Construction News
25/02/2015
Cathodic Corrosion Protection Of High Strength Subsea Bolting
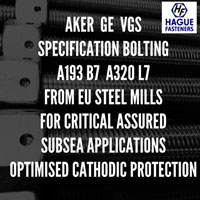
In the last decade Hague Fasteners have seen massive growth in the supply of British Manufactured, European origin material Critical Bolting manufactured to Aker, VGS and other OEM specifications specifically written to ensure the Prevention of failures of high strength fasteners in use in offshore and subsea applications.
The selection, specification, manufacture and installation of fasteners for subsea use is critical to ensure their resistance to corrosion due to various forms of environmentally assisted cracking.
As Oil exploration progresses into far deeper waters, the cost of a fastener failure or other mechanical component breakdown is both a serious financial risk but more so the environmental damage could be truly catastrophic.
With reputation at stake, Hague Fasteners with 45 years of sector experience and technical excellence ensures your subsea projects are without risk and quality assured.
The Subsea specifications Hague Fasteners work strictly too give particular emphasis on the prevention of environmentally induced cracking under the conditions of cathodic prevention. Cathodic protection is frequently used in Marine vessels, and offshore and subsea steel structures to reduce the base metal corrosion by making it the cathode in an electrochemical cell.
It is Hague's decades of experience and knowhow that gives their ever growing Subsea customer base the peace of mind that the special fasteners manufactured and coated by Hague Fasteners do not deviate from the expert specifications designed to minimise the risk from the various forms of environmentally assisted cracking (EAC).
These include stress corrosion cracking (SCC), hydrogen embrittlement (HE) and sustained load cracking (SLC).
The sectors supplied by Hague Fasteners are almost always the high performance applications requiring higher strength fasteners. A major issue with fasteners used offshore and subsea is that higher strength fasteners are susceptible to stress corrosion cracking and hydrogen embrittlement. In general, higher the strength, the higher the hardness of the material and the greater the susceptibility to these failure mechanisms.
The more common critical offshore and subsea bolting material grades requested are the common bolting materials ASTM A 320 Grade L43, ASTM A320 L7 and ASTM A193 Grade B7, the fastener industry is flooded with inferior imported mass produced petrochemical fasteners where quality is often compromised in exchange for being the cheapest and securing contracts. Hague Fasteners distance themselves from this side of the market as failures in these cheap and suspect quality items have occurred, particularly where the use of cathodic protection increases their susceptibility to hydrogen cracking.
Hague Fasteners certify their manufactured items with additional PMI testing, MPI testing and further ensure integrity of their components by limiting the hardness well below the proven 34 HRC where high strength bolting becomes highly susceptible to cracking from hydrogen embrittlement induced by cathodic protection. For reference, the maximum hardness of regular B7 is 35 HRC and hence can fall above the susceptible range.
Quality simply can not be compromised. The best in British manufacturing at Hague Fasteners ensures all the risks are assessed and minimised by strict adherence to Subsea and Offshore manufacturing specifications. Where reputation is at stake, Hague Fasteners are your solution.
The selection, specification, manufacture and installation of fasteners for subsea use is critical to ensure their resistance to corrosion due to various forms of environmentally assisted cracking.
As Oil exploration progresses into far deeper waters, the cost of a fastener failure or other mechanical component breakdown is both a serious financial risk but more so the environmental damage could be truly catastrophic.
With reputation at stake, Hague Fasteners with 45 years of sector experience and technical excellence ensures your subsea projects are without risk and quality assured.
The Subsea specifications Hague Fasteners work strictly too give particular emphasis on the prevention of environmentally induced cracking under the conditions of cathodic prevention. Cathodic protection is frequently used in Marine vessels, and offshore and subsea steel structures to reduce the base metal corrosion by making it the cathode in an electrochemical cell.
It is Hague's decades of experience and knowhow that gives their ever growing Subsea customer base the peace of mind that the special fasteners manufactured and coated by Hague Fasteners do not deviate from the expert specifications designed to minimise the risk from the various forms of environmentally assisted cracking (EAC).
These include stress corrosion cracking (SCC), hydrogen embrittlement (HE) and sustained load cracking (SLC).
