HVAC is an area in which there may be significant savings in considering alternative technologies. Replacing the conventional steel ducts with fabric-based alternatives offers relevant gains in terms of time usage and total costs.
It happens almost as regularly as clockwork that contractors and construction clients, due to external factors, such as archeological findings, missing or delayed deliveries, or even geopolitical challenges, find themselves facing significant delays or budget overruns. This is not a fun situation to be in, but what if we were to tell you that there's hope yet – through considering alternative technologies.
The Americans even have a term for it, "value engineering", aka the art of finding savings through alternative products without compromising the quality. And HVAC is often at the pinnacle of this exercise, because we are typically some of the last elements to be installed on a project.
Conventional ductwork is a time consuming and labour intensive job to install. The heavy steel ducts require special tools, alert workers and typically also involve onsite attenuation and post processing. This is why the air dispersion ducting is an area with significant savings potential.
In terms of manhours, up 75% can be saved by switching from steel ducting to fabric ducting. Fabric ducts weight as little as 10% of a steel solution, which also means it can be added to existing building mass without structural reinforcement. Not only are the fabric-based solutions 4-5 times faster to install, they also offer a much safer work environment due to their lightweight nature.
The ease of installation is a hallmark of the technology. It doesn't require any specialised tools and installation can be handle by two people in a matter of hours – of course depending on the project size.
The fabric air dispersion solution arrives on site within two weeks of ordering the system and it comes ready for installation, tailored to the specific project. This makes it easy to plan, and a relevant source of time gains if the project is exceeding the time frame; lean construction at its best. The system also takes up virtually no space on the building site – a few boxes compared to a couple of truckloads of steel ducts.
In terms of material prices there is also savings to be gained from going fabric, thus the total installed costs saving from switching from steel to fabric ducting ranges up to 70%. This is one of the reasons why the global market for fabric air dispersion is growing.
Another is the operational savings that can be realised from the switch to a more precise and even air dispersion method. Clients are realizing up to 40% savings on their energy consumption due to the lower pressure loss and the higher airflow precision of the alternative technology. Thus, fabric ducting is also a more sustainable alternative, which is a theme that is gaining in importance within the European construction sector.
As fabric air dispersion solutions are tailored to the specific project, there is no on site attenuation; no welding, no cutting, no insulating or painting, no adding grilles or diffusors. In other words: significantly less hassle.
Once the system is running there are more gains to be had from the alternative fabric-based technology. There are no issues with condensation, because the duct "breathes" and there is virtually no system maintenance, as long as the pre-filter is changed as prescribed. The latter means the facility manager also saves time further adding to the savings on running costs.
The best is saved for last, as the switch from steel ducting to fabric ducting actually entails an increased comfort levels in the occupied zone, creating a more pleasant indoor environment and IAQ. It is in fact a win-win situation, even if it is derived from exceeded budgets and blown timeframes.
The savings that can be realised from using alternative fabric-based air dispersion technology are valuable to the contractor as well as the building owner and facility manager. One might even call it the "life hack" of the construction sector.
www.fabricair.com
Construction News
09/09/2019
What Can You Do When Both Timeframe And Budget Is Exceeded?
