Castle & Pryor use diamond blades for cutting because they are cost effective, accurate, and safe.
Diamond tipped blades can be used on a variety of tooling including floor saws, track/wall saws, and hand cutters making them very versatile to meet the everyday requirements of the construction industry. The advantages of diamond cutting cementitious construction materials are many faceted in respect you can cut accurately, free of dust and vibration, by hand or using specialist machinery to suit the task at hand.
Large or small sections of concrete or masonry can be isolated or removed in situ without disturbing the remaining structure making modification or refurbishments works easier to carry out. All sections can be cut to size to accommodate weight restrictions or size to suit site ergonomics upon removal.
What are the benefits of using diamond blades?
Cost Efficiency: Although initially expensive, the longevity of diamond tools offsets the need for frequent replacements, saving costs over time.
Faster Cutting Speeds: The strength of diamonds allows for faster material removal, improving productivity in time-sensitive projects.
Minimal Downtime: The durability and sharpness of diamond tools reduce the frequency of tool changes.
Low Heat Buildup: Diamond tools can withstand high temperatures without losing their cutting edge, making them suitable for prolonged use in demanding conditions.
Low Vibration and Noise: These tools reduce vibrations and noise levels.
Less Waste: Precision cutting results in minimal material wastage.
Efficient Resource Use: Reduced material waste and the long lifespan of diamond tools contribute to a more sustainable operation.
Reliability: Their ability to handle tough materials makes them indispensable for demolition, roadwork, and structural projects.
Clean Cuts: Diamond cutting tools ensure straight, precise, and clean cuts, reducing the need for secondary adjustments or repairs.
How do diamond blades work?
Diamond blades don't technically "cut" materials, they grind through them. The embedded diamond particles induce a shearing effect which progressively wears material off.
How are diamond blades made?
Diamond saw blades are made using a specialist process that combines synthetic diamonds with a metal or resin bond to create a strong and powerful blade. The synthetic diamond crystals are stronger than natural diamonds.
The diamond particles are then exposed on the edge of the blade to cut through materials. The cut is essentially achieved thanks to the exposed diamonds on the edge of the blade slicing through the stone.
How has the manufacturing of diamond cutting blades evolved over the past 20 years?
Diamond Retention: The metal or resin bond matrix has been refined to provide better retention of diamonds, leading to longer blade life and more efficient use of diamond particles.
Higher-quality synthetic diamonds: The use of higher-grade synthetic diamonds has improved blade durability and cutting precision. Modern synthetic diamonds are engineered to have consistent shape, size, and toughness.
Micro-diamond technology: Finer diamond particles are now used in combination with coarse particles, optimising the balance between speed and precision in cutting applications.
Nanodiamonds: The integration of nanodiamonds into the bonding matrix improves cutting performance by increasing wear resistance and heat dissipation.
Auto Array: An Auto Array arranges diamond particles within the blade’s bonding matrix in a highly organised and precise manner, rather than relying on the traditional random distribution of diamonds. This innovation improves the blade’s performance, efficiency, and lifespan.
Precise Diamond Placement:
Diamonds are systematically arranged in layers or patterns within the segment to maximise cutting efficiency. These patterns are designed to ensure that:
The diamonds are uniformly distributed.
Each diamond contributes to the cutting process, minimising waste.
Cutting performance remains consistent over time as the blade wears.
Metal Bond Engineering:
Auto Array blades use advanced bonding techniques to secure the diamonds in place. These bonds are formulated to wear down at a rate that keeps fresh diamonds exposed throughout the blade's use.
Segment design: Blade segments are now designed with a range of patterns (e.g., turbo, segmented, and continuous rim designs) tailored to specific cutting needs. These designs improve debris removal, cooling, and cutting efficiency.
Cooling holes and slots: Modern blades feature precision-engineered cooling holes or slots in the steel core to enhance heat dissipation and reduce the risk of warping during heavy use.
Noise reduction: Anti-vibration cores and specialised designs reduce noise and vibration during cutting, improving safety and operator comfort.
Computerised Manufacturing: Automated systems, such as laser-guided or robotic processes, precisely position diamonds during the production of the segments. This level of precision is unattainable through traditional methods.
Material-specific blades: Manufacturers now offer a wide variety of blades tailored for cutting specific materials like concrete, asphalt, stone, ceramic, and metal. These blades are optimised for the hardness and abrasiveness of the target material.
Recycling of diamonds: Old blades are increasingly recycled to recover diamond particles, reducing waste and environmental impact.