The sectors supplied by Hague Fasteners are almost always the high performance applications requiring higher strength fasteners. A major issue with fasteners used offshore and subsea is that higher strength fasteners are susceptible to stress corrosion cracking and hydrogen embrittlement. In general, higher the strength, the higher the hardness of the material and the greater the susceptibility to these failure mechanisms.
The more common critical offshore and subsea bolting material grades requested are the common bolting materials ASTM A 320 Grade L43, ASTM A320 L7 and ASTM A193 Grade B7, the fastener industry is flooded with inferior imported mass produced petrochemical fasteners where quality is often compromised in exchange for being the cheapest and securing contracts. Hague Fasteners distance themselves from this side of the market as failures in these cheap and suspect quality items have occurred, particularly where the use of cathodic protection increases their susceptibility to hydrogen cracking.
Hague Fasteners certify their manufactured items with additional PMI testing, MPI testing and further ensure integrity of their components by limiting the hardness well below the proven 34 HRC where high strength bolting becomes highly susceptible to cracking from hydrogen embrittlement induced by cathodic protection. For reference, the maximum hardness of regular B7 is 35 HRC and hence can fall above the susceptible range.
Quality simply can not be compromised. The best in British manufacturing at Hague Fasteners ensures all the risks are assessed and minimised by strict adherence to Subsea and Offshore manufacturing specifications. Where reputation is at stake, Hague Fasteners are your solution.
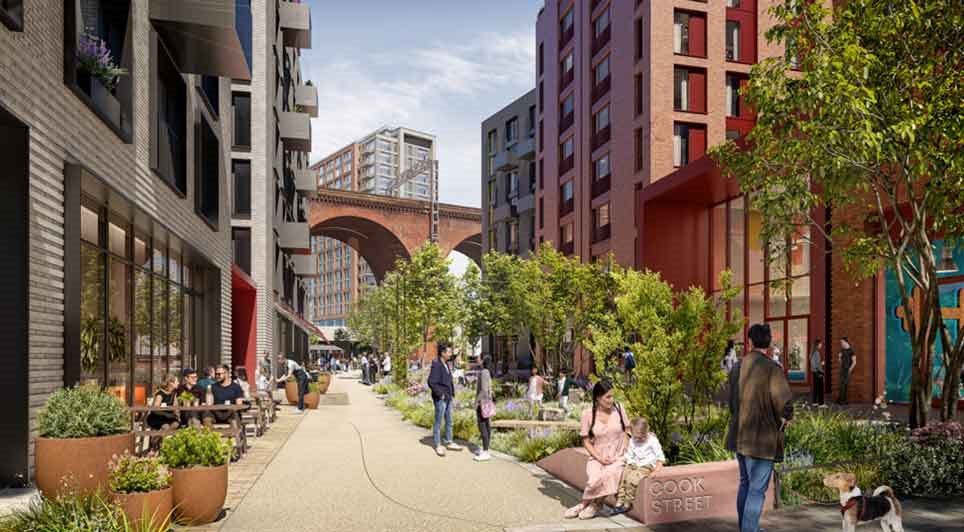
05/02/2025
Stockport Mayoral Development Corporation (MDC) and ECF, a joint venture between Homes England, Legal & General, and Muse, have selected Vinci as the preferred contractor for Phase 1 of Stockport 8, a £350 million residential development west of Stockport town centre.
