Construction News
06/12/2021
London Concrete Completes Seven-Day Slipform Pour At Slough Multifuel
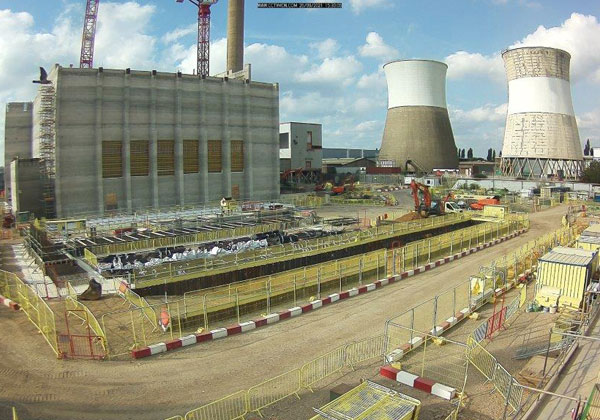
London Concrete, part of the Aggregate Industries business, has successfully completed a week-long continuous slipform pour after delivering 3,300m3 of ECOPact low carbon concrete over seven days for SSE and joint venture partner CIP, for new energy-from-waste (EfW) project, Slough Multifuel.
Together with Hitachi Zosen Inova, the Principal Contractor, and Careys, who are a specialist civils contractor, work on the construction of the new £400million EfW facility, located within Slough Trading Estate, began earlier this year and will be fully operational by 2024. It will provide a more sustainable waste management solution for the Greater London area, by processing 480,000 tons of residual waste per annum, and will contribute to the UK government's strategy to reduce landfill and export of waste.
By utilising residual waste as a renewable energy source, Slough Multifuel will offset more than 147,000 tons of CO2 per year and power more than 100,000 homes. Moreover, the project is bringing hundreds of local jobs to the area during construction as well as around 50 permanent jobs in the operations phase.
Construction of the main waste bunker at the new facility commenced earlier this year. London Concrete was brought in to assist the civils contractors Careys and GB Slipform in the delivery of a 24/7 concrete supply, with Aggregate Industries' low carbon concrete, ECOPact Prime, specified to deliver the workability performance needed for a slipform of this size whilst meeting the challenge set to reduce the embodied carbon of concrete.
A decision was made early in the process to adopt slipform to help significantly reduce the amount of construction joints in the walls of the waste bunker and ensure a completely watertight structure. It was also essential to make the bunker resistant to chemical attack and therefore the concrete needed to be DC-3 class compliant. However, the immense size of the bunker posed a significant challenge, taking seven days and nights to complete. Furthermore, use of ECOPact Prime, an engineered low carbon concrete that utilises higher blends of cement substitutes such as GGBS, presented challenges for slipforming when it came to setting times and compressive strengths.
Jamie Hamill, Contracts Manager at Careys, explained: "We needed to carry out a number of samples of the different types of concrete mixes to make sure we got the right consistency and strength gain. We knew if the concrete went off too quickly in the shutter, then there would be little time to pour it correctly, there would be risks of blockages in the pumps, the rig would need to slide quicker to keep up and everyone would become under increasing pressure to work faster. This, we knew, would risk a poor finish, or the quality being jeopardised.
"On a big slide like this, you need to be slow and steady, so that you are always under control. The flipside is, however, if the concrete takes too long to go off, it is difficult to speed it up, which has a knock-on effect on the project time and cost. Getting the concrete right is not an exact science as there are lots of different factors that can affect its strength, hence why testing samples in a relative sample size to determine how quickly we wanted the concrete to set was so important on this project. We did this over a few weeks, and we got the correct strength."
Daniel King, Managing Director for London Concrete, added: "The project brief was certainly interesting! An eight-day continuous pour using a low carbon concrete that, by design, with its high GGBS content, is not typically used in slipform construction. However, trials carried out over a two-week period at our Heathrow plant, followed by frequent batch testing and 24/7 supervision during the pour, ensured we could supply a mix design that was optimised for performance while also maintaining the sustainability credentials of the build through use of a low carbon concrete. Overall, we were able to deliver a total carbon reduction of 42%, a saving of 608,951kg or 609 tonnes of eCO2 in comparison to a standard slipform mix."