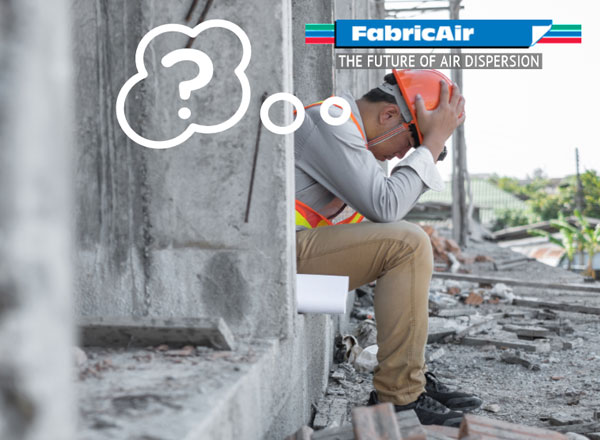
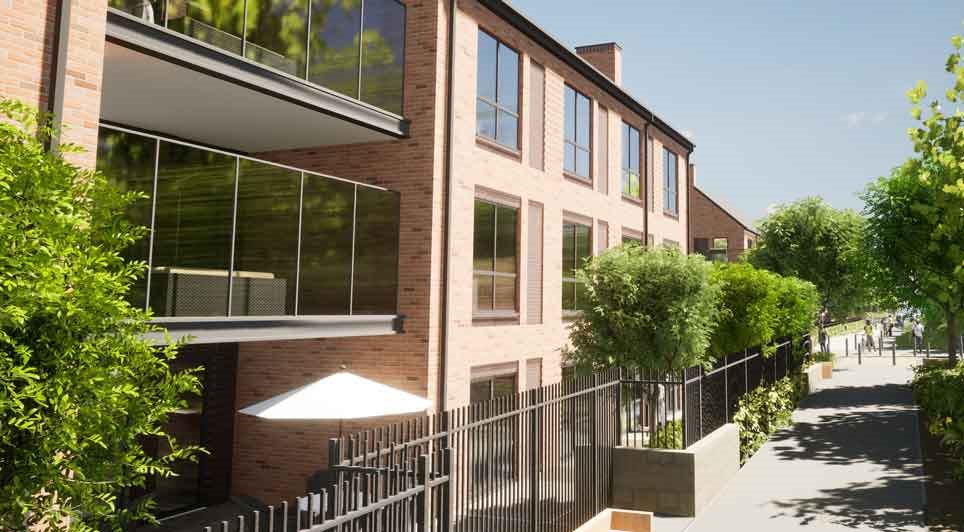
04/04/2025
A major new multi-generational housing scheme is set to take shape in Congleton after the McGoff Group secured unanimous planning approval for its proposed development on Morley Drive, the former site of John Morley Limited.
Approved at a recent planning committee meeting, the joint application fro
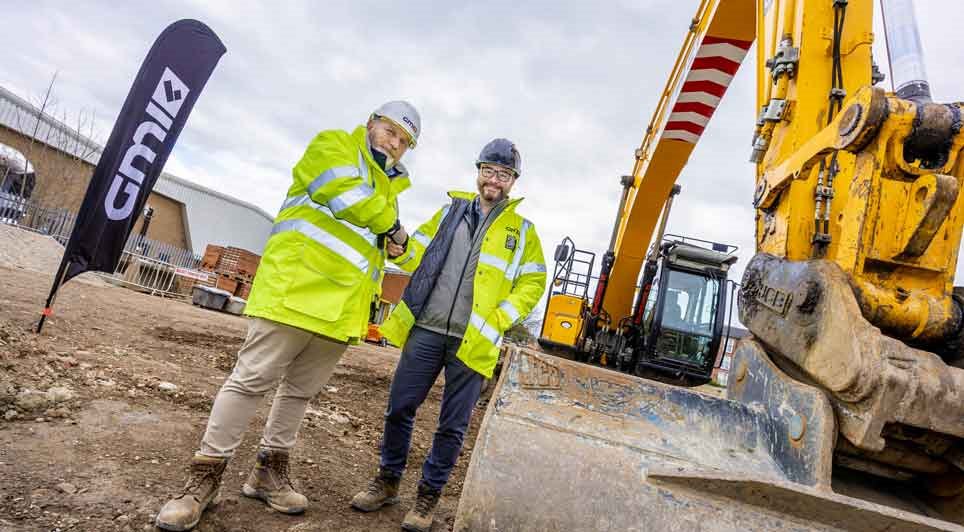
04/04/2025
GMI Construction Group has broken ground on a new £17 million purpose-built student accommodation (PBSA) development on Foss Islands Road, marking its third major student housing project in York.