What are the benefits of the innovations to diamond blades?
Longer blade life: Innovations in bonding materials and segment designs have significantly increased the lifespan of diamond blades.
Faster cutting speeds: Improved segment geometry and diamond grit distribution enhance the speed of cutting without compromising quality.
Thermal resistance: Advances in heat-resistant bonding materials and cooling systems have improved the blade's ability to perform under high temperatures.
What is a blade doctor?
A Diamond Blade Doctor ensures that diamond blades perform at their best while saving costs by extending their lifespan through proper maintenance and expert care. They are skilled at:
Segment Replacement: Replacing worn-out or damaged segments with new ones to restore cutting performance.
Core Straightening: Fixing warped or bent steel cores to extend the blade’s usable life.
Glazing Removal: Restoring cutting efficiency by removing glazed layers and exposing fresh diamond particles through grinding or dressing.
Re-tipping: Adding new diamond tips to segments that have been excessively worn down.
Summary
The production of diamond saw blades involves careful selection of materials, precision engineering, and stringent quality control. The result is a highly durable cutting tool capable of delivering precision and efficiency across a wide range of materials and applications, which is why Castle & Pryor choose to use Diamond Cutting Blades.
Need a price for your project? Speak to one of our team. Call 0800 163 382.
castle-pryor.co.uk
Construction News
12/03/2025
Why Do Castle & Pryor Use Diamond Blades For Cutting?
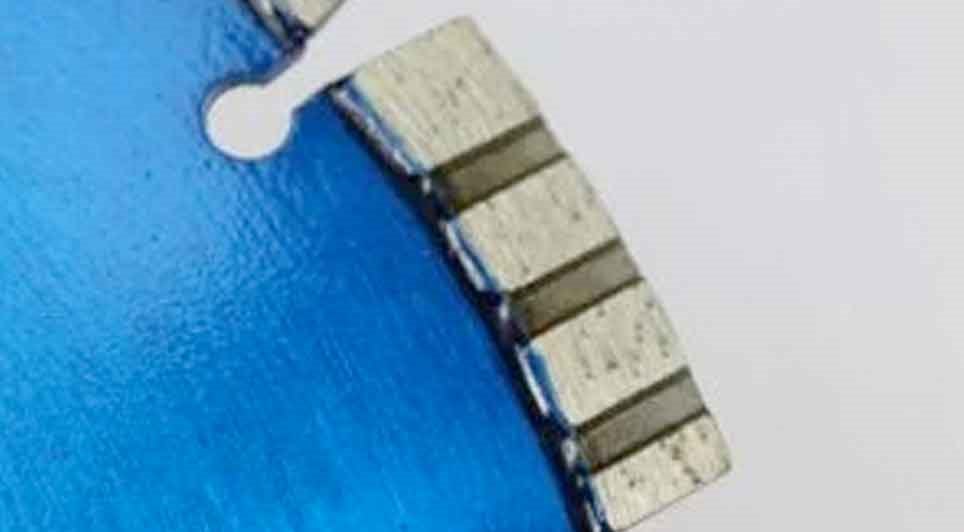
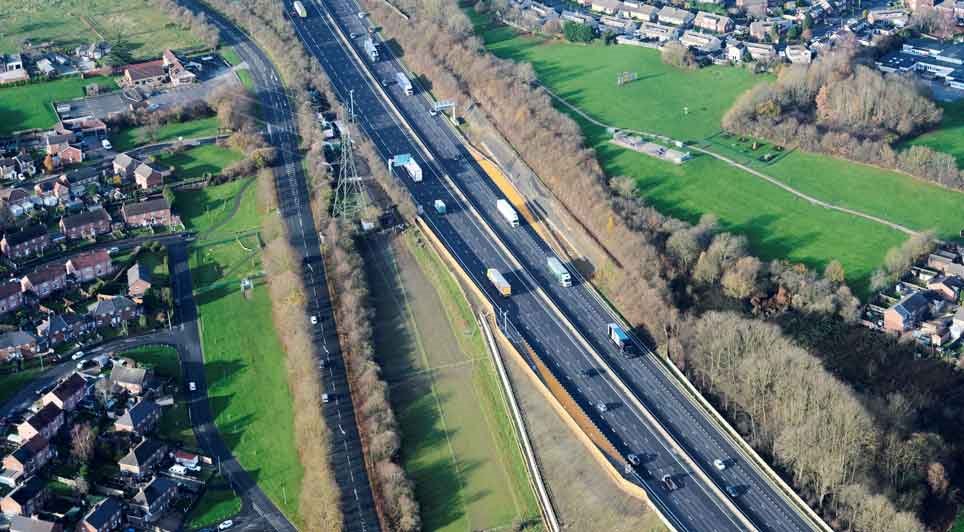
15/04/2025
Costain, working as part of the SMP Alliance, has completed the construction of 41 new emergency areas on the M1 motorway between junctions 28 and 35A, delivering the project ahead of schedule.