Those interested in Aggregate Industries' ECOPact range can get a clear understanding of their individual requirements and potential carbon savings through using Aggregate Industries' simple to use carbon calculator. The calculator, which includes over 100 different mixes, recommends all of the available ECOPact options together with the embodied carbon for each level, making the product selection much easier. In addition, Aggregate Industries has an experienced technical team on hand to discuss options or project specific carbon calculations if required.
Together with Hitachi Zosen Inova, the Principal Contractor, and Careys, who are a specialist civils contractor, work on the construction of the new £400million EfW facility, located within Slough Trading Estate, began earlier this year and will be fully operational by 2024. It will provide a more sustainable waste management solution for the Greater London area, by processing 480,000 tons of residual waste per annum, and will contribute to the UK government's strategy to reduce landfill and export of waste.
By utilising residual waste as a renewable energy source, Slough Multifuel will offset more than 147,000 tons of CO2 per year and power more than 100,000 homes. Moreover, the project is bringing hundreds of local jobs to the area during construction as well as around 50 permanent jobs in the operations phase.
Construction of the main waste bunker at the new facility commenced earlier this year. London Concrete was brought in to assist the civils contractors Careys and GB Slipform in the delivery of a 24/7 concrete supply, with Aggregate Industries' low carbon concrete, ECOPact Prime, specified to deliver the workability performance needed for a slipform of this size whilst meeting the challenge set to reduce the embodied carbon of concrete.
A decision was made early in the process to adopt slipform to help significantly reduce the amount of construction joints in the walls of the waste bunker and ensure a completely watertight structure. It was also essential to make the bunker resistant to chemical attack and therefore the concrete needed to be DC-3 class compliant. However, the immense size of the bunker posed a significant challenge, taking seven days and nights to complete. Furthermore, use of ECOPact Prime, an engineered low carbon concrete that utilises higher blends of cement substitutes such as GGBS, presented challenges for slipforming when it came to setting times and compressive strengths.
Jamie Hamill, Contracts Manager at Careys, explained: "We needed to carry out a number of samples of the different types of concrete mixes to make sure we got the right consistency and strength gain. We knew if the concrete went off too quickly in the shutter, then there would be little time to pour it correctly, there would be risks of blockages in the pumps, the rig would need to slide quicker to keep up and everyone would become under increasing pressure to work faster. This, we knew, would risk a poor finish, or the quality being jeopardised.
"On a big slide like this, you need to be slow and steady, so that you are always under control. The flipside is, however, if the concrete takes too long to go off, it is difficult to speed it up, which has a knock-on effect on the project time and cost. Getting the concrete right is not an exact science as there are lots of different factors that can affect its strength, hence why testing samples in a relative sample size to determine how quickly we wanted the concrete to set was so important on this project. We did this over a few weeks, and we got the correct strength."
Daniel King, Managing Director for London Concrete, added: "The project brief was certainly interesting! An eight-day continuous pour using a low carbon concrete that, by design, with its high GGBS content, is not typically used in slipform construction. However, trials carried out over a two-week period at our Heathrow plant, followed by frequent batch testing and 24/7 supervision during the pour, ensured we could supply a mix design that was optimised for performance while also maintaining the sustainability credentials of the build through use of a low carbon concrete. Overall, we were able to deliver a total carbon reduction of 42%, a saving of 608,951kg or 609 tonnes of eCO2 in comparison to a standard slipform mix."
Those interested in Aggregate Industries' ECOPact range can get a clear understanding of their individual requirements and potential carbon savings through using Aggregate Industries' simple to use carbon calculator. The calculator, which includes over 100 different mixes, recommends all of the available ECOPact options together with the embodied carbon for each level, making the product selection much easier. In addition, Aggregate Industries has an experienced technical team on hand to discuss options or project specific carbon calculations if required.
