Everyone's talking about Industry 4.0 nowadays. It's a hot topic for society, politics and the economy. But what about digitisation in metal-working companies? What does it mean for joining technology with its various welding processes? What is the impact of digital networking on systems and components and how do companies stand to benefit? The focus here is on cost effectiveness and competitiveness.
Analysing, optimising and documenting welding parameters. Ensuring stable welding processes with minimal distortion and thereby boosting cost effectiveness at the same time. These are all challenges that metal-working companies are facing in order to maintain their competitiveness for the future. Widescale digitisation plays an important role here.
For example, Fronius runs a prototyping centre at the Wels site, where a number of digital solutions for welding technology and other high-tech equipment are already being used. While the prototyping centre of course offers companies the option of outsourcing their prototyping activities, it also provides an example of how Industry 4.0 can look in practice.
"Offline" programming: lower downtime costs and higher output
Companies are already programming their welding processes "offline" to boost efficiency, as the work can take place away from the actual robot welding systems – just like at the Fronius prototyping centre. As a result, welding engineers no longer need to wait around until the live welding work has been completed to configure the robot for new tasks. Instead, they can define and simulate all welding sequences seam for seam from the outset.
Offline programming and simulation software such as the Fronius Pathfinder detects axis limits and calculates start points, end points and access routes. The software also sets positioning points independently. Obstacle contours are visualised and torch positions corrected simultaneously – right from the start and not just during the initial welding trials. Offline programming and simulation optimise the welding process, boost productivity and eliminate unnecessary downtime costs.
Efficient and resource-conserving: robot-assisted surface cleaning using hot plasma technology
Foreign particles and sealing film must be removed from metal surfaces before welding to achieve high-quality welded joints such as those required in the automotive industry. In the past, large quantities of chemical cleaning solutions were often necessary and the entire surface of a component would typically need to be treated. However, it is now possible to remove organic and film-related dirt deposits extremely efficiently as part of Industry 4.0.
The Acerios surface cleaning system from Fronius uses hot active plasma to clean component surfaces. The robot takes the welding torch and its plasma flame at 1,000 degrees Celsius to precisely the areas that need to be cleaned; in other words, where welding is set to take place. The cleaning plasma then moves over the metal surfaces at a rate of around six metres per minute. This provides a significant boost to efficiency because, rather than cleaning as much as possible, Acerios cleans as much as necessary. This is easy on the finances as well as on environmental resources.
Prerequisite for forward-looking arc control: state-of-the-art, high-tech equipment
But how is it possible to produce stable and low-spatter welding processes that achieve excellent root fusion, a high deposition rate with reduced energy per unit length, stable penetration behaviour or constant arc lengths? Digital welding systems with high computing power, enormous memory capacities, extremely quick bus systems and, last but not least, highly dynamic wirefeeders provide the answer here. For these kinds of systems, Fronius offers the TPS/i high-tech welding system platform. Innovative welding processes and process variants go hand in hand with this solution.
LSC (Low Spatter Control), for instance, is characterised by high arc stability and significantly reduced welding splatter. PMC (Pulse Multi Control) boasts features such as an improved pulse correction function and a refined SynchroPulse process. Both welding processes include penetration and arc length stabilizers. PCS (Pulse Controlled Spray Arc) in turn enables users to switch smoothly between pulsed arc and spray arc, doing away with the problematic intermediate arc.
These kinds of innovative welding processes and characteristics generally make welding systems easier to operate, save on time and improve the quality of weld seams.
Innovative and cost effective: the wire electrode as a sensor for automatic corrections
Automated, completely autonomous welding with defect-free weld seams – that is the vision. Welding systems should compensate for air gaps, clamping tolerances and other imperfections independently. With WireSense, SeamTracking and TouchSense, Fronius offers innovative assistance systems for various applications that significantly improve welding efficiency. With their support, welding robots are able to adapt their programs to weld runs completely independently.
This saves on a significant amount of rework and, in the case of deviations, it also saves on the time and effort spent on reprogramming robot paths at a later date. All three assistance systems thereby use the wire electrode not just as filler metal, but rather also as a sensor. There are no restrictions on component accessibility, unlike most instances where laser or camera sensor systems are used. Companies thereby avoid maintenance work and expenses for additional sensor hardware.
Real-time arc monitoring using a camera
The latest ArcView camera system from Fronius provides a direct view of the arc, guaranteeing real-time monitoring of the ongoing welding process. In combination with TPS/i power sources, ArcView generates pulse-controlled images – precisely in the dark phases of the arc. The system thereby provides high-resolution images, where images with different exposure times are combined to form a detailed HDR image. If necessary, the welding engineer can take immediate corrective action.