The newly installed emergency areas span a 32-mile stretch of motorway running from Derbyshire to South Y
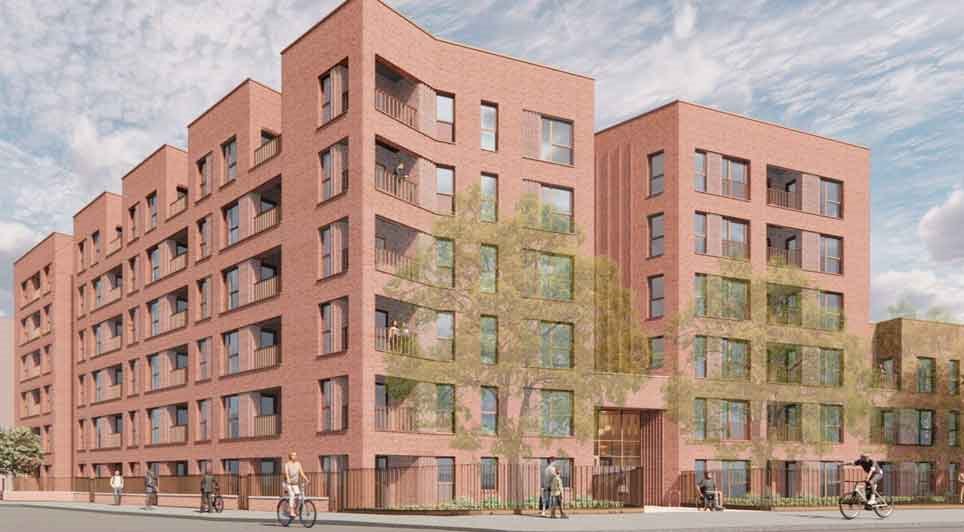
15/04/2025
Great Places Housing Group has formally submitted plans for the first development to come forward under the newly approved masterplan for the regeneration of the Grey Mare Lane neighbourhood in east Manchester.
The proposal outlines a new affordable housing scheme comprising 82 apartments for socia
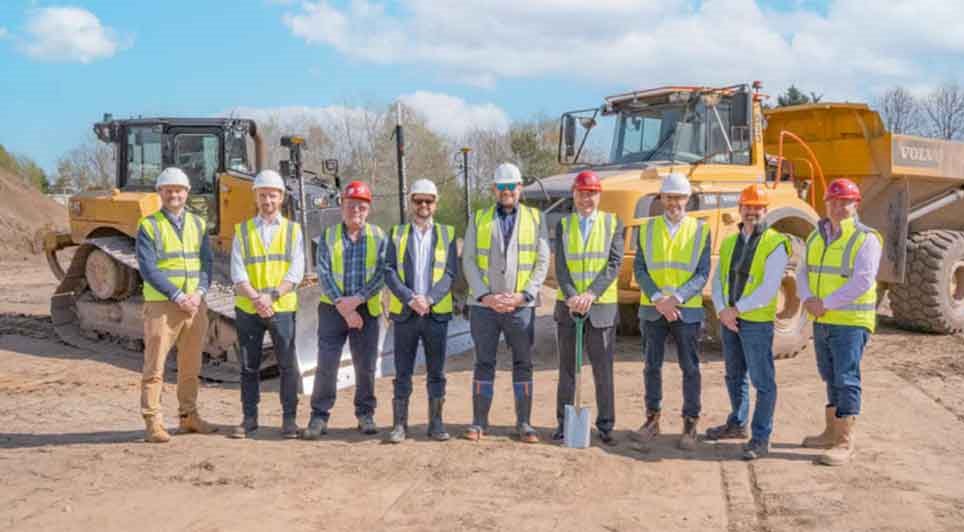
15/04/2025
Construction has officially begun on a £20 million speculatively developed industrial and logistics unit at Tournament Fields Business Park in Warwick.
