In the construction industry stampede to meet the requirements of the new building regulations which came into force in May this year, timber frame companies could be fairly relaxed.
Among these companies, Scotframe, the privately-owned manufacturer and supplier could afford to be more relaxed than most. The reason is that timber frame homes already meet most of the thermal value and energy efficiency requirements in the new regulations. This is a fundamental reason that they are so popular. It is clearly recognised by developers and small to medium-sized builders that proving their green credentials makes good business sense.
Scotframe has increasingly become a market leading business in the sector since its approach has always stressed the importance of going out of its way to exceed - not simply to meet - the expectations of regulators and clients alike.
The company insists on using 45mm thick wood on the basic external and internal timbers rather than the 38mm employed by most of its competitors, on the grounds that it provides a more stable, rigid and true construction - and demonstrates that paring costs to the bone does not provide best value.
In the same spirit, Scotframe is now proposing a new suite of products which will not just jump the bar of the new regulations, but clear it substantially. The new range of modified wall construction products, which will be available shortly, will provide industry-beating thermal efficiency and remarkable u-values.
The fact is that it makes sense to cut energy emissions in the building of new homes, which account for more than a quarter of all the UK’s carbon emissions. The regulations aim to address the issue of poorly-performing windows and doors and inferior building materials which allow energy to “leak” from homes.
Tests are now recommended on all new-build residential properties to determine how airtight they are by checking for “leaks” from gaps and cracks in floors, walls, windows and doors. Increasingly, developers are using the new recommendations to their commercial advantage and providing air energy efficiency ratings as a marketing tactic with energy conscious buyers. Clearly, the higher the ratings, the lower the energy bills.
From an environmental perspective, timber frame homes start with the advantage of being constructed from a renewable resource - forestry interests in the developed world have taken the green message on board and, as a rough rule, three trees are planted for every one that is felled.
It also avoids the energy intensive nature of the materials used in traditional brick and block construction, where non-renewable aggregate has to be laboriously recovered and then made into building blocks in a process so energy wasteful that it leaves environmentalists ashen-faced.
Timber frame ticks the right boxes for speed of construction as well. Once the shell, or skeleton, of the house is wind and watertight, it can be roofed and the internal trades can get about their business. In fact, a timber frame home can be virtually finished inside before the external leaf is applied. This means that weather need no longer delay projects and important quality, efficiency and health and safety benefits are gained
Last year, a National Audit Office report into modern methods of construction concluded that timber frame construction - often thought to be more expensive than traditional methods - actually delivers a financial saving to both public and private sector of up to £35 a square metre.
This confirms that timber frame competes not only on environmental but on cost grounds, particularly in more developed markets such as Scotland - and this does not take into account the effect inexorably rising fuel costs is having on brick and block production.
The timber frame industry is nowhere near as dependent on fossil fuels. More than 70 per cent of the energy used in making wood products in the UK comes from wood residues and recovered wood. Through effectively recycling its own waste, the timber industry is helping keep both manufacturing and environmental costs as low as possible.
At Scotframe, which operates across the UK and Ireland from its bases in Inverurie near Aberdeen, Cumbernauld near Glasgow and Hillsborough in Northern Ireland, its management team’s aim is to be at the forefront of product quality and innovation in timber frame. More than 200 are employed and turnover is in excess of £35m.
With its philosophy of going the extra mile for its customers, as well a being continually aware of the environmental impact of its activities, the company is well placed within the industry for future and long-term growth.
(CD)
Construction News
21/09/2007
Timber Frame Plays Its Part In Making Construction Even More Energy Efficient
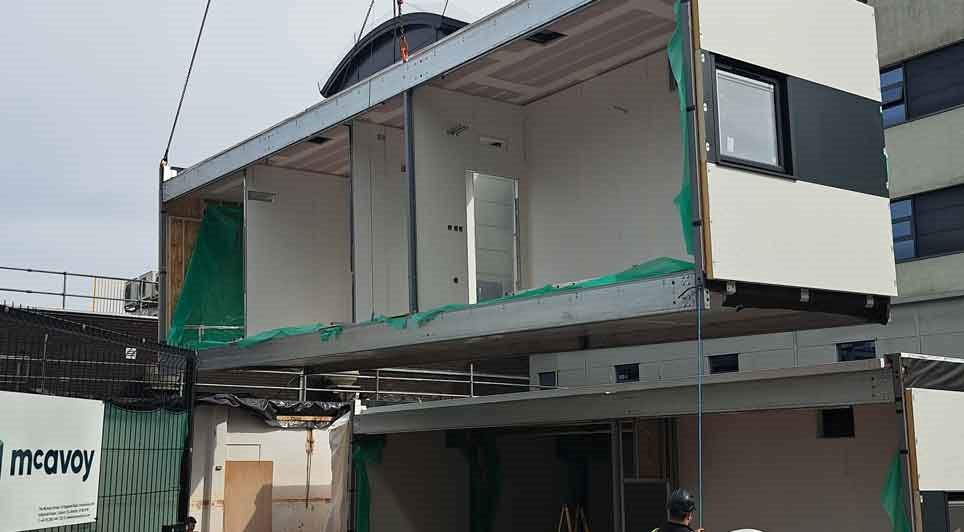
08/05/2025
McAvoy, in partnership with University Hospitals Birmingham NHS Foundation Trust, has reached a key sustainability milestone by achieving zero landfill waste during the construction of a new Medical Assessment Unit (MAU) extension at Good Hope Hospital in Birmingham.