Welding data management with web-based software solutions
Transparency, security, productivity and time savings are common requirements when it comes to welding production processes. Welding data therefore has to be recorded for documentation and analysis purposes. Immediate feedback from the production line helps to optimise processes. System statuses can also be monitored and errors detected to ensure safe and high-quality production as a result.
The Fronius WeldCube data documentation software stores all relevant data from the welding process and makes it possible to track each individual weld seam. On top of this, all WeldCube versions are web-based software solutions, which means they can be used both on a computer as well as on mobile devices and users can view details of every single weld seam. The system documents the progress of welding work and evaluates each individual weld seam using a traffic light system.
Cameras and robots: precise measurement of welded components
A modern optical measuring system – just like the one used at the Fronius prototyping centre – checks distortion and component deviations against the CAD design data for the components. A robot positions a special measuring camera at various points on the component for this purpose. Before the pictures are taken, a light grid is superimposed on the components.
The system uses this light grid to detect the contours of the component and generate a three-dimensional image. Special software then detects and evaluates any deviations from the original design data (welding sequence, distortions, etc.). Not only do the results from the measurement data support quality control, but they also result in the continuous optimisation of the joining work.
High level of autonomy: robotic welding systems with digitally networked components
Various components of all shapes and sizes call for intelligent welding concepts. Fronius Welding Automation uses the platform approach when it comes to robotics. This makes it possible to combine standardised components in a customer-specific welding system. Welding robots, handling robots and positioners are all used here. Changeover stations for welding torches, contact tips, gripper deposit systems, part lock gates for transportation and automated shelving systems have also been integrated.
Digital networking of all these components and their central system controller guarantees fully automated welding and component handling processes. This in turn ensures a high level of autonomy. Interfaces are also available to common ERP systems and a web API has been developed for exchanging data with third-party systems.
www.fronius.co.uk
Construction News
02/06/2021
Intelligent Welding Process Management As A Competitive Advantage
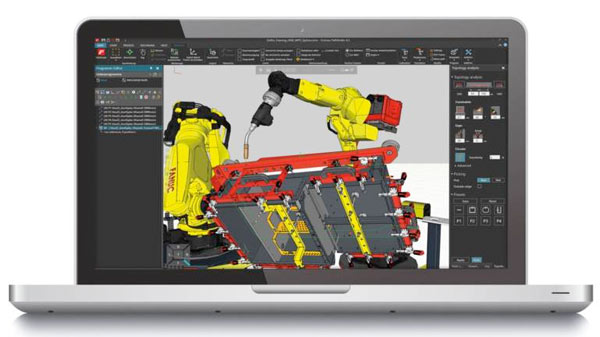
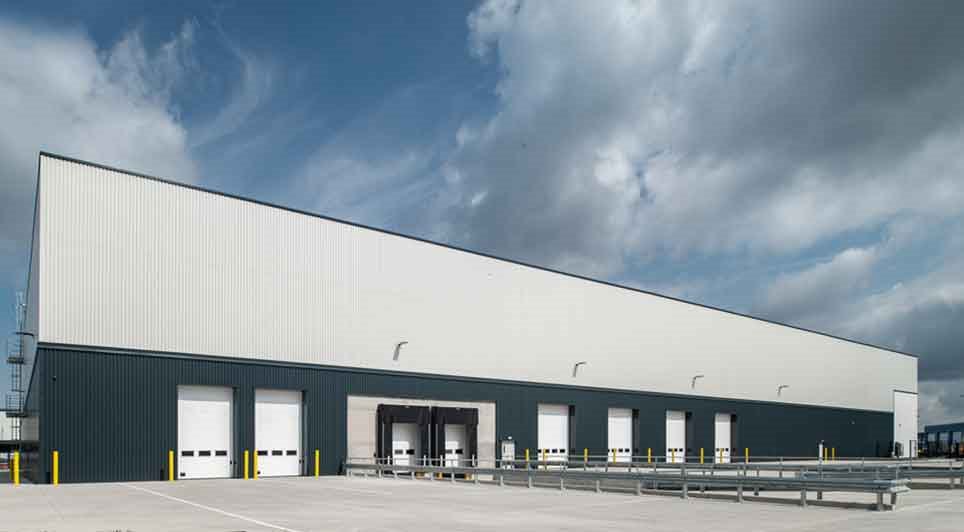
20/06/2025
McLaren Construction Midlands and North has completed the £12.8 million B4 industrial scheme at Manchester Airport, marking a significant step in the ongoing regeneration of the World Freight Terminal.