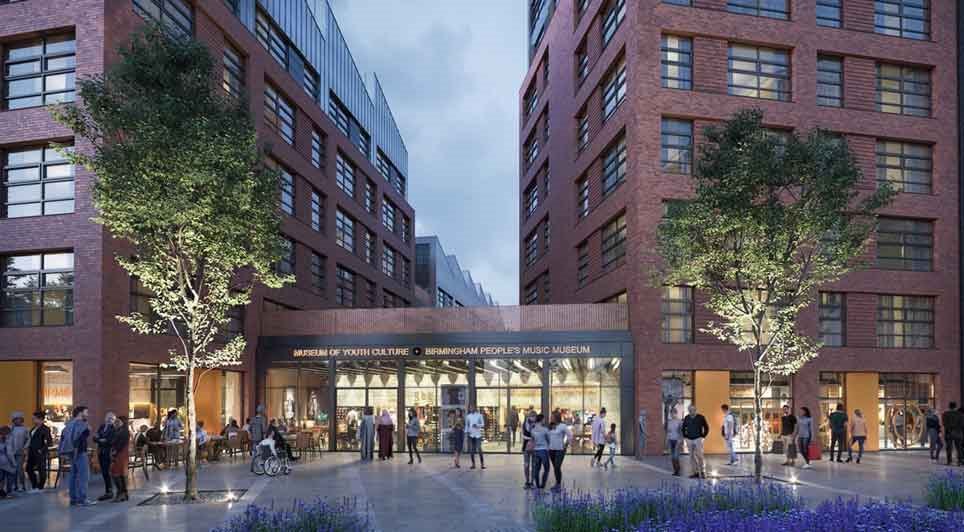
29/01/2025
Caddick Construction has been awarded a £43 million contract to deliver the first phase of Cole Waterhouse's flagship regeneration scheme in Digbeth, Birmingham.
The project, known as Upper Trinity Street, marks a significant step in the area’s transformation.
Spanning 182,986 square feet, the re
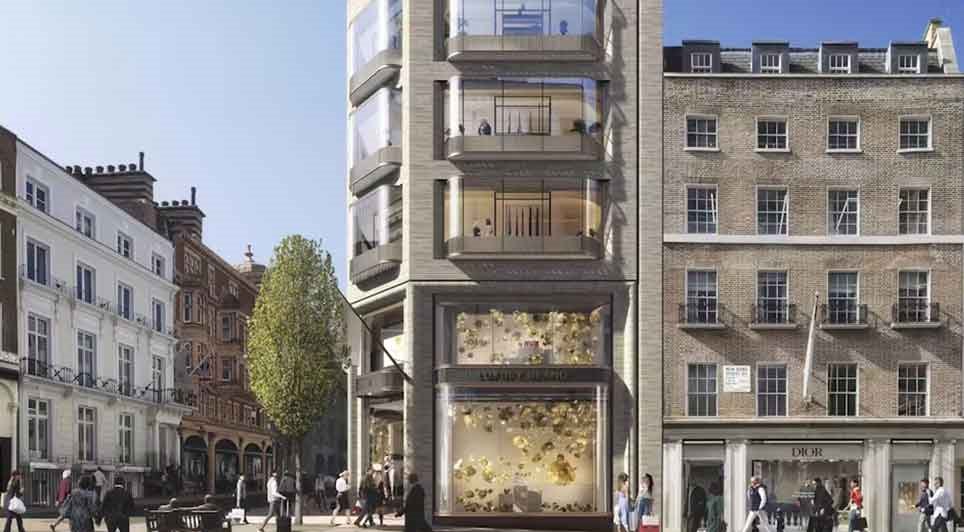
29/01/2025
McLaren Construction has been appointed by O&H Properties to deliver the first phase of a £60 million Foster & Partners-designed development at the corner of New Bond Street and Grafton Street in London’s West End.
