As one of the UK's leading rubber moulding companies, we understand the importance of incorporating the right components into your designs to ensure optimal performance, safety, and longevity.
One such crucial element that is often overlooked is the humble rubber grommet. However, custom rubber grommets can be the unsung heroes of your product, providing a range of benefits that can truly elevate your design.
In this article, we explore in detail custom rubber grommets, explore into their significance, the various types available, and how they can be seamlessly integrated into your product design to enhance efficiency and safety. Whether you’re an engineer, a manufacturer, or a designer, this guide will equip you with the knowledge to make informed decisions and unlock the full potential of custom rubber grommets.
Understanding the Importance of Custom Rubber Grommets in Product Design
Rubber grommets are often the unsung heroes of product design, serving as crucial interface points between different components or materials. They play a vital role in protecting wires, cables, and other sensitive elements from abrasion, wear, and tear, ensuring the overall integrity and longevity of your product.
However, off-the-shelf grommets may not always be the best fit for your specific design requirements. That’s where custom rubber grommets come into play. By tailoring the size, shape, material, and other specifications to your unique needs, you can unlock a world of advantages that can transform your product’s performance and user experience.
Benefits of Using Custom Grommets
Improved Fit and Functionality: Custom rubber grommets are designed to seamlessly integrate with your product's specific dimensions and requirements, ensuring a perfect fit and optimal functionality.
Enhanced Safety: Customised grommets can provide superior protection for cables, wires, and other sensitive components, reducing the risk of damage and potential safety hazards.
Increased Durability: By selecting the appropriate materials and design, custom rubber grommets can withstand the rigours of your product’s operating environment, extending its lifespan and reducing maintenance costs.
Aesthetic Appeal: Customised grommets can be designed to complement the overall aesthetic of your product, contributing to a cohesive and visually appealing design.
Cost-Effectiveness: While the initial investment in custom grommets may be slightly higher, the long-term benefits and reduced maintenance costs can make them a more cost-effective solution in the grand scheme of your product’s lifecycle.
Versatility: Custom rubber grommets can be tailored to a wide range of applications, from electrical and electronics to automotive, industrial, and beyond, making them a versatile solution for diverse product designs.
Different Types of Custom Grommets and Their Applications
Custom rubber grommets come in a variety of shapes, sizes, and materials, each suited to specific applications and requirements. Some of the most common types include:
Flat Grommets: Ideal for sealing openings in flat surfaces, such as panels or enclosures, to protect against moisture, dust, and other environmental factors.
Flanged Grommets: Designed with a flange or lip, these grommets provide a secure seal and are commonly used in applications where the grommet needs to be mounted or secured to a surface.
Stepped Grommets: Featuring a stepped design, these grommets are used to accommodate different hole sizes or thicknesses, ensuring a tight and reliable fit.
Conical Grommets: With a tapered or conical shape, these grommets are well-suited for applications where the hole size varies or where the grommet needs to be inserted into a pre-drilled opening.
Split Grommets: Designed with a split or slit, these grommets allow for easy installation around existing cables or wires, making them a convenient choice for retrofitting or maintenance tasks.
Specialty Grommets: Customised grommets can be designed to meet specific requirements, such as high-temperature resistance, chemical compatibility, or unique shapes and sizes to accommodate complex product designs.
The choice of custom rubber grommet type will depend on the specific needs of your product, including the size and shape of the openings, the environmental conditions, and the level of protection required.
Factors to Consider When Choosing Custom Rubber Grommets
When selecting custom rubber grommets for your product design, there are several key factors to consider:
Material Compatibility: Ensure that the grommet material is compatible with the surrounding components and the operating environment of your product. Common materials include nitrile, silicone, EPDM, and neoprene, each with its own unique properties and performance characteristics.
Size and Dimensions: Carefully measure the openings in your product and select grommets that provide a secure and snug fit, preventing any gaps or leaks.
Environmental Conditions: Consider the temperature range, exposure to chemicals, UV radiation, or other environmental factors that the grommets will need to withstand.
Compression and Sealing Requirements: Determine the level of compression and sealing needed to protect sensitive components, and choose grommets with the appropriate hardness and compression characteristics.