Delivered in partnership with Columbia Threadneedle Investments, the high-spec 92,000 sq. ft. un
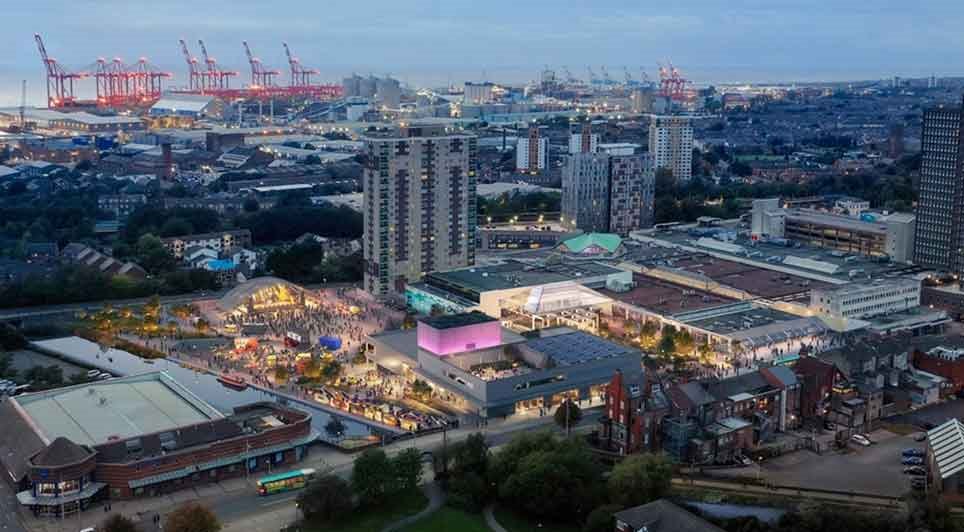
20/06/2025
Demolition work has officially begun at Bootle Strand, marking the first major step in Sefton Council's regeneration project to reshape the town centre.
Carried out by VINCI Construction UK, the works are part of Phase One of the Bootle Strand Transformation Project, which aims to create a more ac
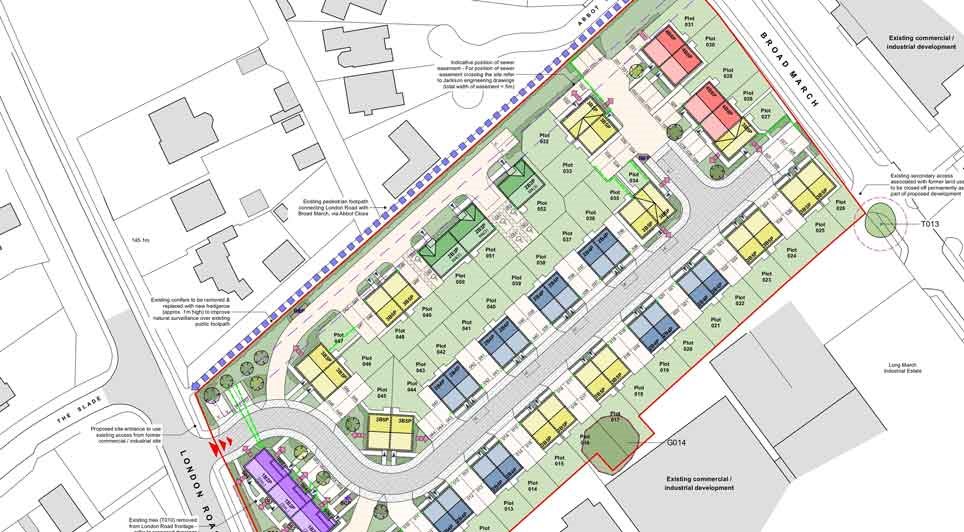
20/06/2025
Construction has commenced on a major new eco-friendly housing development in Daventry, as Midlands-based housebuilder Morro Partnerships breaks ground on a 52-home scheme designed with sustainability and social value at its heart.