The seven-storey, 5,400 square metre prime retail and office scheme will feature ret
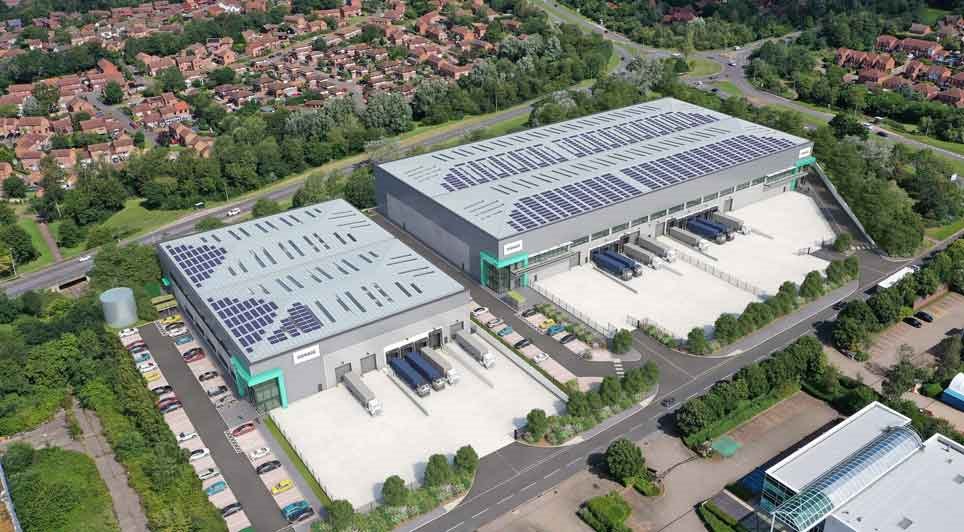
29/01/2025
GMI Construction Group has been awarded a contract to develop three high-specification warehouse units totalling over 175,000 square feet at Precedent Drive, Milton Keynes.
The £20 million project, commissioned by DV5 Last Mile Developments (UK) Ltd, a joint venture between Coltham and Delancey Re
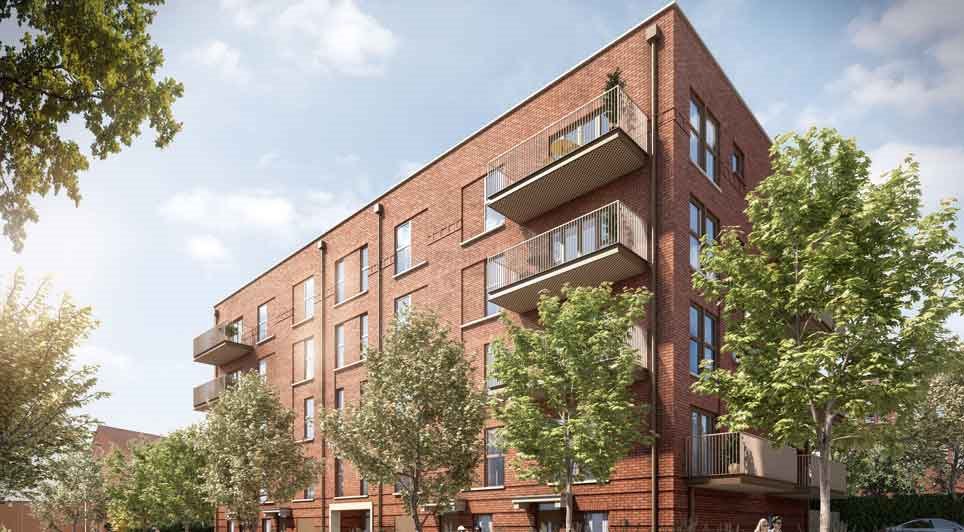
29/01/2025
Plans for 106 sustainable new homes in Southville, a neighbourhood in South Bristol, have been approved as the city seeks to increase housing delivery to address growing demand.