The five-storey scheme, developed in partnership by Urbium Capital and Harrogate-based Gregory Properti
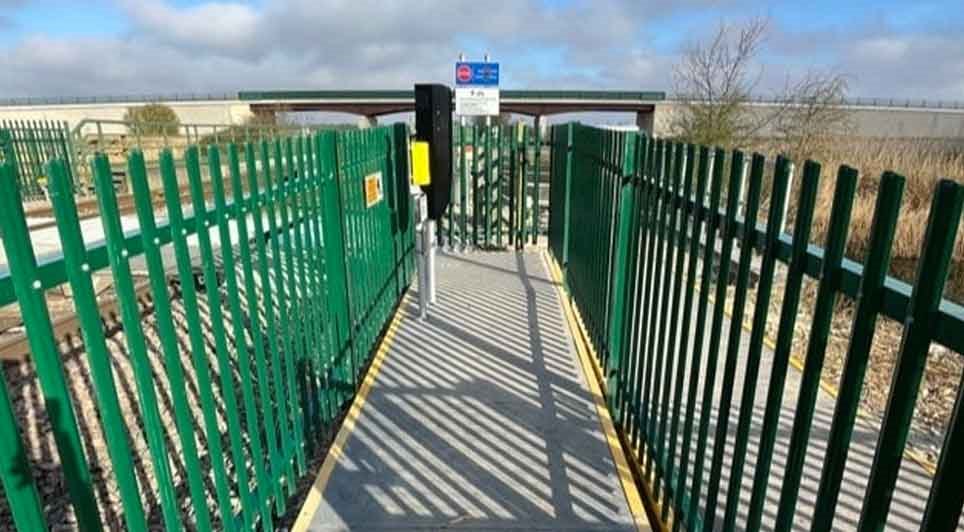
04/04/2025
Network Rail has reopened a railway crossing at Vernatts Drain in Lincolnshire, using cutting-edge technology to ensure safer crossings for pedestrians and cyclists.
The crossing, which had been temporarily closed during the construction of the Spalding Western Relief Road, has now been upgraded wi
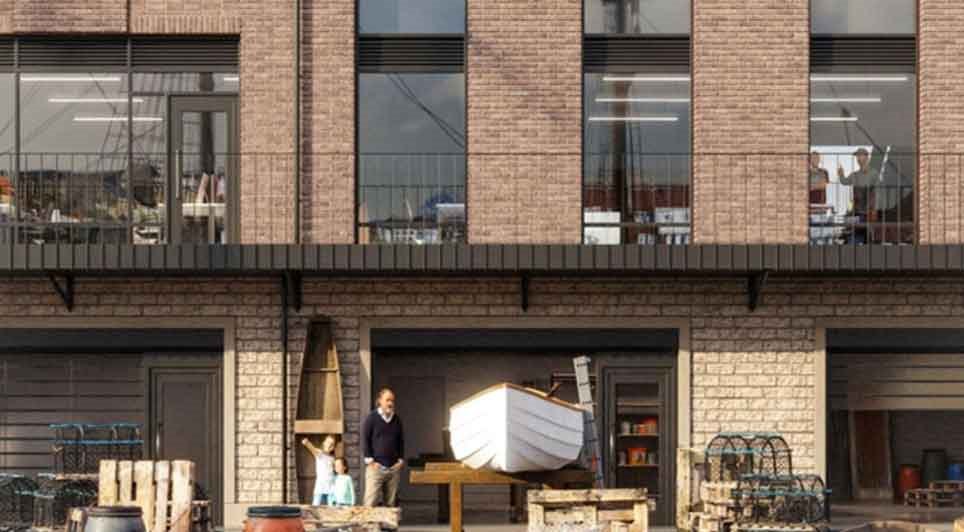
04/04/2025
Construction has officially begun on a landmark maritime training facility in Whitby that aims to position the town as a key player in the UK's offshore renewable energy and maritime industries.