The £12.6 million project, commissioned by housing provider emh gro
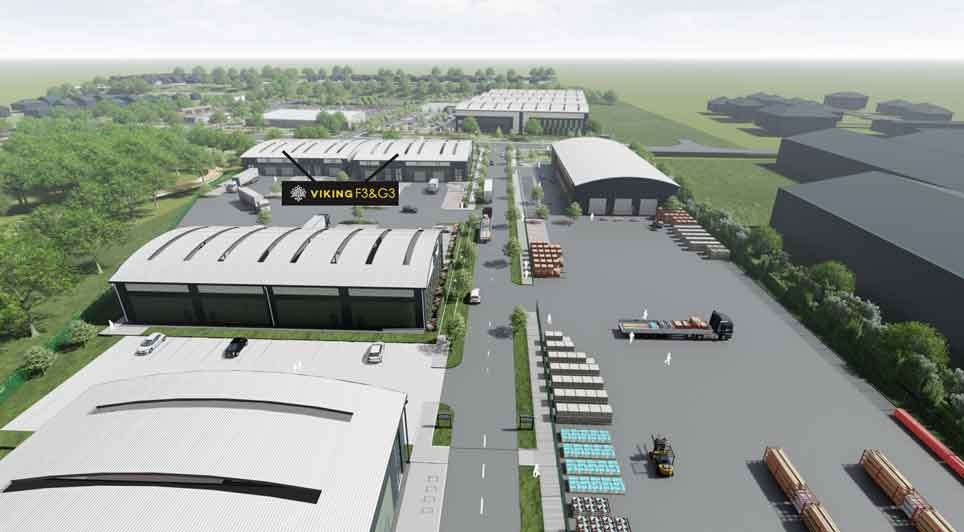
20/06/2025
Clowes Developments has completed Phase One of its Viking Park scheme in Congleton, with all units now fully let.
Building on the success of the initial phase, the company has launched Phase Two, introducing two new high-quality industrial, trade counter, or warehouse units to the market.
The nex
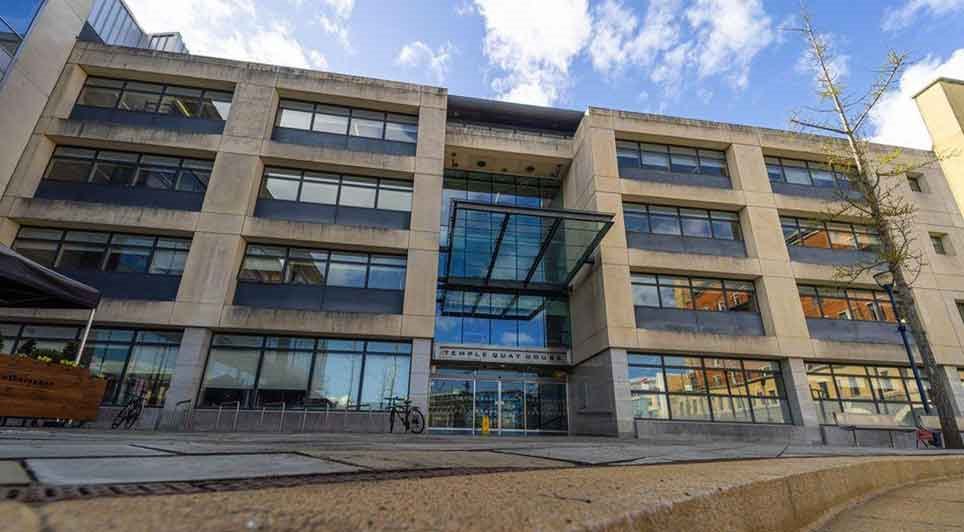
20/06/2025
BAM's transformation of Temple Quay House in Bristol is redefining what sustainable public infrastructure can achieve, earning national recognition with a Silver Considerate Constructors Scheme (CCS) Award.