Top 10 award-winning housebuilder The Hill Group will create a £60 million development on Raleigh Road, on land that was
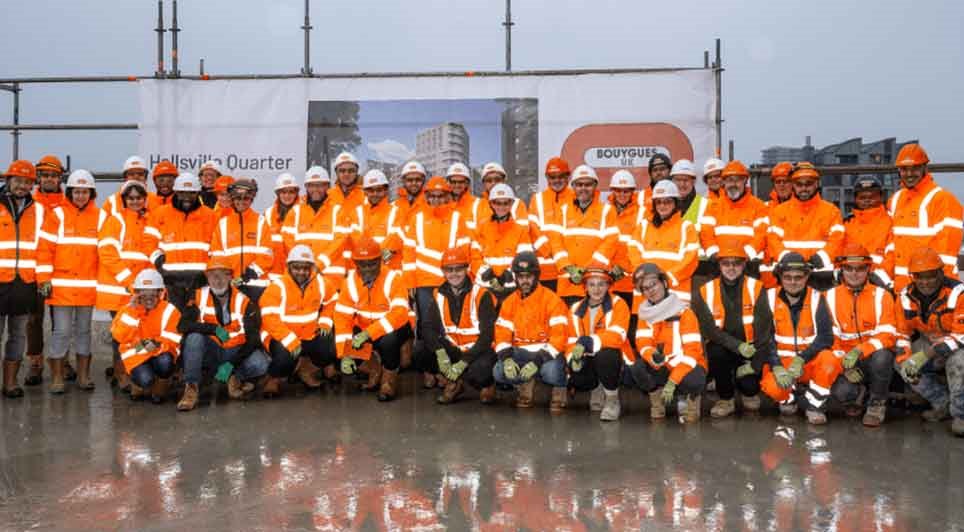
29/01/2025
Bouygues UK has reached a major milestone in the fourth phase of the Hallsville Quarter regeneration project in Canning Town, London.
The project, part of the £3.7 billion Canning Town and Custom House Regeneration Programme, recently held a topping out ceremony, marking the completion of the 11-s
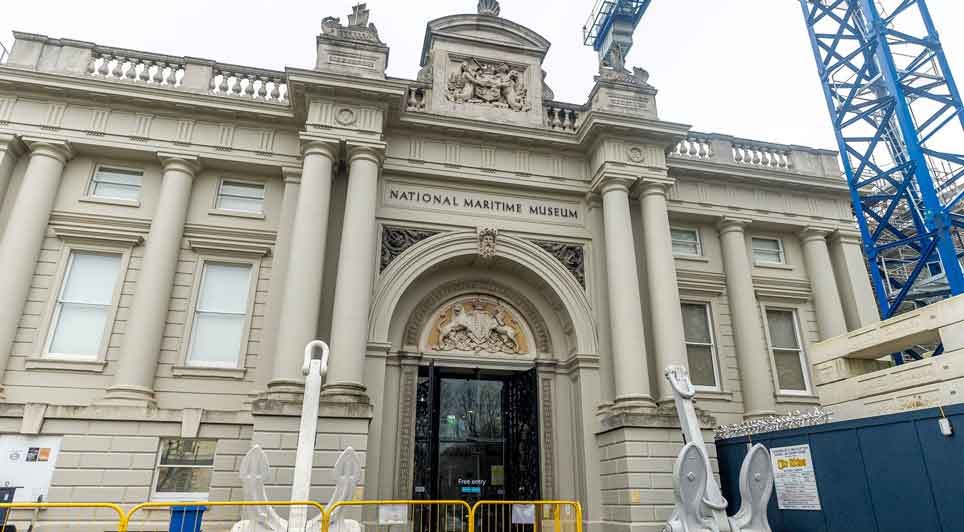
29/01/2025
Willmott Dixon Interiors is carrying out a significant upgrade to the roof of the National Maritime Museum in Greenwich, one of London's most iconic cultural landmarks.