The decision follows a competi
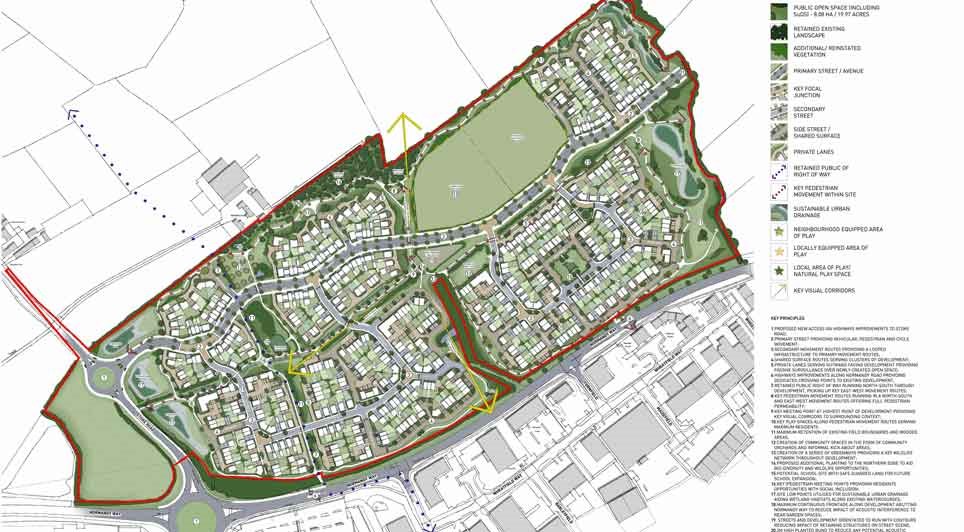
05/02/2025
Vistry Group has finalised contracts for a significant housing development in Hinckley, Leicestershire, securing outline planning permission to deliver 475 new homes in the area.
The development, located east of Stoke Road and north of Normandy Way in the town's northern region, has a projected val
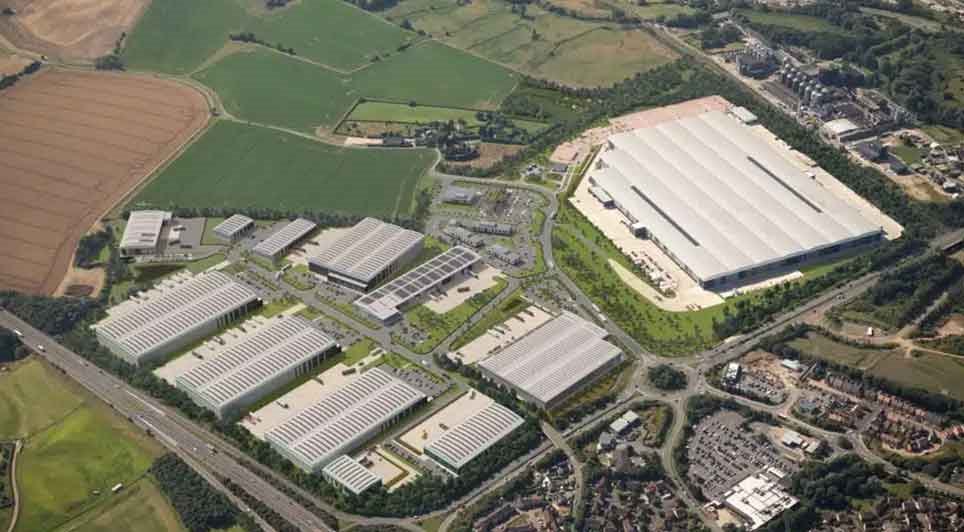
05/02/2025
Wilten Construction has been awarded a second Design and Build contract at Gateway 14 by client Gateway 14 Ltd and Jaynic.
The project involves the development of a state-of-the-art, three-storey Skills and Innovation Centre spanning 35,000 sq ft in the heart of Gateway 14. Designed to achieve BREE
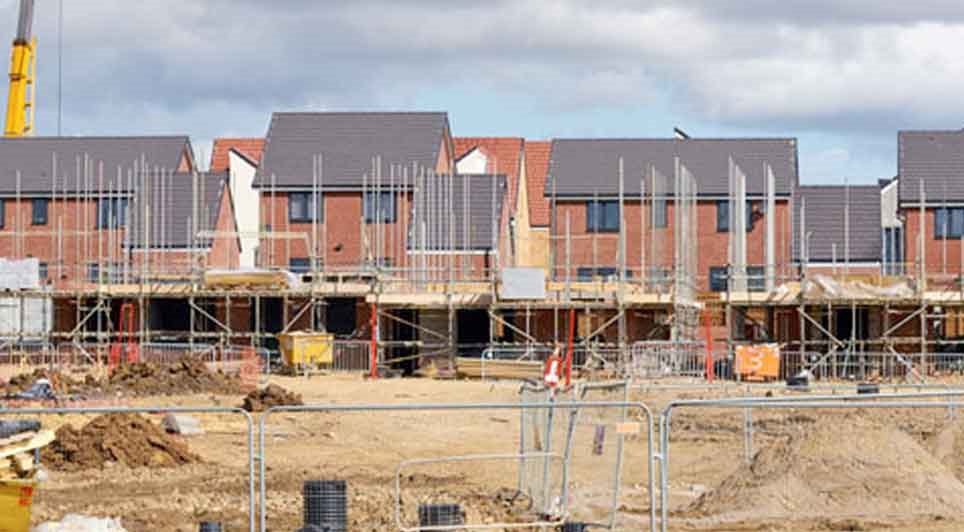
05/02/2025
Knowsley Council has approved a major housing development in Kirkby, giving the green light to 800 new energy-efficient homes in the town's centre.