The construction project, which
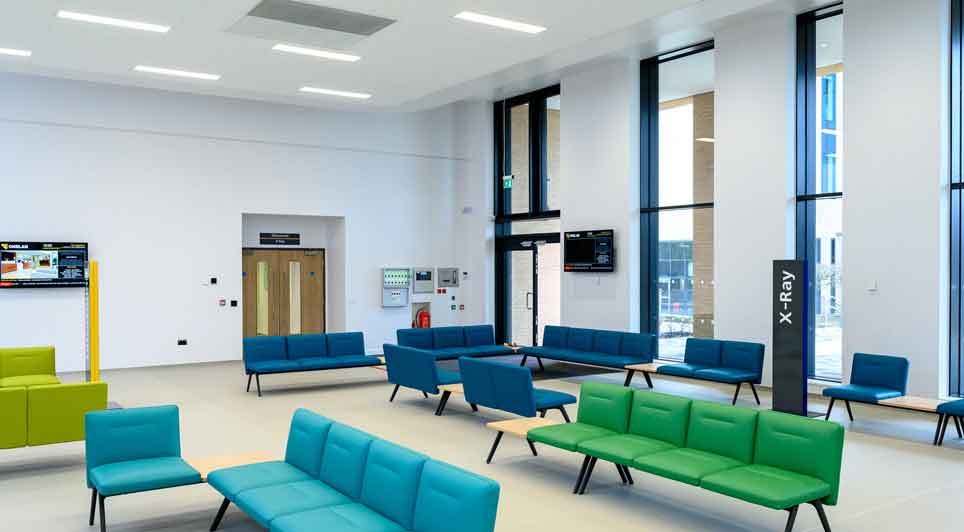
08/05/2025
A £25 million Community Diagnostic Centre at Norfolk and Norwich University Hospital (NNUH) was officially opened in late April by His Majesty's Lord-Lieutenant of Norfolk, The Lady Dannatt MBE, marking a major milestone in the delivery of modern healthcare services across Norfolk and Waveney.
The
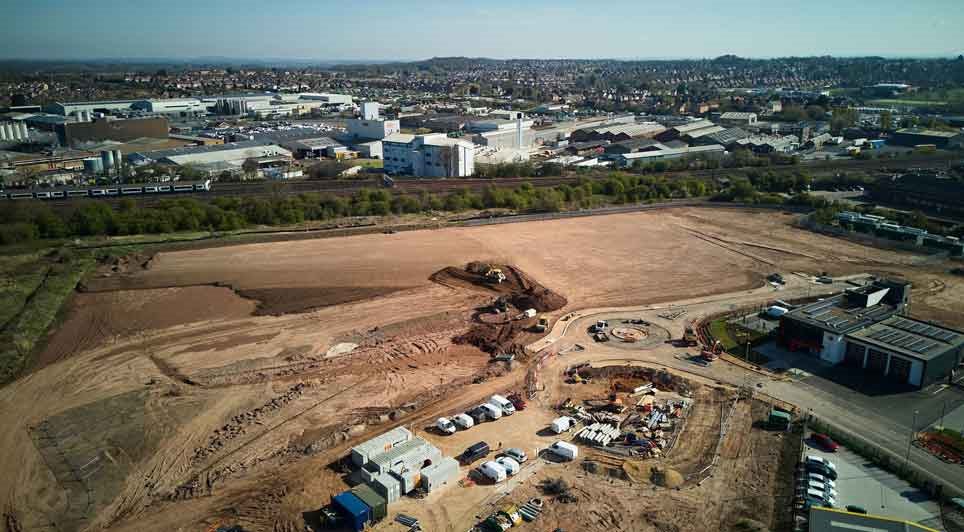
08/05/2025
Caddick Civil Engineering Ltd has completed a £2 million construction contract at the Vesuvius site in Worksop.
