HS2 Ltd has announced the start of construction on the railway's first and longest viaduct with the launch of an enormous 700 tonne bridge-building machine at an event attended by the HS2 Minister, Andrew Stephenson MP, just outside London.
Stretching for more than two miles (3.4km) across a series of lakes and waterways between Hillingdon and the M25, the Colne Valley Viaduct will also be the longest railway bridge in the UK.
The start of construction is the latest major milestone in the delivery of the HS2 project, which is designed to improve rail links between London, Birmingham and North, help level-up the economy and provide a low carbon alternative to car and air travel.
Mr Stephenson said: "HS2 began construction on what’s set to be Britain’s longest railway viaduct, a landmark moment for HS2 and a feat of British engineering, taking the HS2 line from London, and into Hertfordshire and Buckinghamshire.
"Infrastructure is the backbone of HS2 and this viaduct will be integral to delivering faster journeys and an increased capacity rail network."
Known as a 'launching girder', the 160m long bridge-building machine is the only one of its kind in the UK and will be used to lift the giant concrete deck segments that form the viaduct’s arches into position. Once each section is complete, the machine will inch itself forward into position to build the next stage.
A total of one thousand deck segments will be needed, with each one weighing up to 140 tonnes. To allow for the gentle curves of the viaduct as it crosses the valley, all the segments are slightly different shapes and made on site at a purpose-built temporary factory close to the north abutment.
The huge viaduct project is being led by HS2's main works contractor Align JV – a team made up of Bouygues Travaux Publics, Sir Robert McAlpine and VolkerFitzpatrick.
Originally built in 2004, the launching girder was first used during the construction of the Hong Kong East Tsing Yi Viaduct. Specially designed to handle complex viaduct construction, the machine is named ‘Dominique’ in memory of Bouygues engineer Dominique Droniou who played a leading role in its design and development.
56 piers each weighing around 370 tonnes are being constructed along the Colne Valley ahead of the girder, with the girder moving from one pier to the next, installing the deck segments as it goes. One segment is put in place each side of the central pier, using a cantilever approach to balance the structure, as two half-arches either side of each pier are constructed simultaneously. Steel tensioning cables will be threaded through the segments to strengthen the bridge.
Every segment will be a slightly different shape depending on where it fits into the viaduct and the modular approach was chosen to ensure quality, safety and efficiency.
The viaduct pre-cast factory where the segments are made at the peak of construction will cast around 12 segments every week using a ‘match-casting’ technique. This approach - where each segment is poured against the previous one - will ensure the whole deck fits perfectly when assembled on the piers. The mammoth 100m long viaduct precast factory, which is visible from the M25, has an internal volume of 105,000 cubic metres – making it larger than the Royal Albert Hall.
Once construction is complete, the factory and surrounding buildings will be removed and the whole area between the viaduct and the Chiltern tunnel will be transformed into an area of chalk grassland and woodland as part of HS2’s 'green corridor' project.
The design of the Colne Valley Viaduct was inspired by the flight of a stone skipping across the water, with a series of elegant spans, some up to 80m long, carrying the railway around 10m above the surface of the lakes, River Colne and Grand Union Canal.
Set low into the landscape, wider spans will carry the viaduct crosses the lakes, with narrower spans for the approaches. This design was chosen to enable views across the landscape, minimise the viaduct’s footprint on the lakes and help complement views across the natural surroundings.
In another visible sign of progress on the project, the team have also completed the construction of three of four jetties across the lakes to get equipment into position to support the construction and help take construction vehicles off local roads. Where the viaduct crosses the lakes, the piles are being bored directly into the lakebed, using a cofferdam to hold back the water while the pier is constructed.