The decision also secures £7.7 million in Section 106 contributions from developer Barratt David Wilson Homes, further boosting local investment.
The
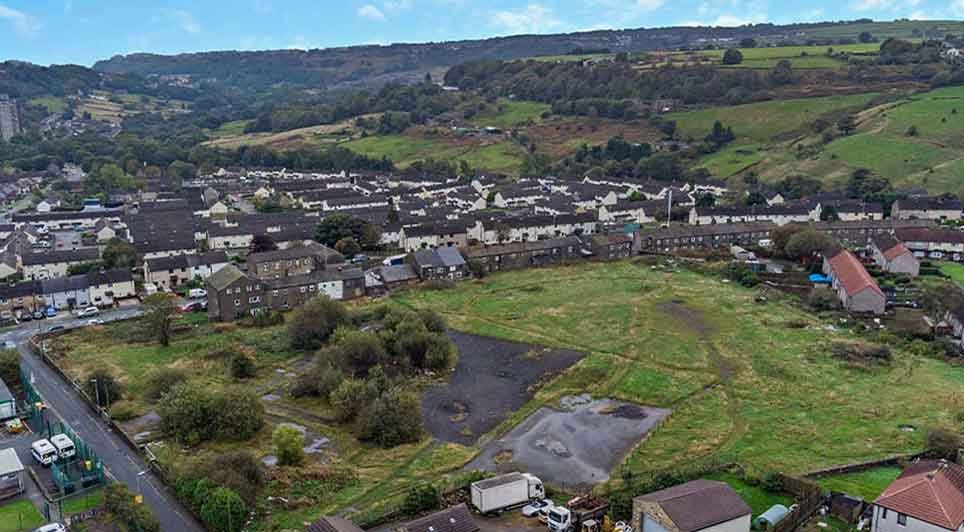
05/02/2025
Keepmoat Homes has announced plans to invest over £50 million in three new housing developments across Calderdale, aiming to deliver more than 200 new homes.
The developments, undertaken in partnership with Calderdale Council, form part of the North Halifax Transformation Programme, a local authori
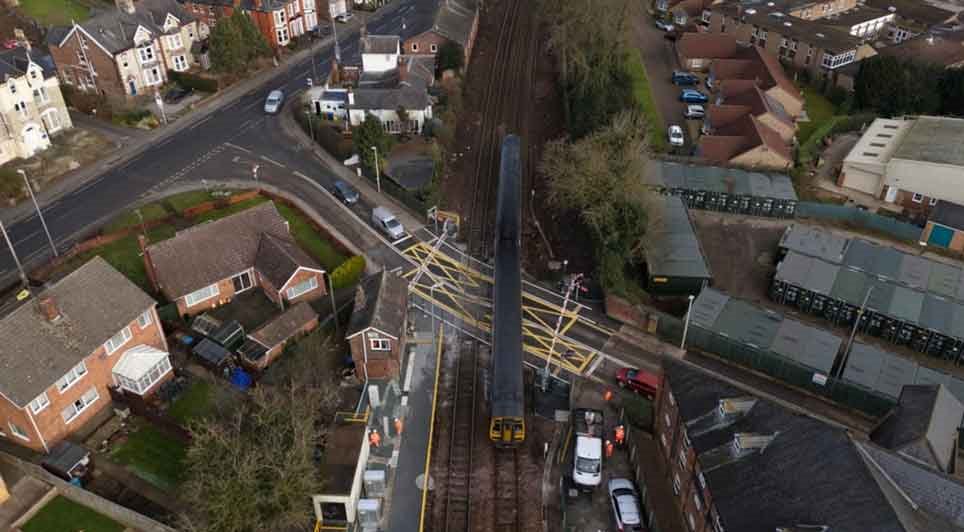
05/02/2025
Essential renewal work at Skerne Road level crossing in Driffield has been completed. Over a six-day period, engineers replaced decades-old equipment, installing a state-of-the-art operating system, replacing the level crossing deck, and resurfacing the road.
