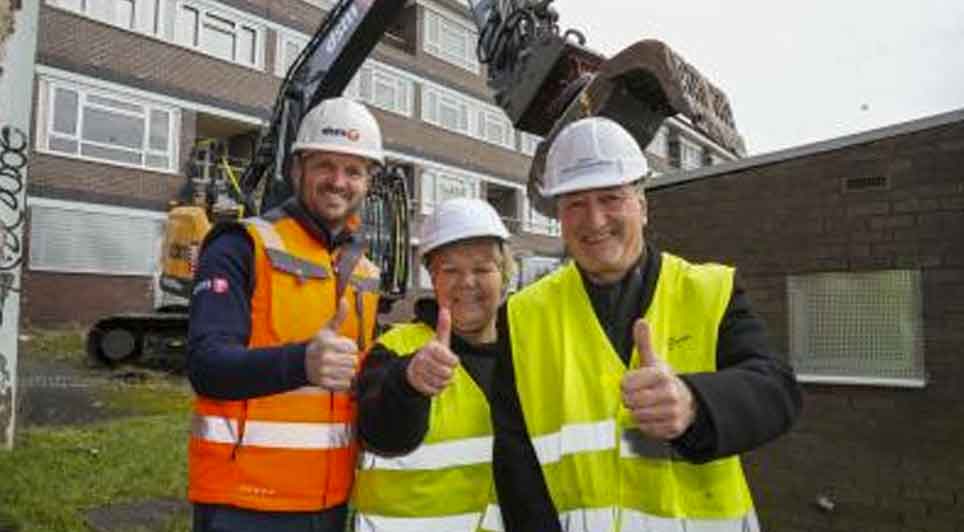
17/01/2025
The City of Wolverhampton Council has announced that demolition work has commenced on the New Park Village estate, marking the start of a major £40 million redevelopment project to transform outdated council housing.
Contractor DSM Demolition has begun pulling down poor-quality bungalows on Valley
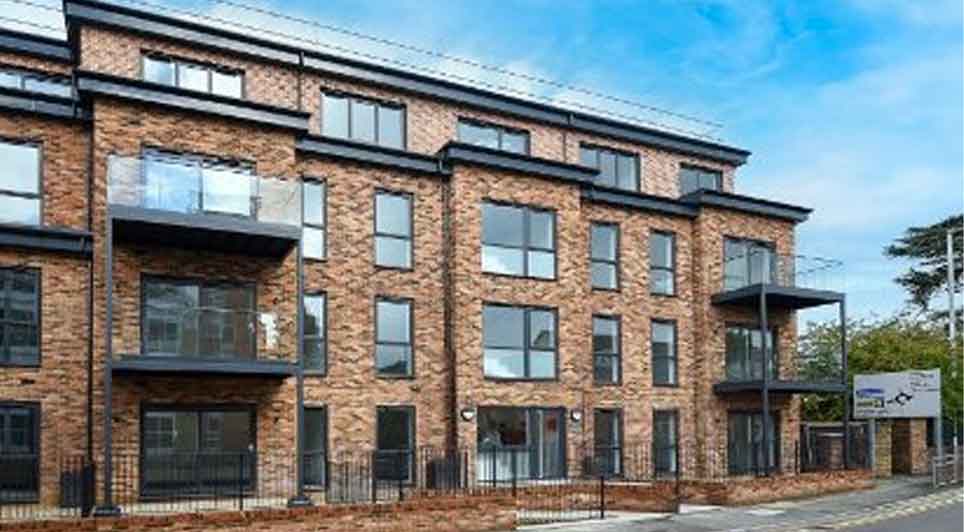
17/01/2025
Hillingdon Council has acquired 12 new homes at Carpenters Court in Uxbridge.
Leader of Hillingdon Council, Cllr Ian Edwards and Cllr Steve Tuckwell, Cabinet Member for Planning, Housing and Growth, visited the site to officially mark the handover of the properties from local developer Kearns Devel
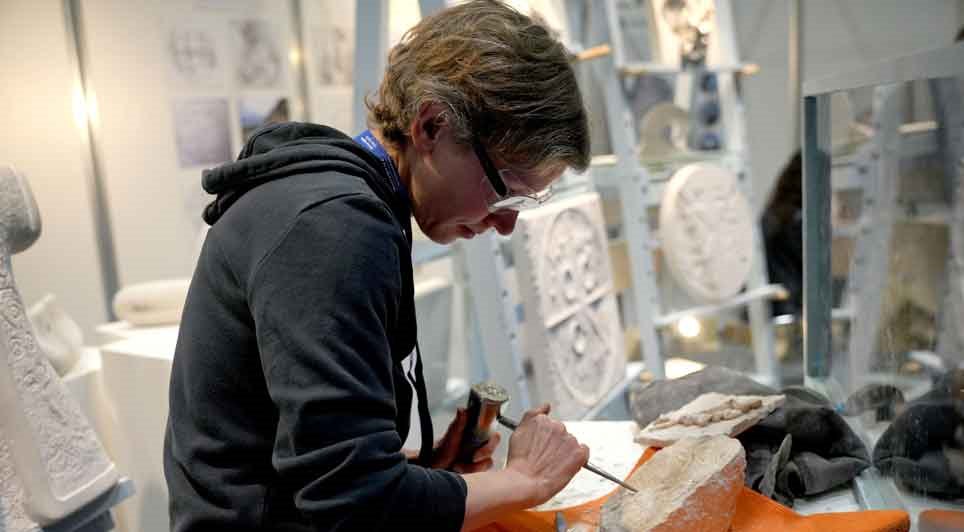
17/01/2025
Organisers of UK Construction Week (UKCW) have announced another major coup for the show's 10th anniversary year, with the news that UKCW London will be co-locating with the 14th edition of The Stone Show & Hard Surfaces, the principal industry event for surface design.
Established 26 years ago, th