Construction News
01/06/2022
Construction Begins On UK's Longest Railway Bridge
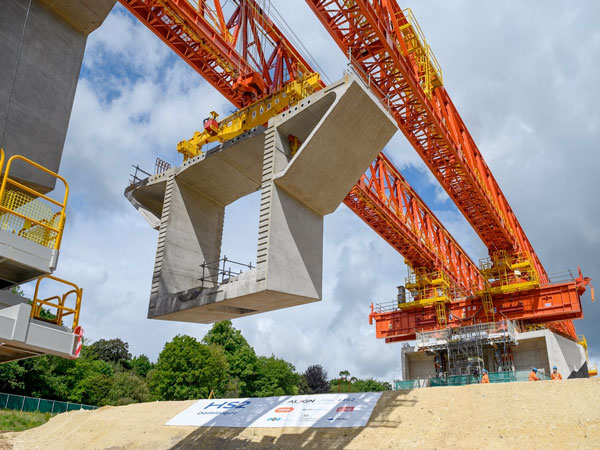
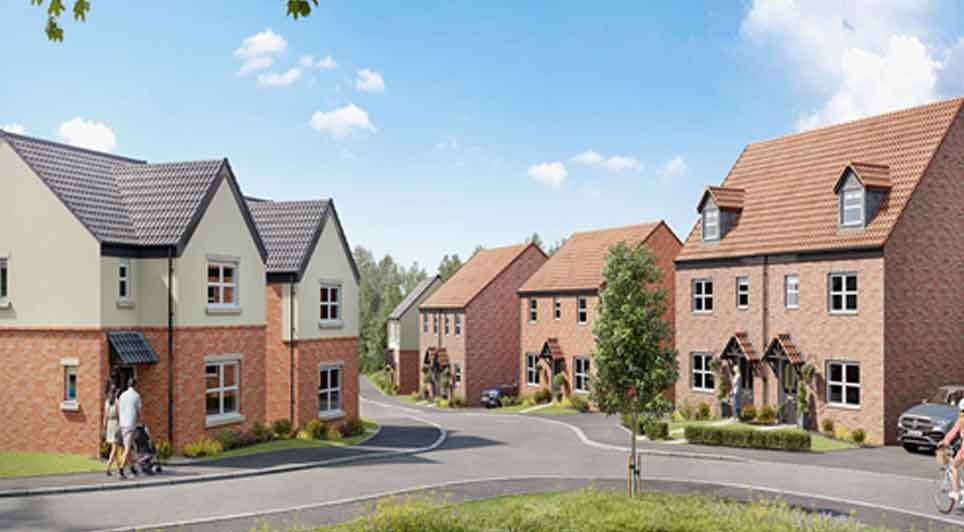
02/04/2025
Hinckley and Bosworth Councillors have approved plans for more than 300 new homes across two key locations, marking a significant expansion in local housing development.
Persimmon Homes North Midlands has received the green light for 81 new homes in Earl Shilton. Of these, 16 homes will be availabl
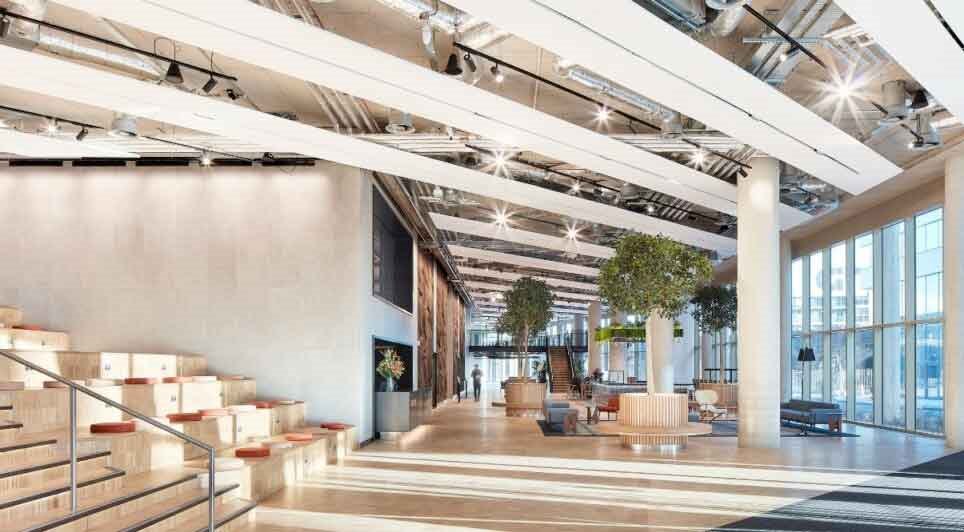
02/04/2025
Wates has completed the Welcome Building®, a 207,000 sq ft, nine-storey commercial space in Bristol.