Commissioned by property investment and development company CEG, the infrastructure works included the extension of the existing spine road, construction of a new roundabout, and full uti
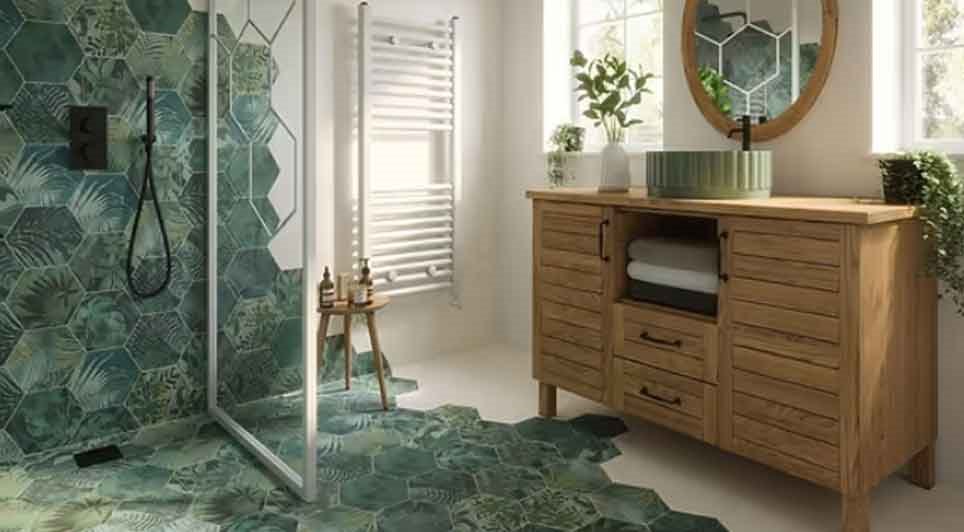
08/05/2025
Hyperion Tiles is a trusted, independent, family-run business dedicated to helping you transform your home into a space of beauty and style.
We offer a stunning selection of Porcelain Tiles,
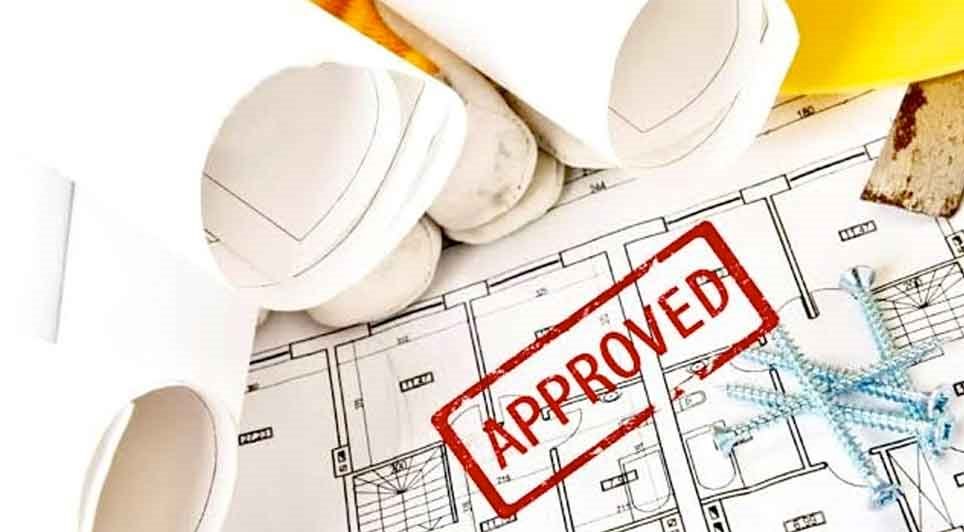
08/05/2025
West Lancashire Borough Council has officially approved the Skelmersdale Masterplan, a landmark decision that sets in motion a long-term regeneration strategy aimed at revitalising the town through economic growth, improved transport and community-focused development.