Willmott Dixon has been appointed to deliver the £9.6 million Whitby Maritime Training Hub, a cutting-ed
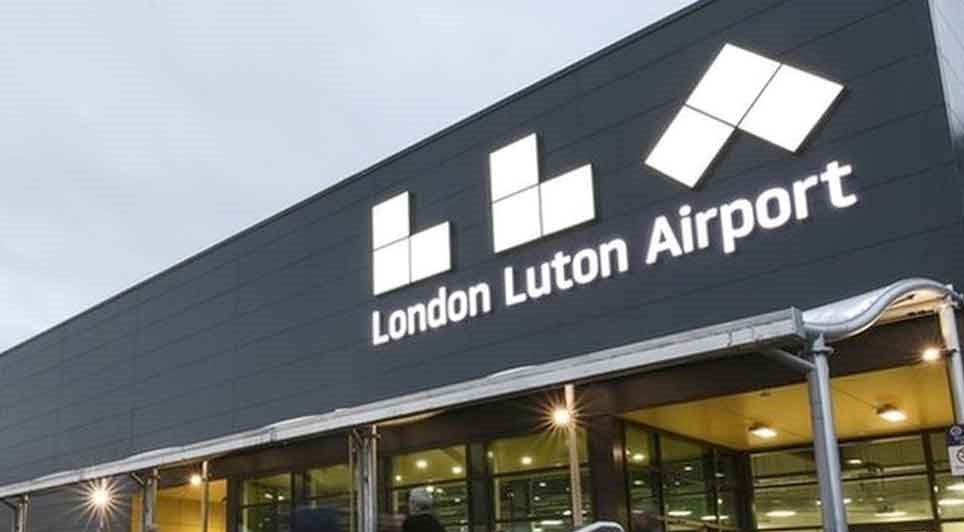
04/04/2025
London Luton Airport has received the green light from the UK Government to increase its annual passenger capacity from 19 million to 32 million, in a decision expected to transform the town's economy and create thousands of new jobs.
The expansion proposal, brought forward by Luton Rising, the air
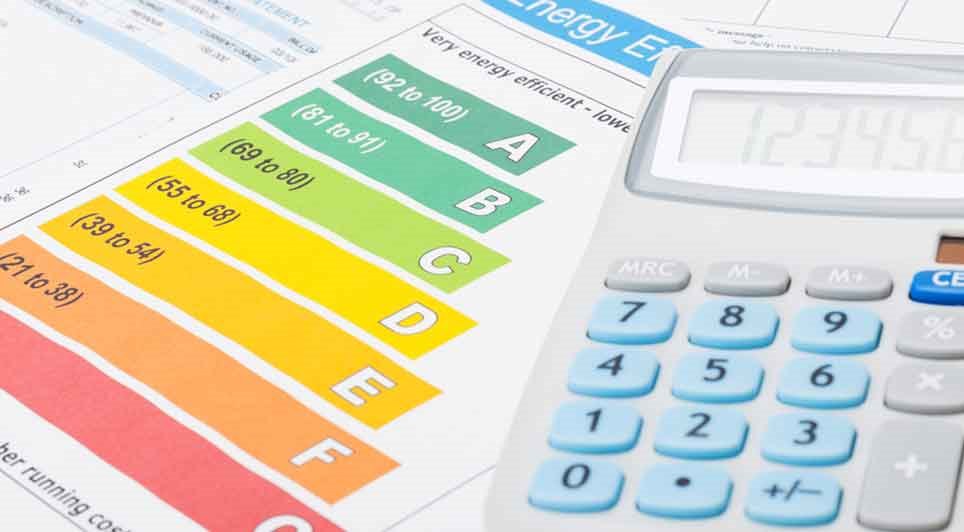
04/04/2025
Essential Green Skills, part of the Essential Site Skills Group, is encouraging commercial property owners to act now to improve their Energy Performance Certificate (EPC) ratings ahead of proposed tightening of Minimum Energy Efficiency Standards (MEES), which could require a minimum EPC rating of