The project, developed as a joint venture between Trammell Crow Company and EPISO 5, a fund managed by Tristan Capital Partners, sets a new benchmark for sustainability, wellbeing and community eng
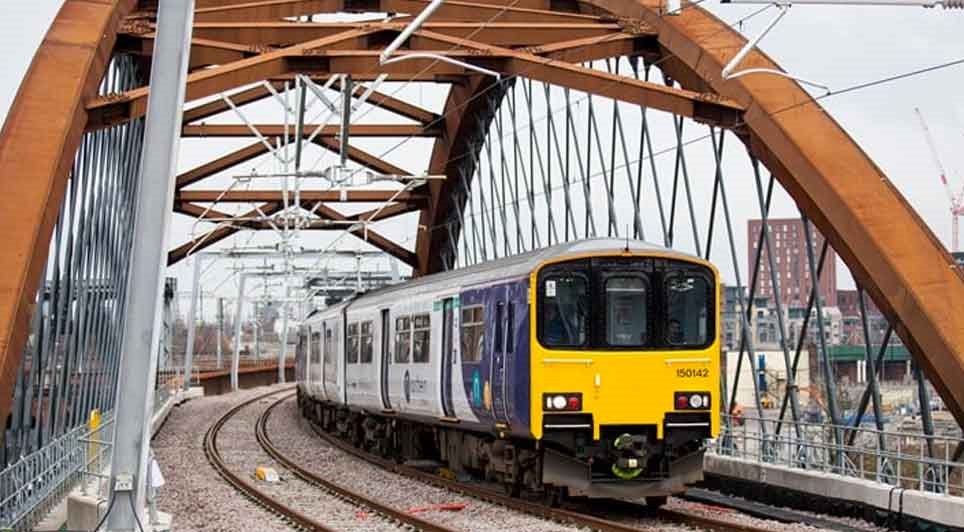
02/04/2025
Skanska, in partnership with an Arup and SYSTRA 50/50 joint venture, has secured a position as a strategic delivery partner on Network Rail’s Eastern Region Development and Design Partnership Framework (DDPF).
The £300 million framework spans five years, with the potential for a three-year extensio

02/04/2025
New lifts and a footbridge have officially opened at Newtown station in Powys, making both platforms fully accessible to all passengers for the first time.
Network Rail and contractor AmcoGiffen began work on the project in December 2023. While the main infrastructure is now complete, additional wo
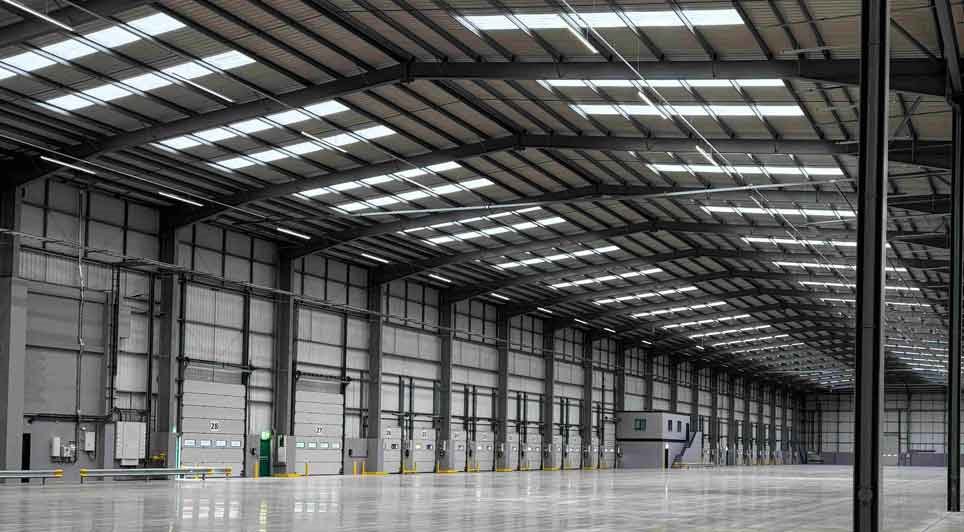
02/04/2025
Pexhurst has wrapped up a strong first quarter of 2025, completing several refurbishment projects across multiple sectors with a combined value of nearly £15 million.