Barberry Industrial, the commercial property developer and investor behind the project, announced that Bromsgrove-based contractor Benniman has bee
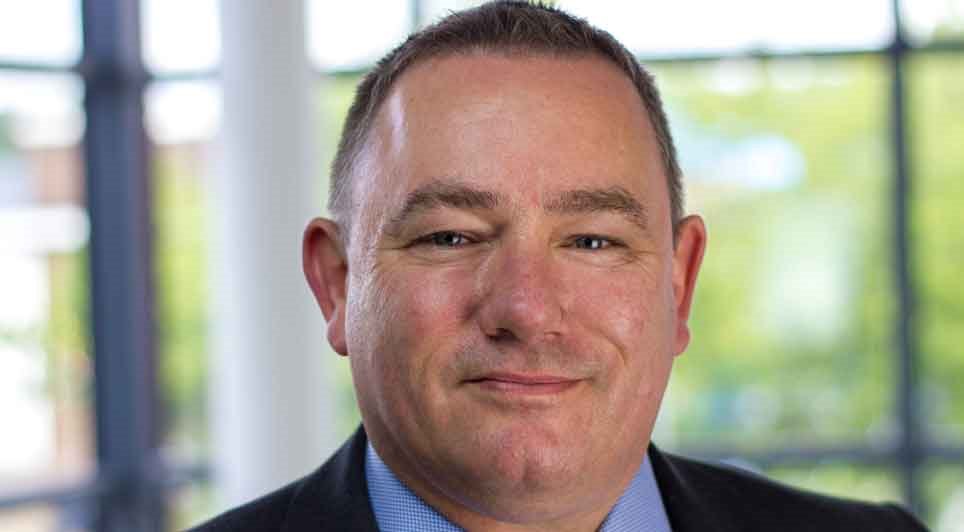
15/04/2025
Caddick Construction Group has posted robust financial results for the year ending 31 August 2024, with annual turnover reaching £356 million, marking a 12% increase on the previous year.
The figures highlight the company's commitment to sustainable growth and reinforce a positive outlook for the
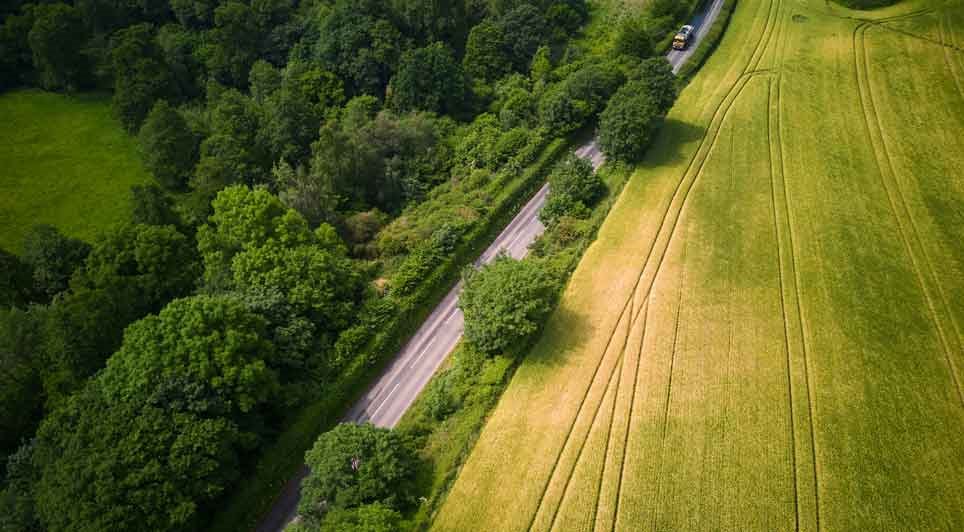
15/04/2025
Shropshire Council has appointed Kier to deliver highways maintenance services for an additional year. This extends the contractor's existing seven-year contract, which began in 2018, through to April 2026.