Delivered without any demolition, the project retained and reimagined the existing structure
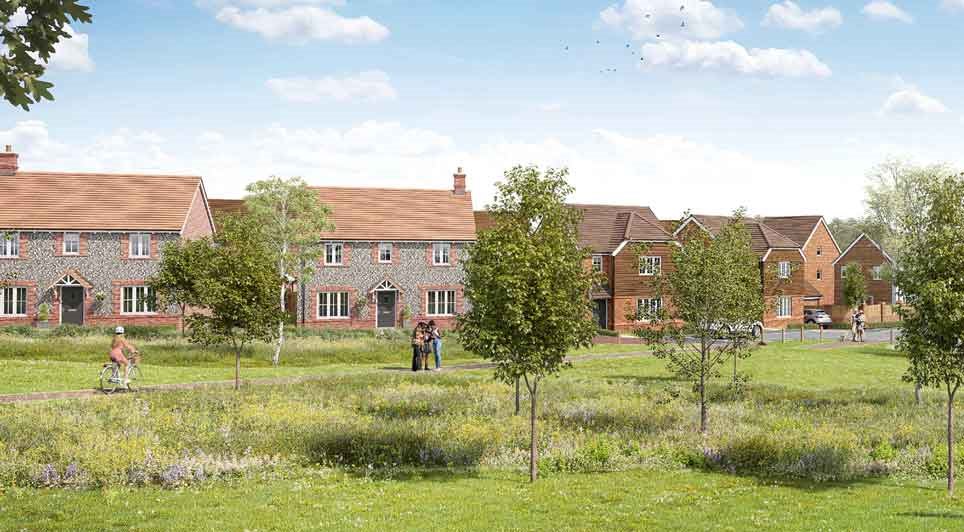
20/06/2025
Thames Valley has received unanimous approval from Adur District Council's planning committee for Phase 2 of the Malthouse Meadows development in West Sompting.
The next phase of the project will deliver 91 new homes, including 27 designated as affordable housing for those not served by the open ma
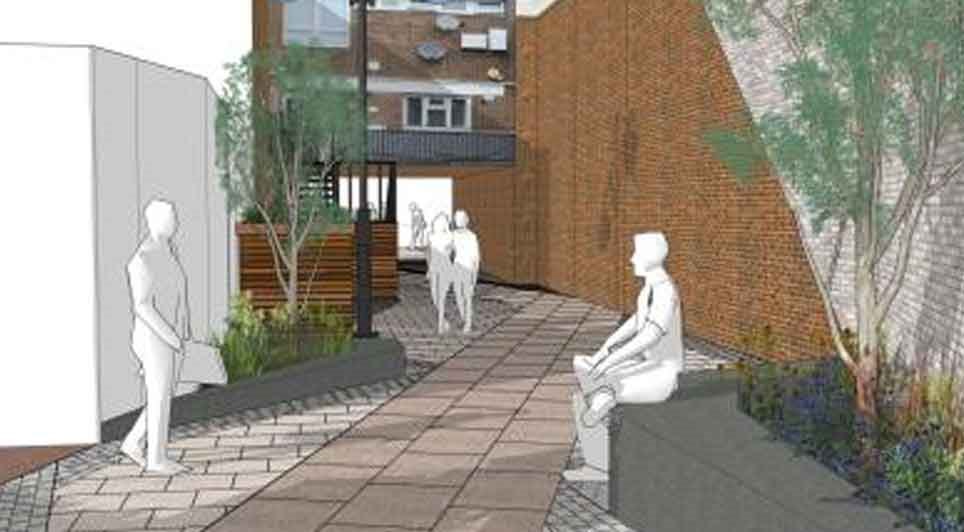
20/06/2025
City of Wolverhampton Council has appointed Taylor Woodrow to deliver a major improvement scheme for Wednesfield High Street, with initial investigatory works scheduled to begin next week.
From Monday 23 June to Friday 27 June, Taylor Woodrow will carry out underground service and drainage surveys,
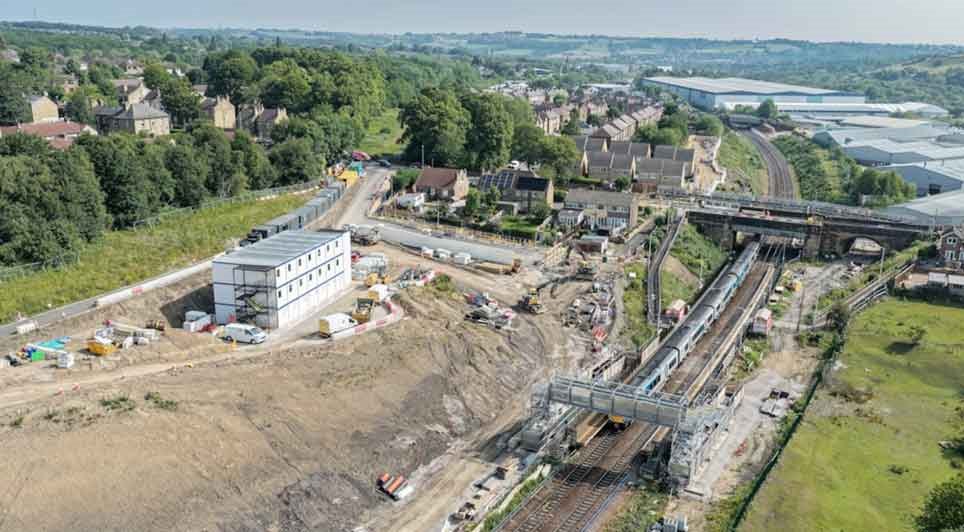
20/06/2025
Deighton station will temporarily close from Saturday 30 August as part of the Transpennine Route Upgrade (TRU), a multi-billion-pound programme set to transform rail travel across the North of England.