The newly installed operating system is
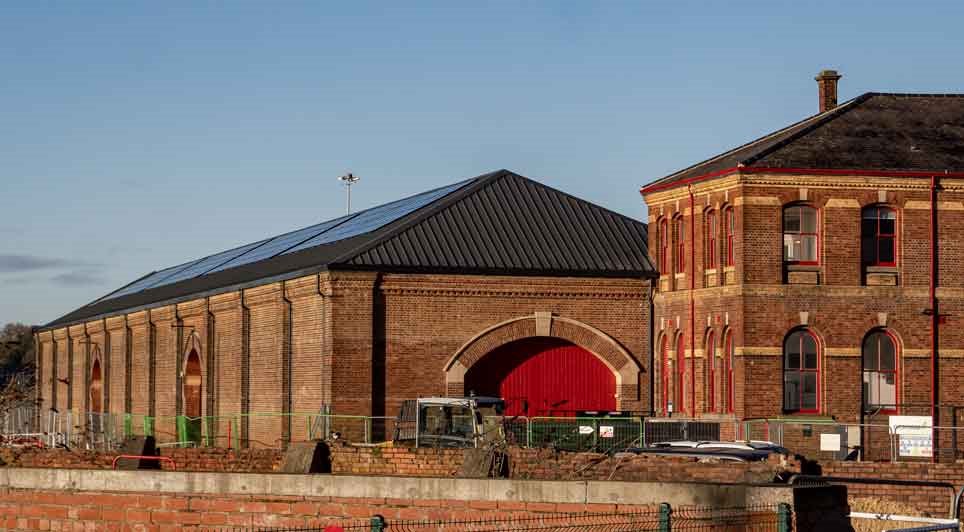
05/02/2025
Construction firm GRAHAM is currently carrying out essential restoration work at the National Railway Museum in York, replacing the Grade II listed roof structure at Station Hall.
Originally built between 1875 and 1877 as a goods station, Station Hall now houses the museum’s six royal carriages.
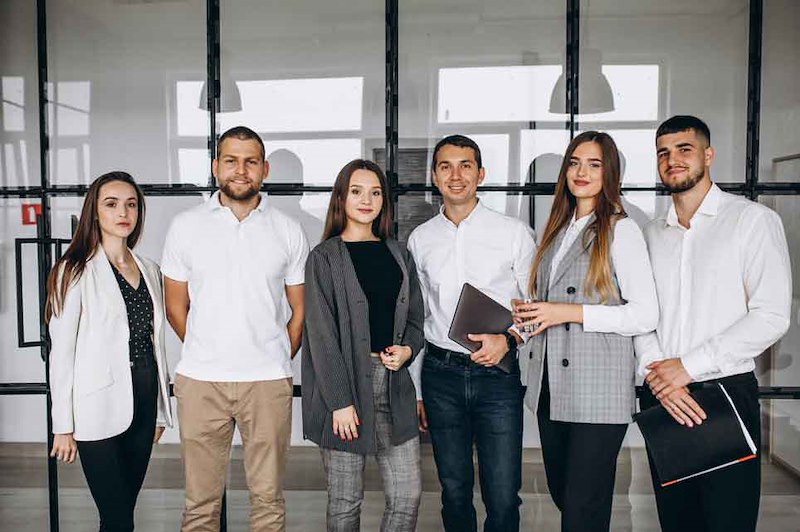
05/02/2025
Mezzanine floors are commonly associated with additional storage or expanded floor space, but did you know they can also have a profound impact on employee productivity and morale? At Doity Engineering, we specialise in designing and installing mezzanine floors for