Kier is responsible for planned and responsive highways works and major projects across Shr
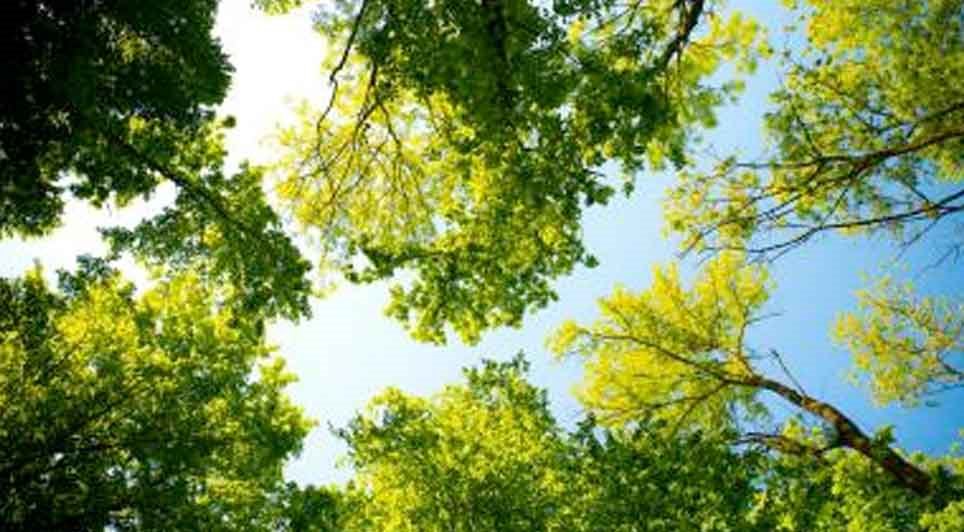
15/04/2025
City of Wolverhampton Council is set to begin work on a ground-breaking neighbourhood pilot aimed at cutting carbon emissions, lowering energy costs, and improving public health following a successful funding bid.
The council has secured £545,502 from the West Midlands Combined Authority's Net Zero
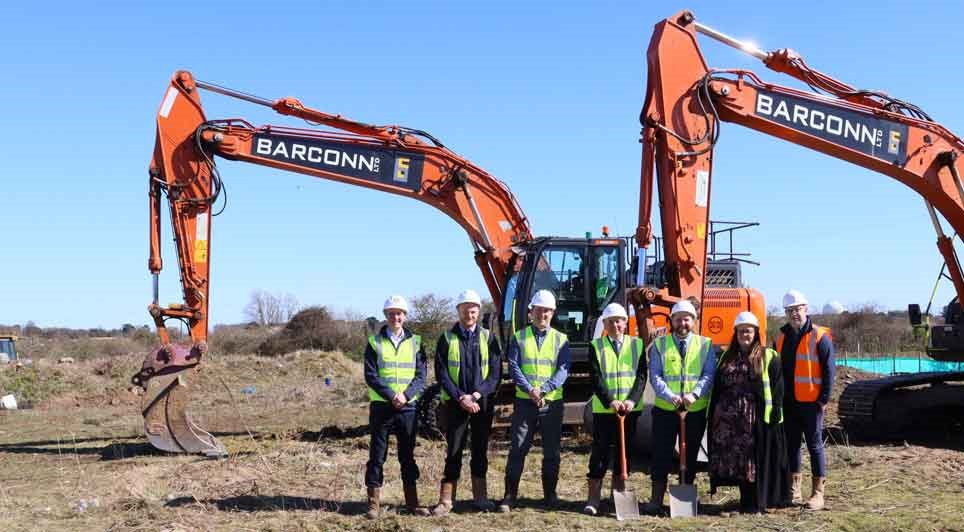
15/04/2025
A disused brickwork site in Leiston is to be transformed as Persimmon Homes has officially broken ground on a new 97-home development, following planning approval from East Suffolk Council.
The project, named Aldhurst View, will deliver a mix of one- to five-bedroom homes, with 32 of the properties
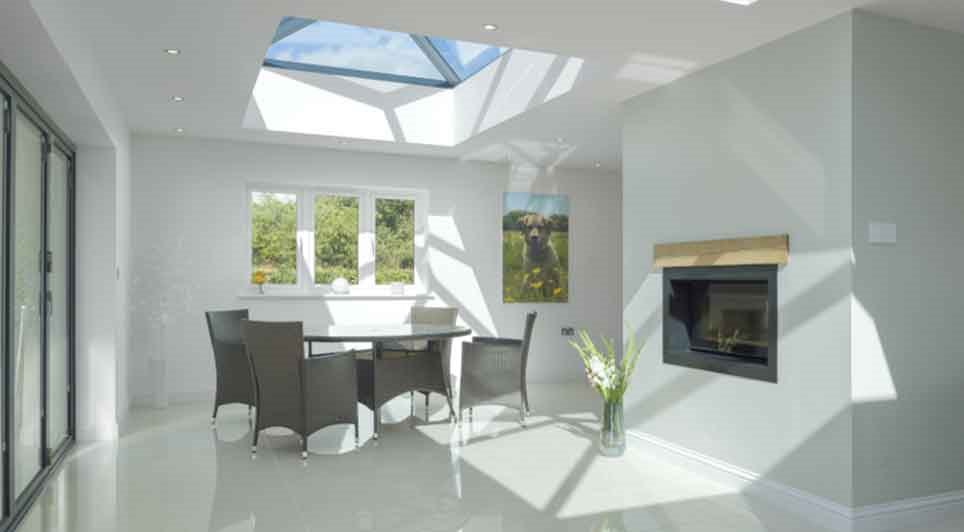
15/04/2025
Roof lanterns are one of the star players in the world of skylights, bringing a touch of glamour and luxury to a growing number of homes across the UK.