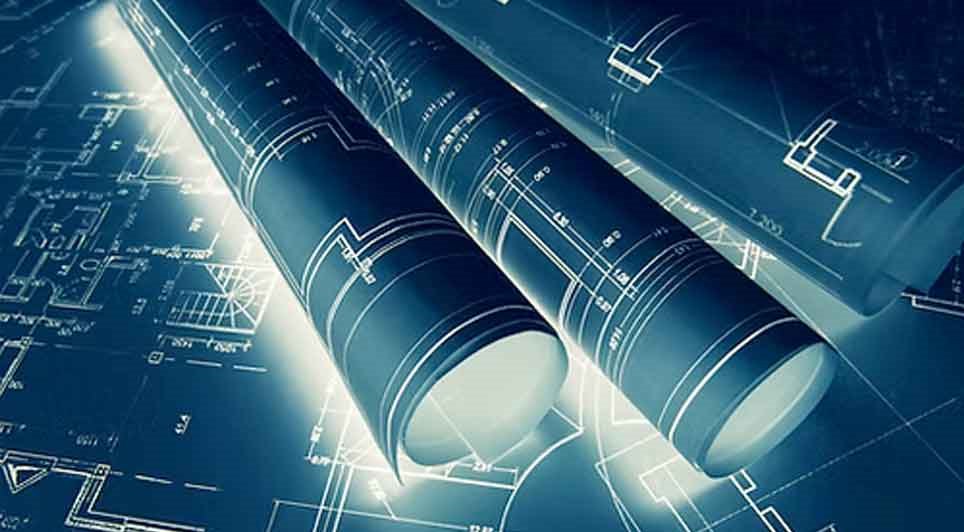
04/04/2025
M.A Humm Quantity Surveying & Estimating Ltd has been delivering comprehensive preconstruction solutions since 2008.
Specialising in full estimating services, detailed and bespoke quantity surveying services, precise measurement and Bills of Quantities, and meticulous project planning, the company
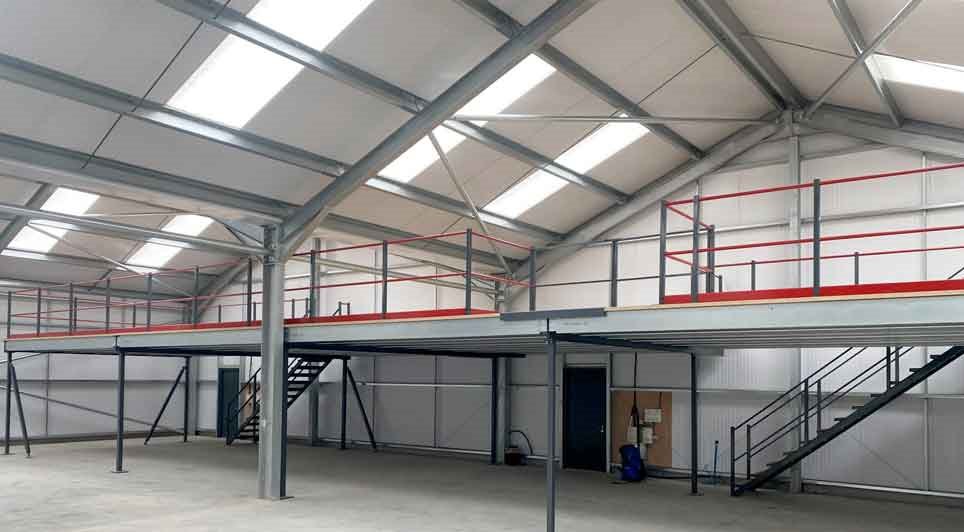
04/04/2025
AE Racking Installations Ltd, a leading provider of racking systems and storage solutions, is proud to offer a wide range of services to meet the unique needs of both residential and commercial clients.