Regulatory and Safety Standards: Ensure that the custom rubber grommets comply with any relevant industry standards or regulations, such as those related to electrical safety, food-grade applications, or automotive requirements.
Cost and Lead Time: Evaluate the cost implications of custom grommets and balance them against the long-term benefits, while also considering the lead time required for manufacturing and delivery.
By carefully evaluating these factors, you can select the most suitable custom rubber grommets for your product design, optimising performance, safety, and cost-effectiveness.
How to Incorporate Custom Rubber Grommets into Your Product Design
Integrating custom rubber grommets into your product design is a straightforward process that can yield significant benefits. Here’s a step-by-step guide:
Identify the Grommet Locations: Carefully review your product design and identify all the areas where grommets will be needed, such as cable/wire entry points, mounting holes, or other openings.
Determine the Grommet Specifications: Based on the factors discussed earlier, determine the required size, shape, material, and other specifications for each grommet location.
Design the Grommet Openings: Ensure that the openings in your product are appropriately sized and shaped to accommodate the selected custom grommets, allowing for a secure and reliable fit.
Incorporate Grommet Mounting Considerations: Depending on the grommet type, plan for the necessary mounting features, such as flanges or snap-fit mechanisms, to ensure a secure and stable installation.
Evaluate the Overall Design: Review the integrated custom rubber grommets to ensure they align with the product’s aesthetic, functional, and safety requirements.
Collaborate with Grommet Suppliers: Work closely with reliable custom grommet suppliers to finalise the design, obtain samples, and ensure a seamless integration into your product's manufacturing process.
By following this step-by-step approach, you can effectively incorporate custom rubber grommets into your product design, optimising performance, safety, and overall product quality.
Rubber Grommet Manufacturing Process
The manufacturing of custom rubber grommets involves a multi-step process that ensures the final product meets your specific requirements. Here’s a general overview of the process:
Design and Engineering: Based on your product design and specifications, the grommet supplier will work with you to finalise the size, shape, material, and other key characteristics of the custom rubber grommets.
Mould Fabrication: The supplier will create a custom mould that matches the desired grommet design, ensuring precise dimensions and tolerances.
Rubber Compounding: The appropriate rubber compound, such as nitrile, silicone, or EPDM, is carefully selected and compounded to meet the performance requirements of your application.
Injection Moulding: The rubber compound is then injected into the custom mould, where it is cured and formed into the desired grommet shape.
Finishing and Inspection: The moulded grommets undergo a series of finishing processes, such as trimming, deburing, and quality inspections, to ensure they meet the specified standards.
Packaging and Delivery: Finally, the custom rubber grommets are carefully packaged and delivered to you, ready for integration into your product design.
Throughout this process, the grommet supplier will collaborate closely with you to address any design changes, ensure compliance with relevant standards, and provide ongoing support to ensure a seamless integration into your manufacturing workflow.
Where to Find Reliable Suppliers of Custom Grommets
Identifying a reliable supplier of custom rubber grommets is crucial to the success of your product design. Here are some tips to help you find the right partner:
Industry Reputation and Experience: Look for suppliers with a proven track record of delivering high-quality custom rubber grommets to clients in your industry. Assess their technical expertise and capabilities.
Customisation and Flexibility: Evaluate the supplier’s ability to accommodate your unique design requirements, material preferences, and production timelines. A flexible and responsive partner can make all the difference.
Quality Assurance and Compliance: Ensure that the supplier has robust quality control measures in place and can provide the necessary certifications or compliance documentation.
Collaborative Approach: Choose a supplier who is willing to work closely with you throughout the design, prototyping, and production phases, providing valuable insights and recommendations to optimise your grommet solution.
By carefully vetting and selecting a reliable custom rubber grommet supplier, you can ensure a seamless integration of these crucial components into your product design, ultimately enhancing its performance, safety, and overall success in the market.
Conclusion: Enhance Your Product Design with Custom Grommets
In the world of product design, the unsung heroes are often the smallest components, and custom rubber grommets are a prime example. By understanding the importance of these versatile elements and incorporating them strategically into your designs, you can unlock a world of benefits that will elevate your products’ efficiency, safety, and longevity.