The Masterplan was approved at
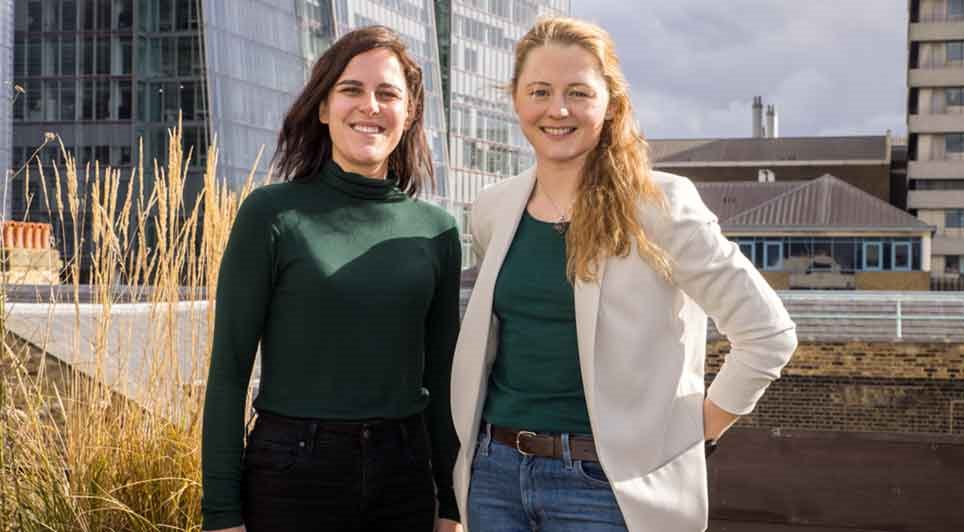
08/05/2025
Qualis Flow (Qflow), the award-winning construction technology company whose instant on-site data capture delivers transformative industry insight, has been honoured with the King's Award for Innovation, the UK's most prestigious recognition for pioneering excellence in business.
Founded in 2018 to
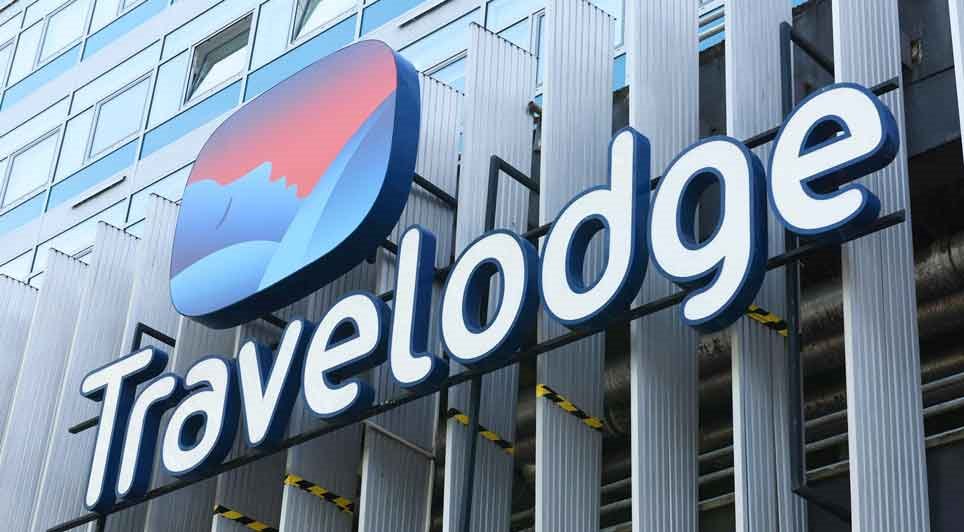
08/05/2025
Travelodge has exchanged contracts to develop a new 89-room hotel at the Goods Yard regeneration scheme in Bishop's Stortford.
The planned hotel will showcase Travelodge's latest premium design, including a contemporary reception area and next-generation rooms aimed at providing a comfortable stay
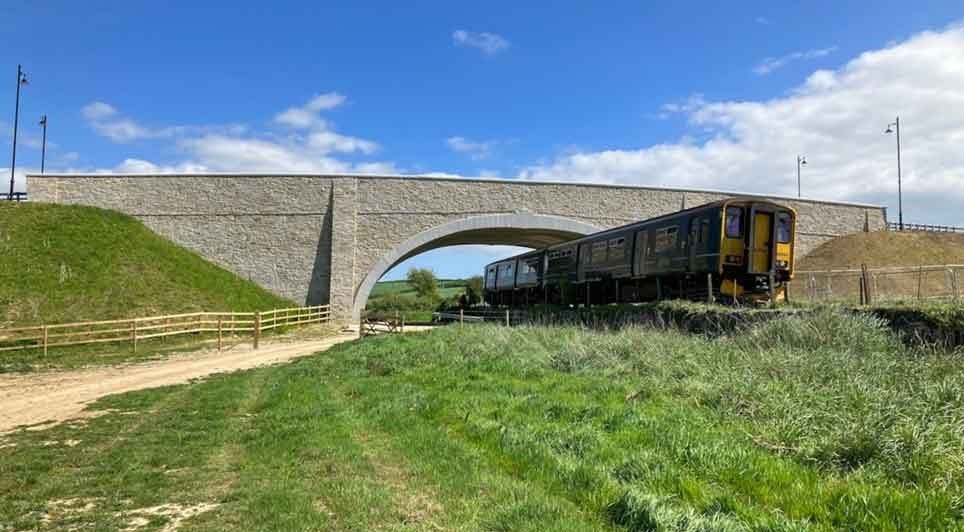
08/05/2025
A major new road scheme designed to improve transport links and unlock long-term economic growth in Newquay has officially opened to the public, with Network Rail’s newly completed railway bridge now in full operation.