The projects supported clients in Pexhurst's key sectors, industrial and logistics, as well as office refurbishments, across the Sou
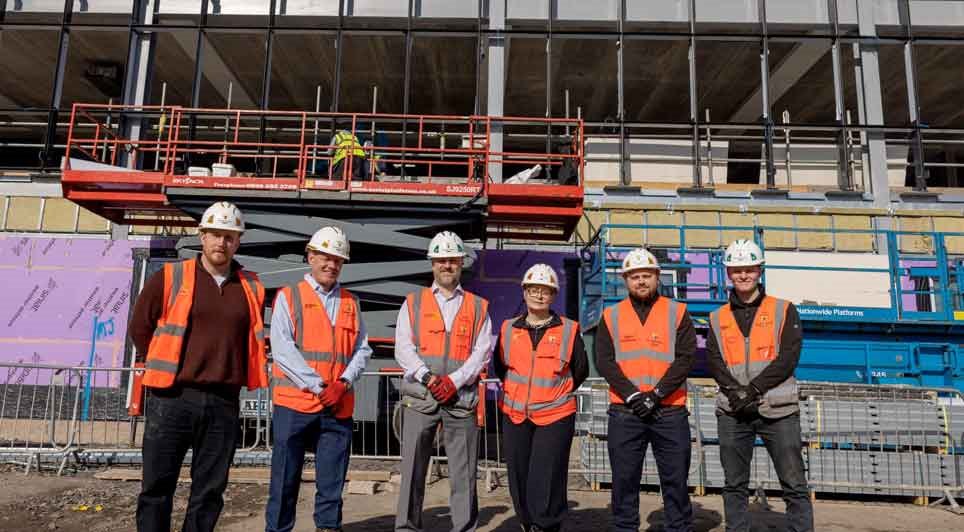
02/04/2025
Willmott Dixon joined officers and staff from Lancashire Police, alongside Lancashire Police and Crime Commissioner (PCC) Clive Grunshaw, to celebrate the topping out of the new Pendle Police Station in Nelson.
With the external structure now complete, the focus will shift to interior work to ensur
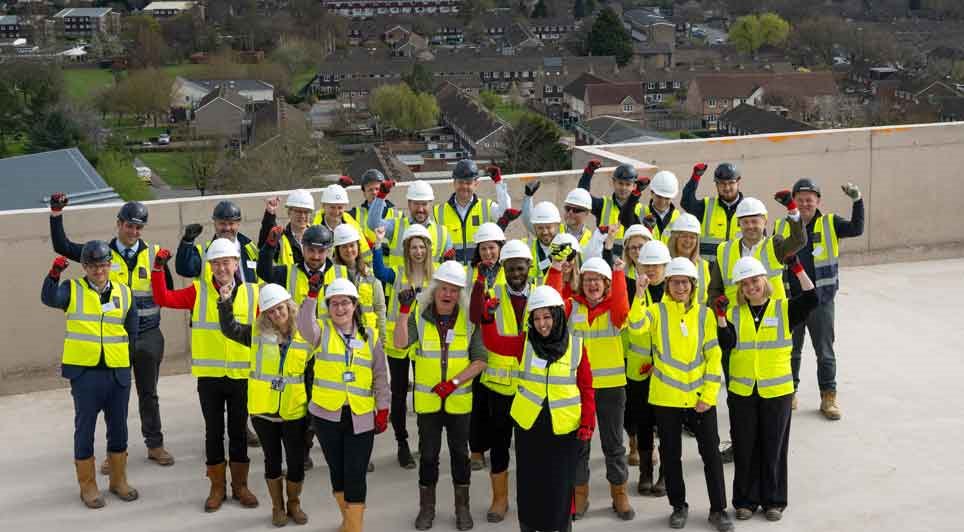
02/04/2025
The first affordable homes in the regeneration of Oxford's Blackbird Leys are set to welcome new residents from this summer.
A total of 84 shared ownership homes, currently being built by Peabody and Oxford City Council at Knight’s Road, will be released in phases between this summer and next sprin
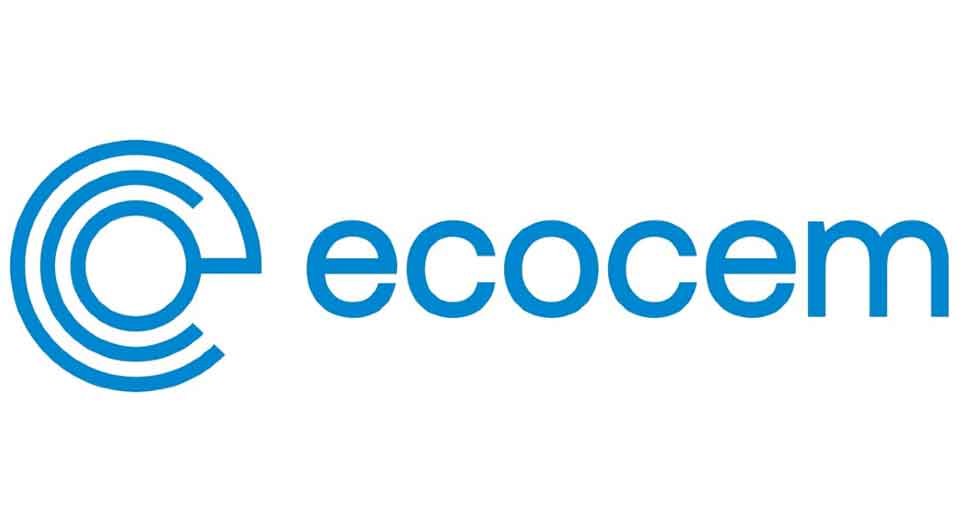
02/04/2025
Ecocem, Europe's leader in low-carbon cement technologies, has announced the signing of a partnership agreement with TITAN Group, a leading international business in the building and infrastructure materials industry, to co-develop and deliver innovative low-carbon cements.