The station is expected to reopen in 2027 with a completely rebuilt, modernised layout designed
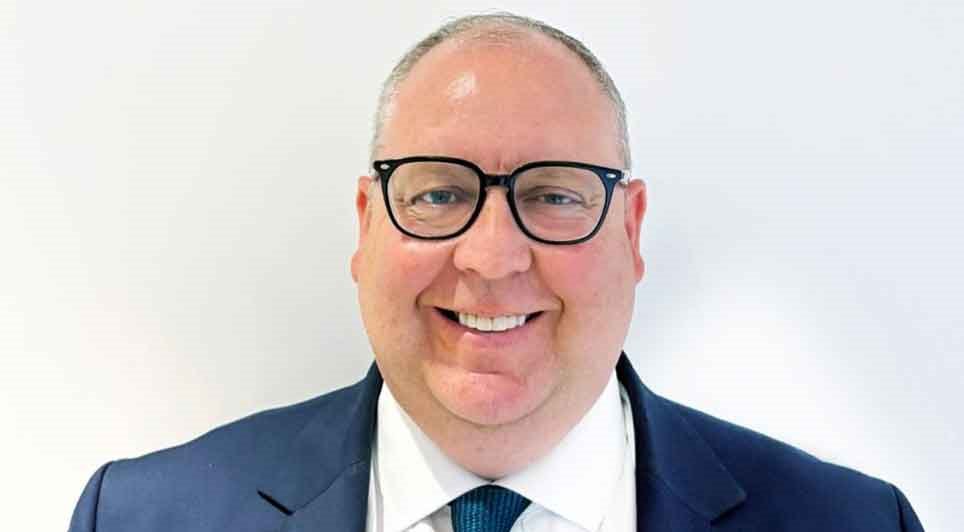
20/06/2025
Wates Group has announced the appointment of Pat Fitzgerald as its new Chief Commercial Officer, effective from 1 September 2025.
He will succeed Simon Potter, who retired earlier this year.
A chartered quantity surveyor, Fitzgerald brings over three decades of experience in commercial and operat
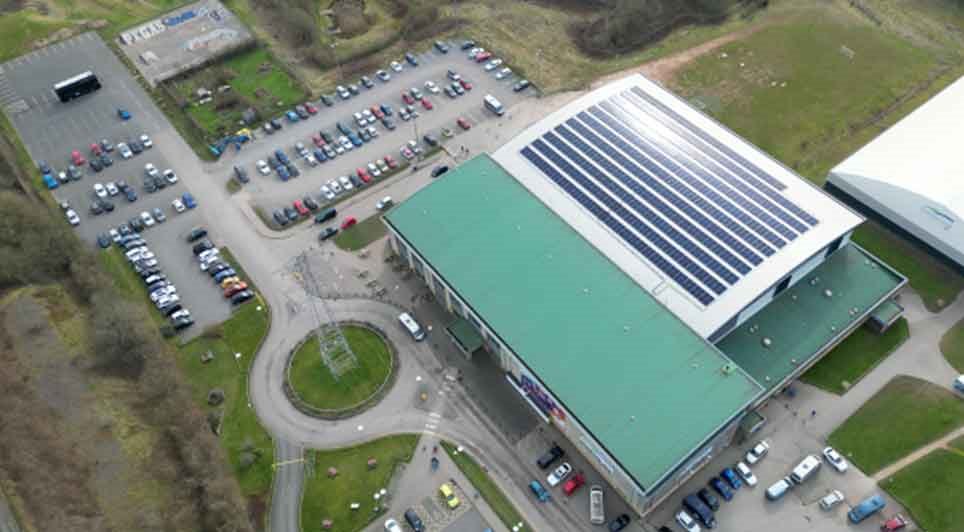
20/06/2025
Coventry City Council, in partnership with CV Life, has completed a series of sustainability upgrades at three of the city’s key leisure centres.
The works were funded by almost £750,000 in grant support from the Department for Culture, Media and Sport and the National Lottery through Sport Englan