The Newquay Strategic Route, developed in partnership by the Duchy of Cornwall a
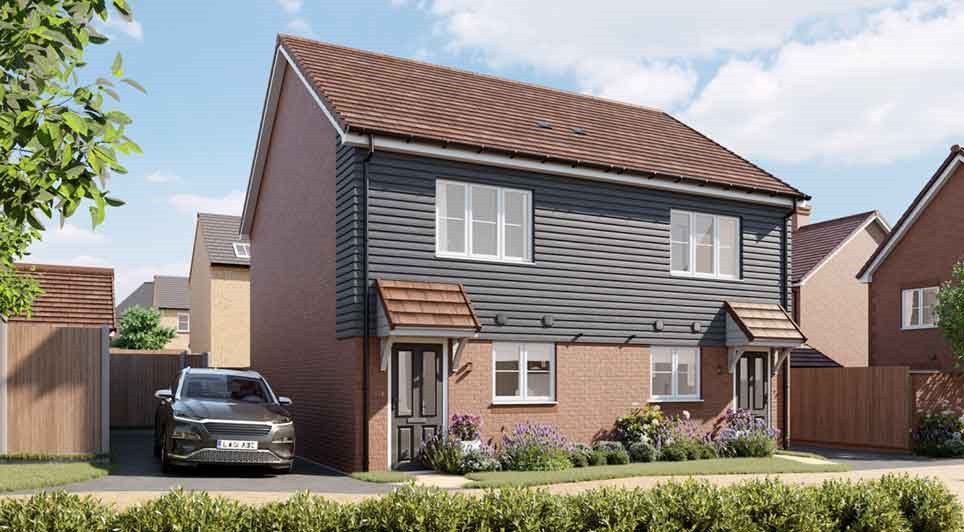
08/05/2025
Leaf Living and Vistry Group have marked a major milestone in their national housing partnership with the handover of their 1,000th jointly delivered home at The Burrows development in Paddock Wood, Kent.
The event was attended by Councillor Astra Birch, Cabinet Member for Housing and Communities
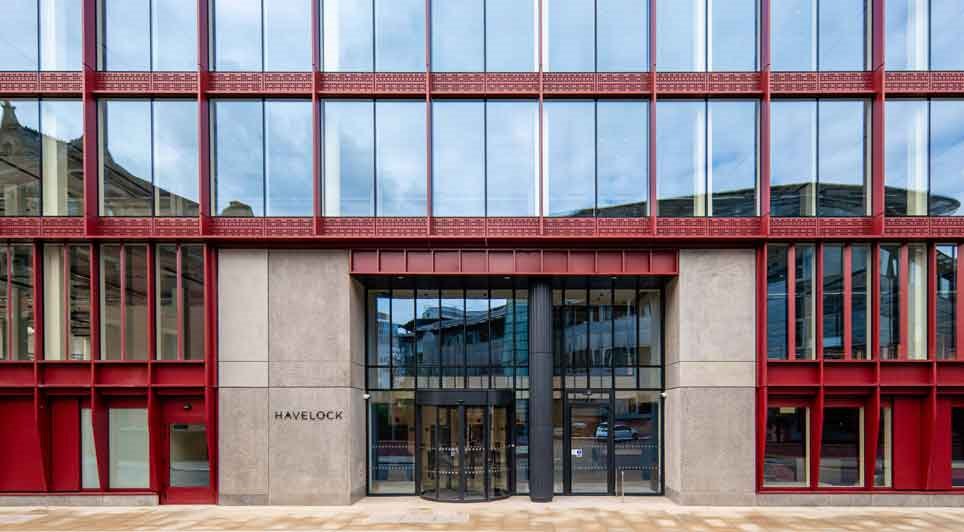
08/05/2025
Gilbert-Ash has announced that its £29 million redevelopment of Havelock House on Great Bridgewater Street, Manchester, has achieved the highly coveted 'BREEAM Outstanding' sustainability rating.
BREEAM (Building Research Establishment Environmental Assessment Method) is an internationally recognis