As part of the £12 million project, the company is installing over 23,000 square feet of sun-protected glazing above the museum’s
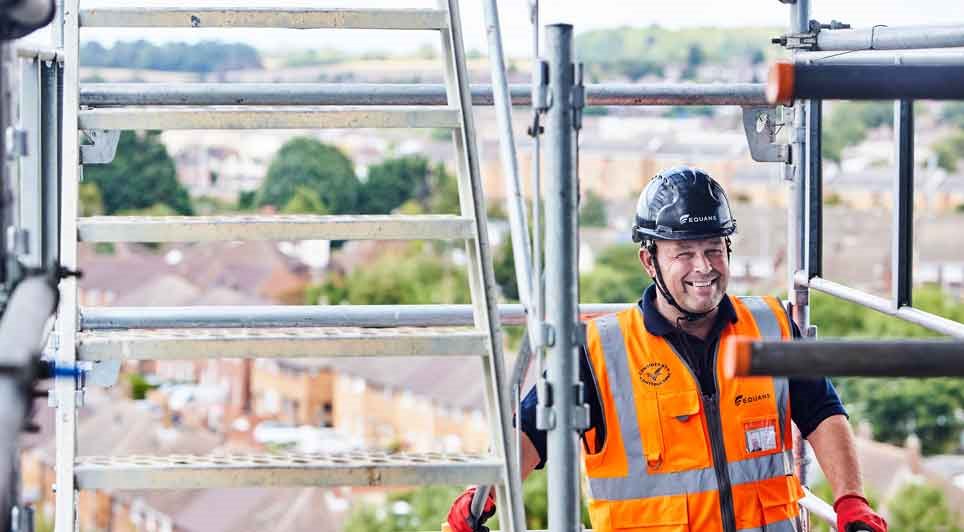
29/01/2025
Equans has been appointed by Babergh and Mid Suffolk District Councils to carry out crucial decarbonisation work across the councils' housing stock, using funding secured through the Social Housing Decarbonisation Fund (SHDF).
The councils used the South East Consortium's Zero Carbon Framework to s
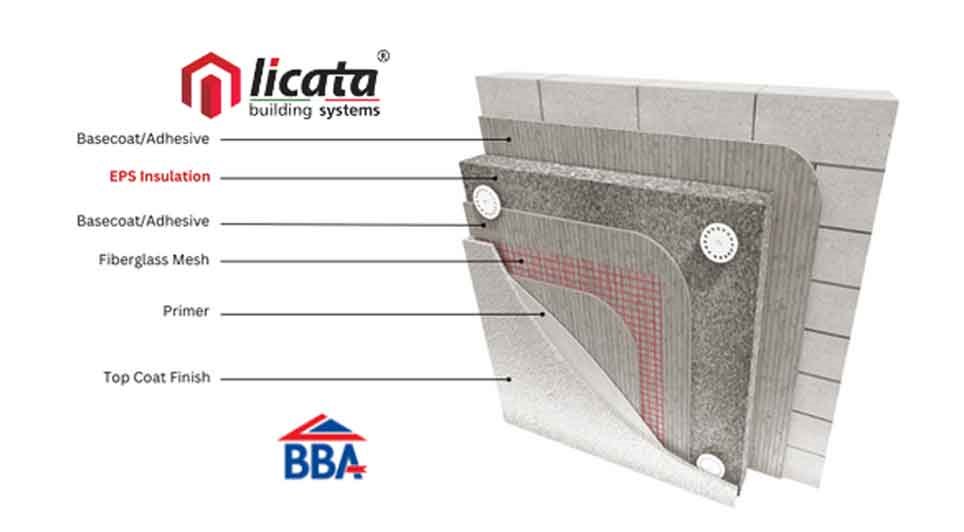
29/01/2025
In the world of construction, the quest for energy efficiency and sustainability is ever-evolving. Among the array of solutions available, EPS (Expanded Polystyrene) insulation stands out as a versatile and effective option for enhancing the thermal performance of buildings, particularly when used f