Whether you're an engineer, a manufacturer, or a designer, we hope this guide has equipped you with the knowledge and insights to make informed decisions about custom rubber grommets. By partnering with reliable suppliers and leveraging the full potential of these customised solutions, you can create products that truly stand out in the market and exceed your customers’ expectations.
For more information about custom rubber grommets or to discuss your requirements contact our team of experts today. Together, we’ll design a tailored solution that enhances your product’s performance, safety, and overall success.
Construction News
28/04/2025
Enhance Efficiency And Safety With Custom Rubber Grommets
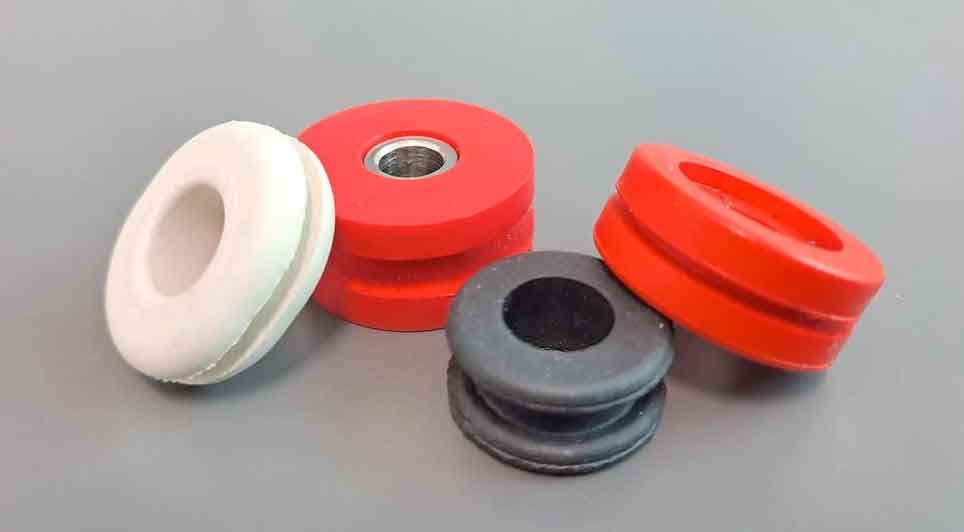
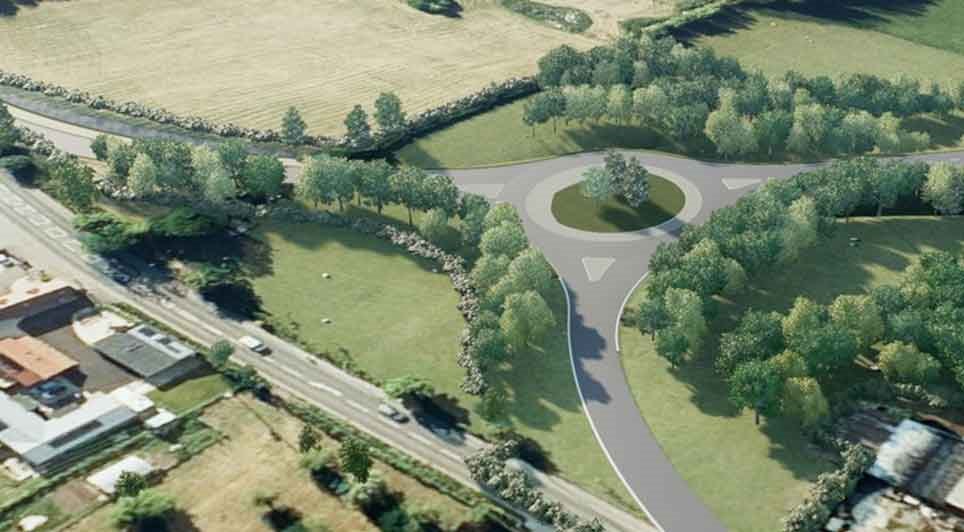
28/04/2025
Galliford Try has announced that its Infrastructure business has been appointed to deliver the Banwell bypass project in North Somerset, under a contract worth £66.5 million.