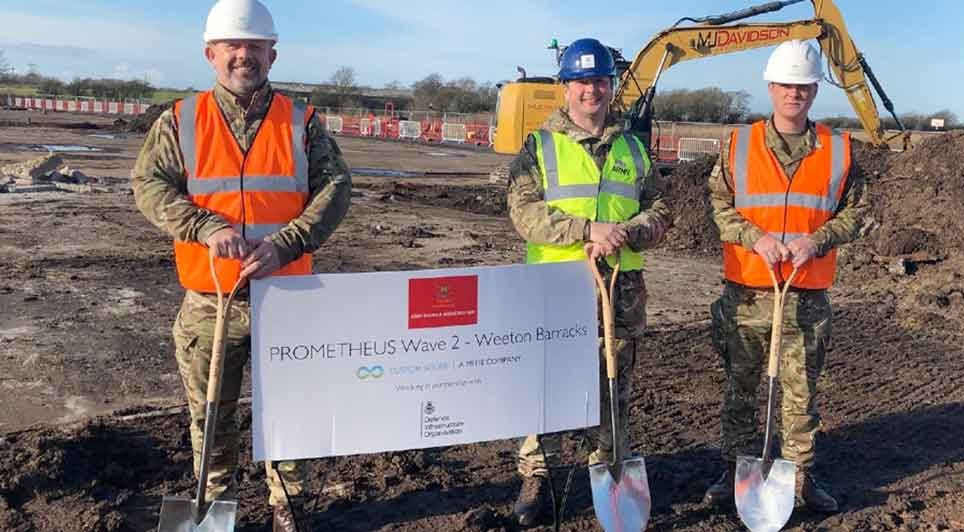
05/02/2025
Construction work is commencing on a new solar array at Weeton Barracks in Lancashire that will generate over one third of the site’s energy needs.
The work has been funded under the British Army’s Project Prometheus, a scheme that is increasing renewable energy across the army estate through inst
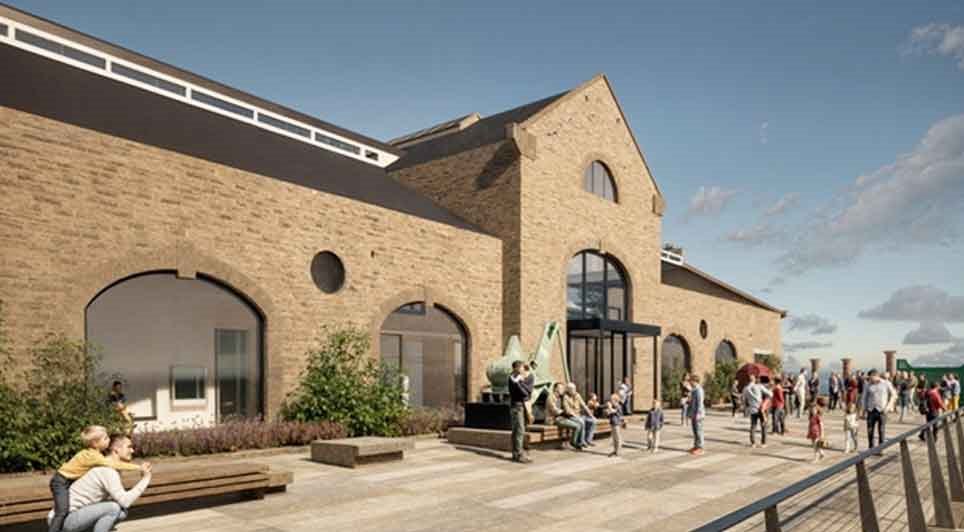
05/02/2025
The regeneration of Hartlepool's waterfront has reached a significant milestone with a £631,000 grant from The National Lottery Heritage Fund.
The funding will support the development phase of the 'Tides of Change' project, aimed at transforming the visitor experience at the Museum of Hartlepool a