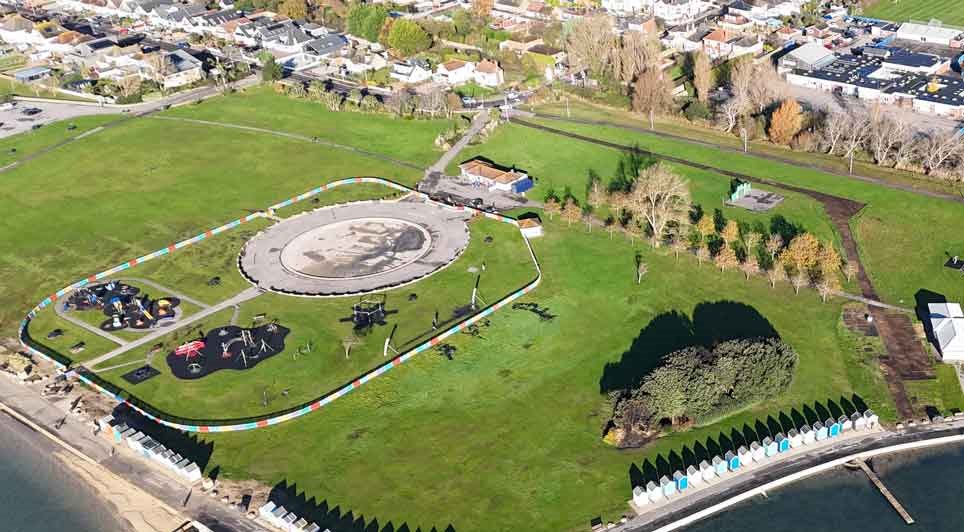
29/01/2025
BCP Council has completed significant coastal protection works at Hamworthy Park, ensuring its resilience against erosion for the next 20 years.
A 200-metre stretch of sea wall along the eastern promenade has been reinforced using low-carbon concrete, while new steps have been constructed to improv
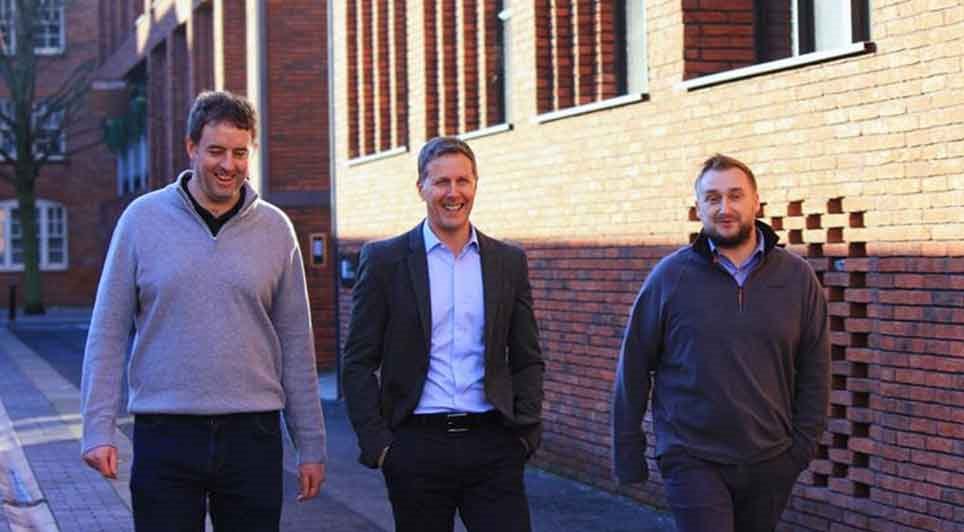
29/01/2025
Geo-environmental consultancy and remediation contractor, The LK Group, has strengthened its team with a trio of recruits.
The multidisciplinary company's latest raft of hires comprises a new director, associate director and remediation manager.
The geo-environmental specialist, headquartered i