Commissioned by North Somerset Council and funded through the Homes England Housing Infrastructure Fund, the project was sec
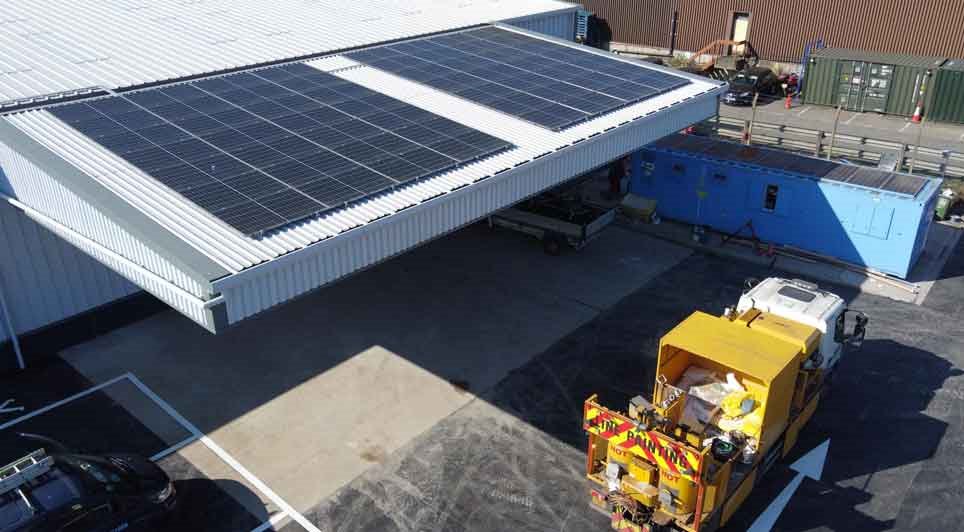
28/04/2025
Willmott Dixon has redeveloped the Therapia Lane Depot in Sutton, transforming a disused industrial site into a modern facility that supports the borough's environmental ambitions.
The new depot now serves as the base for all of Sutton's waste collection and street cleaning vehicles. It features 11
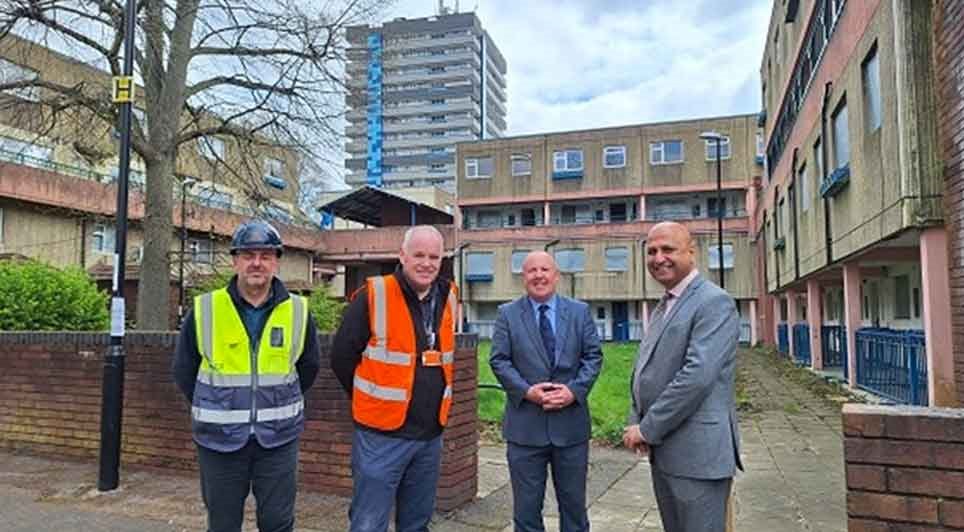
28/04/2025
Demolition work has officially started on three tower blocks in Coventry's Spon End, marking a significant milestone in the area’s major regeneration project.