Specialising in the installation, dismantling, and relocation of various racking systems, AE Ra
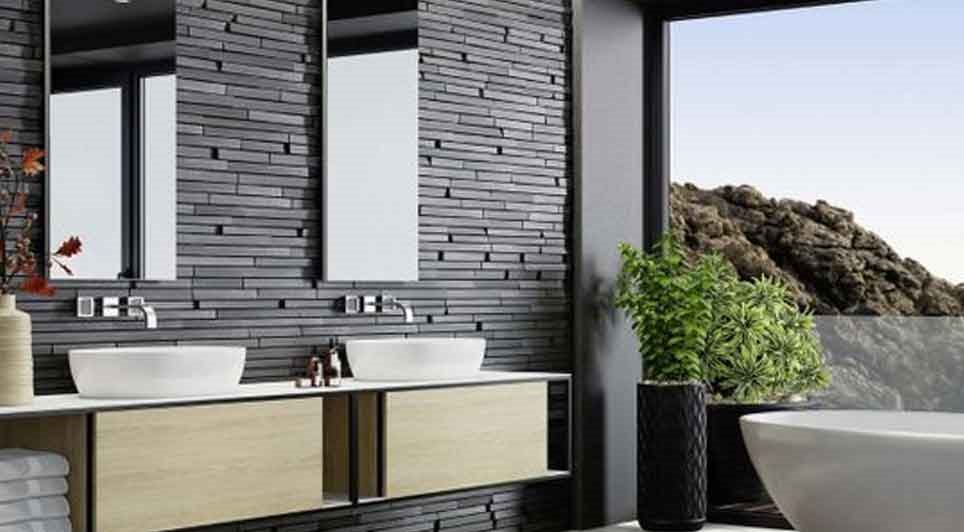
04/04/2025
If you've been wanting to give your home an update without breaking the bank, then you need luxury vinyl click flooring!
Vinyl has come a long way from the low-quality flooring of the past, and it´s now extremely durable and also comes in a large number of colours and styles to suit your taste.
V
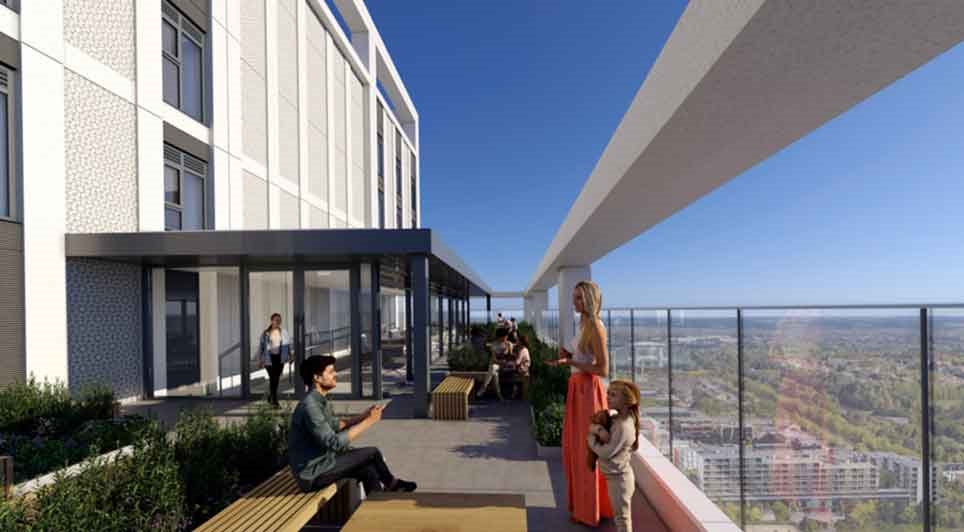
03/04/2025
Galliford Try's Investments business has received planning permission for a major Private Rental Sector (PRS) development at Grafton Gate in Central Milton Keynes, set to transform the city's skyline with a 33-storey residential tower.
The 599 Grafton Gate scheme will deliver 302 new homes, offerin