Focusing initially on th
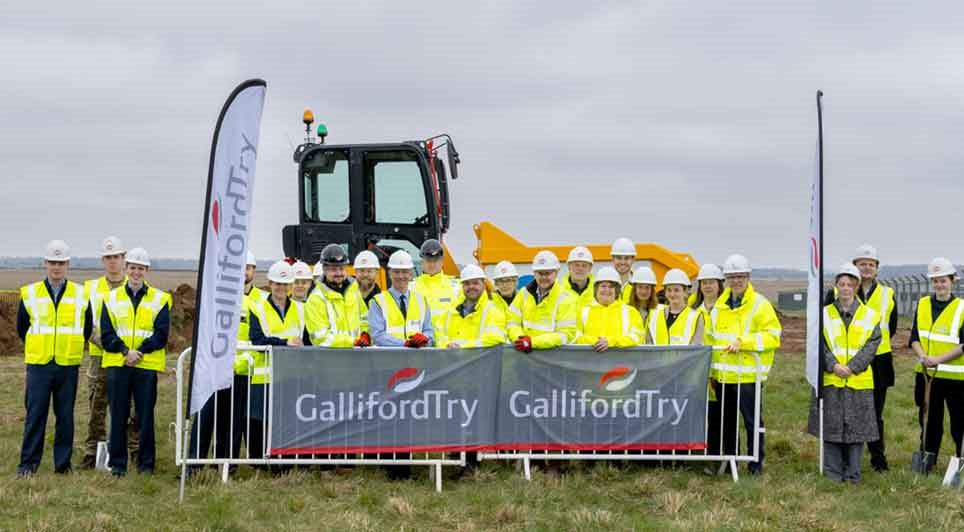
01/04/2025
Galliford Try's Building East Midlands business has officially broken ground on a £63 million Single Living Accommodation (SLA) project at RAF Digby, Lincolnshire.
The historic base, the Royal Air Force's oldest station established in 1918, will see the construction of four new Junior Ranks SLA bu
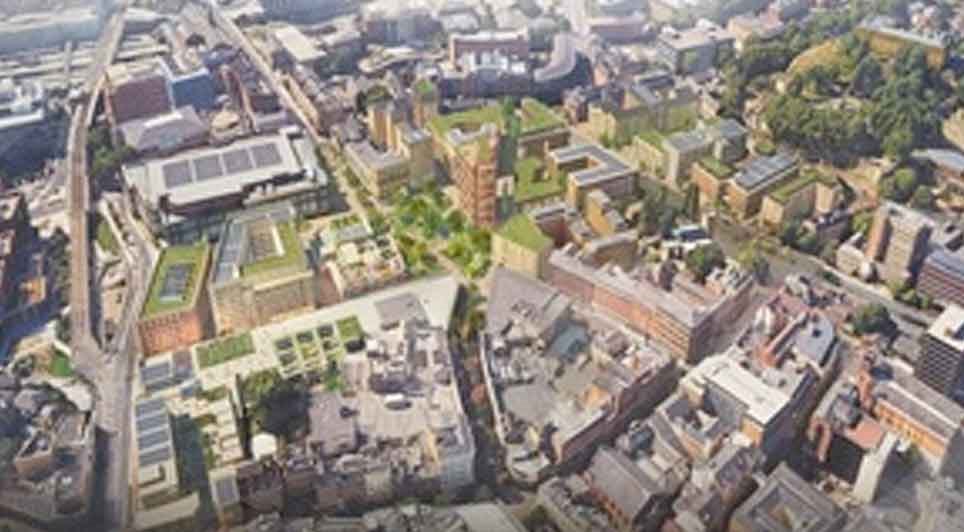
01/04/2025
The regeneration of Nottingham city centre has taken a significant step forward following an agreement for Homes England to acquire the Broad Marsh site from Nottingham City Council.
As the Government's housing and regeneration agency, Homes England will take ownership of the former shopping centre