The 1960s-built blocks, Kerry House, Milestone House, and Trafalgar House, are being taken down by housing association Citizen, working in p
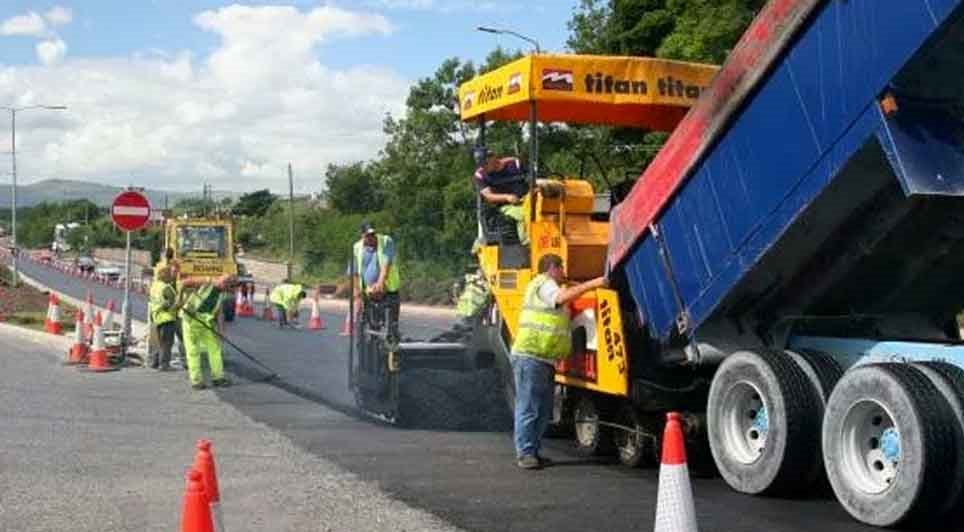
28/04/2025
A major £180,000 highways improvement scheme has begun in Stafford.
The project involves the reconstruction and resurfacing of the A5187 Station Road, including work on the approaches and exits of the Station Road/Railway Street and Victoria Road roundabout. Crews will also be repairing damaged iro
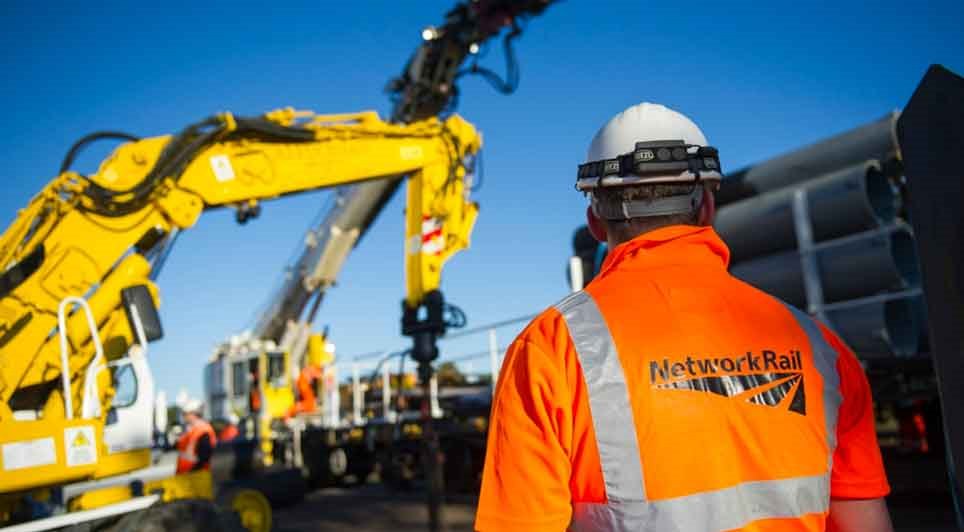
28/04/2025
Network Rail is set to carry out more than 630 projects across Britain's railway network during the early and late May Bank Holidays, aiming to deliver key infrastructure improvements while keeping most services running as normal.