If you have one at the top of your wish list, we're here to help with expert advice, top brand rooflights and a roof lantern buyer's guide to ligh
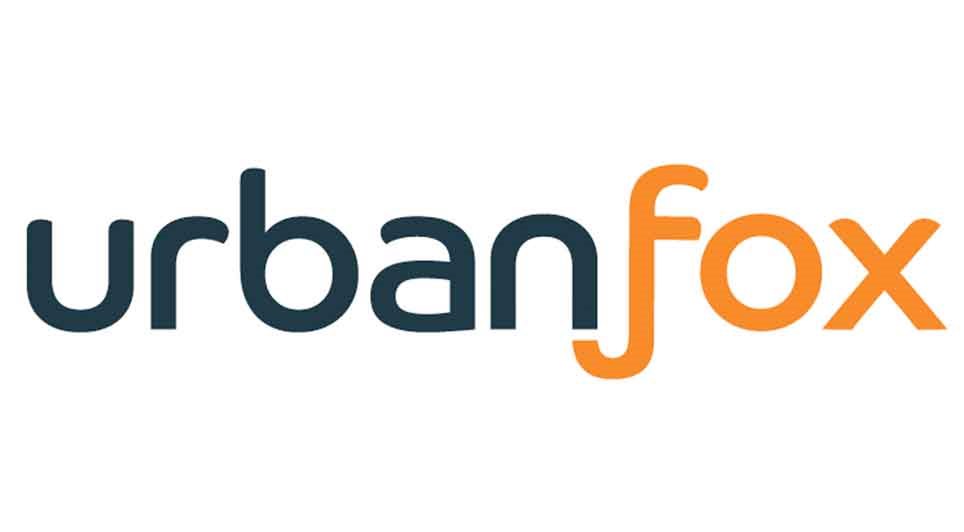
15/04/2025
Urban Fox, a joint venture between Balfour Beatty Investments and Urban Electric Networks, has secured its first-ever contract with Newport City Council to install one of the first lamp post electric vehicle (EV) charging networks in Wales.
The initiative marks a significant step forward in both t
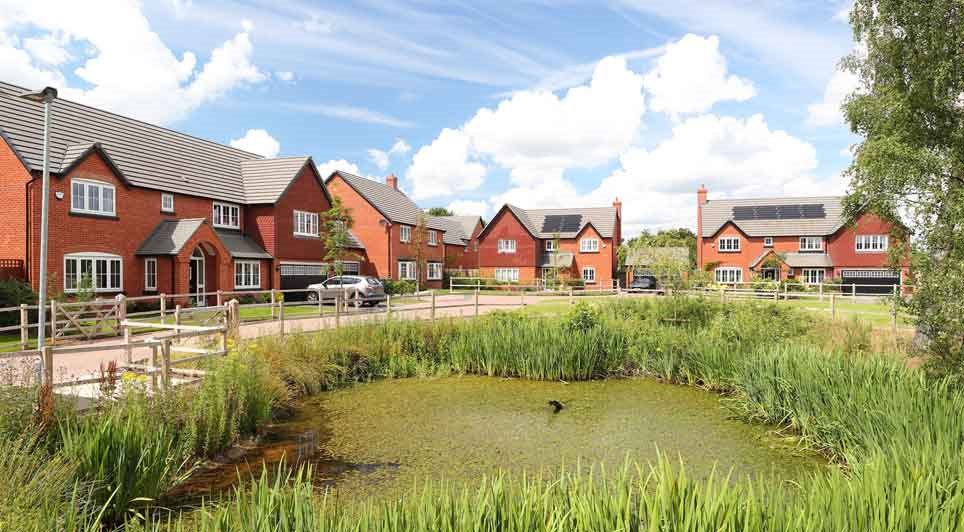
14/04/2025
Elan Homes is preparing to start work on a 110-home scheme in the Warrington village of Hollins Green.
The Cheshire-based business recently acquired a 10.5-acre site off Manchester Road.
The land was allocated for housing in the Warrington Local Plan 2021/22 to 2038/39, which was adopted in Decemb