The quieter bank holiday weekends, particularly on major commuter ro
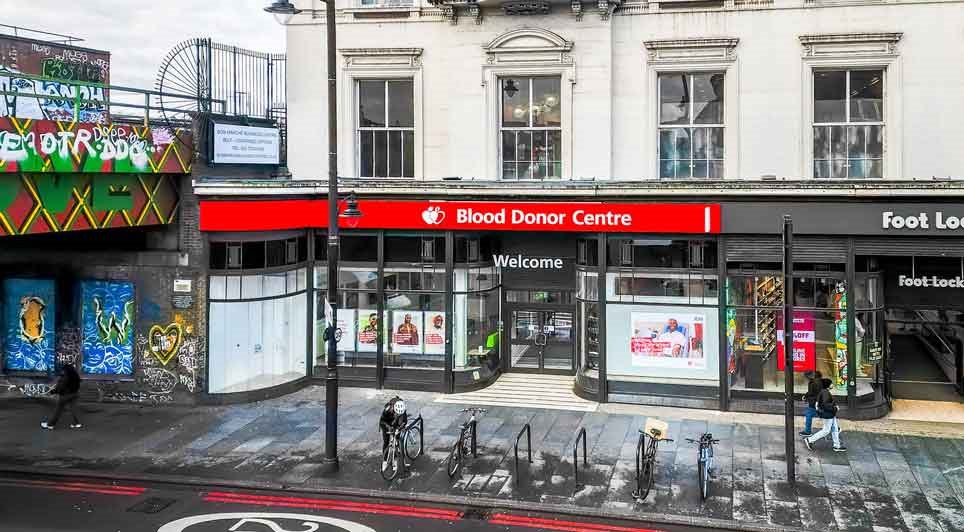
28/04/2025
A new blood donation centre has completed in South London, boosting community engagement and playing a key role in combatting sickle cell disease.
The first permanent NHS Blood and Transplant donor centre in Brixton, converted from an unused retail unit, has been completely refitted with nine donor
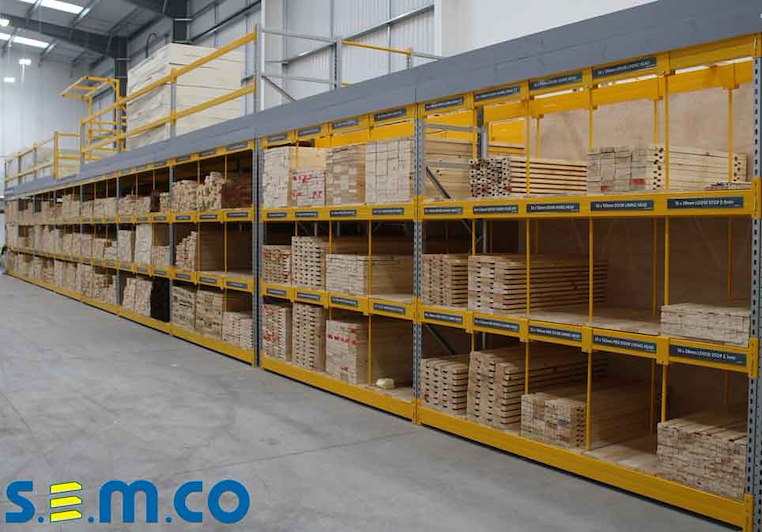
28/04/2025
S.E.M.CO specialises in bespoke racking for timber merchants, manufacturing and supplying directly from its purpose-built facility in Cannock, Staffordshire, and are truly experts in the f
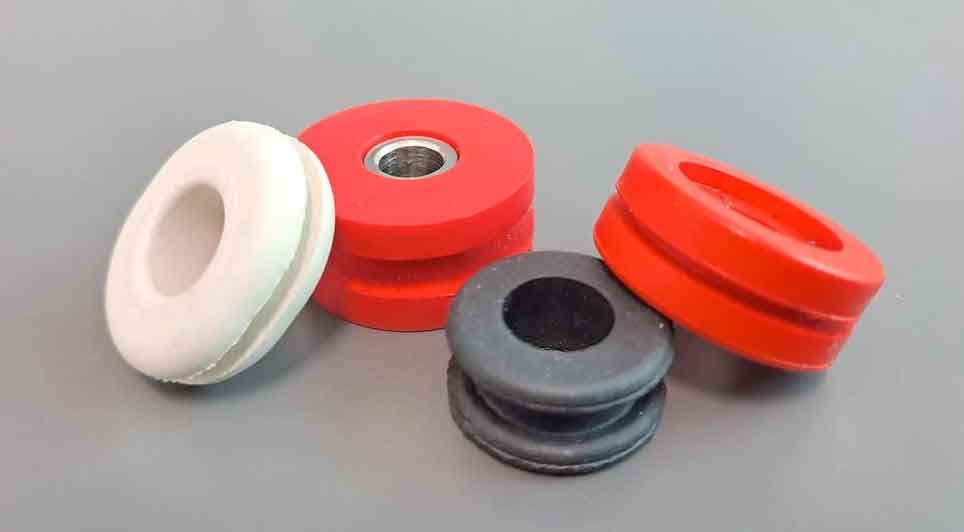
28/04/2025
As one of the UK's leading rubber moulding companies, we understand the importance of incorporating the right components into your designs to ensure optimal performance, safety, and longevity.
One such crucial element that is often overlooked is the humble rubber grommet. However, custom rubber gr
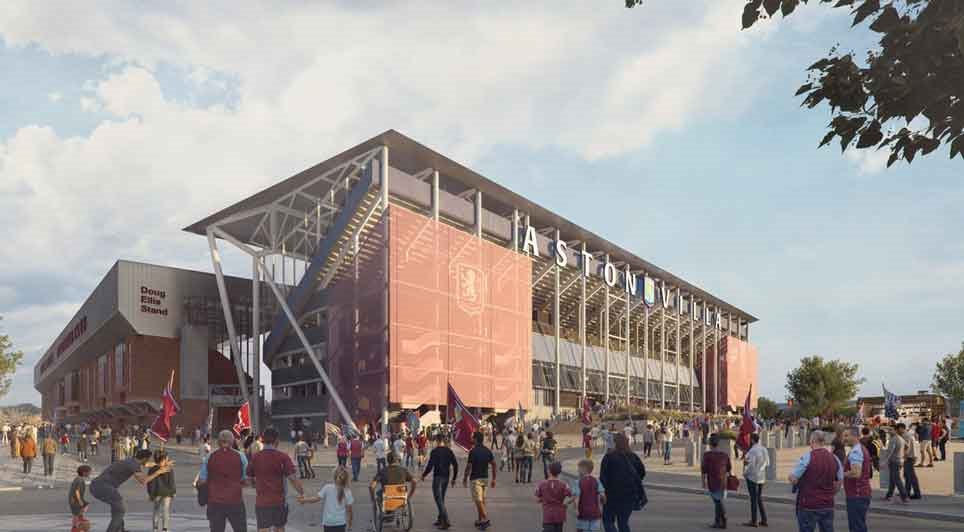
25/04/2025
Aston Villa Football Club has unveiled plans to refurbish and expand the iconic North Stand at Villa Park, a major step in the wider regeneration of the North Grounds.
The redevelopment will raise the stadium's total capacity to over 50,000, with the North Stand alone increasing to more than 12,00
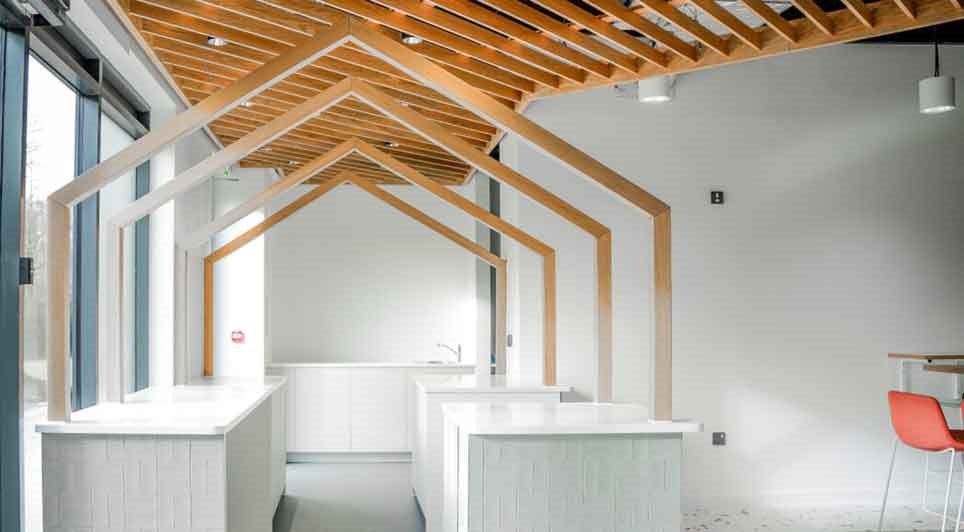
25/04/2025
Morgan Sindall Construction's Southern Home Counties team has officially handed over the newly completed Crawley Innovation Centre to Crawley Borough Council (CBC).
The transformation of the former TUI travel house into a cutting-edge innovation, economic and technology hub drew local leaders, busi